Prototek Unveils the World of Customized CNC Machining Parts
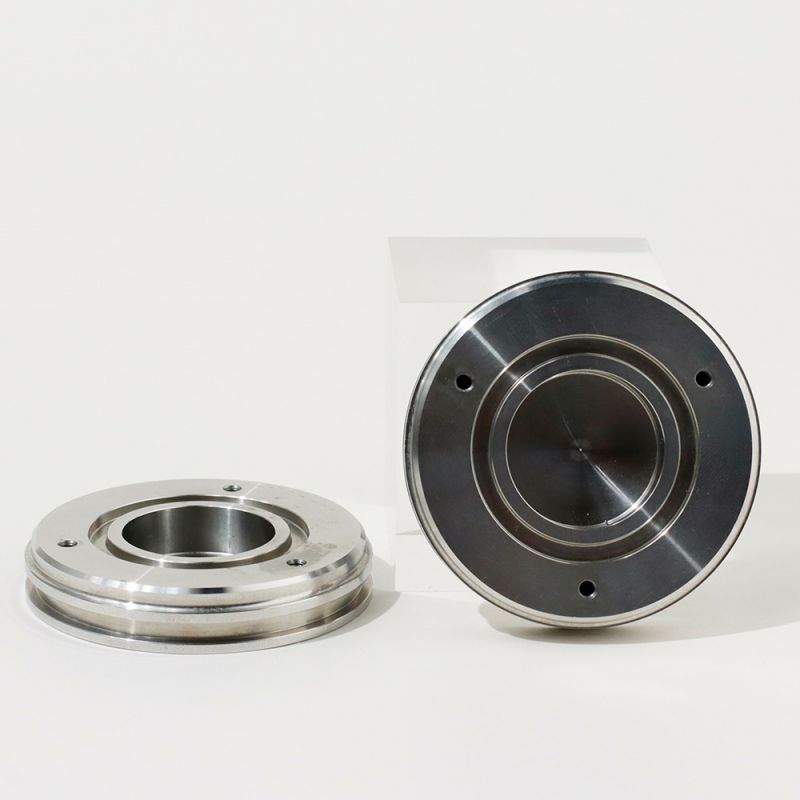
Blog Details In the dynamic landscape of manufacturing, CNC machining has emerged as a pivotal force, offering precision and efficiency in the production of components. One facet that has gained significant traction is the customization of CNC machining parts, presenting a spectrum of advantages for businesses and individuals. What is CNC Machining CNC or Computer Numerical Control, is a sophisticated manufacturing process that utilizes computerized systems to control machine tools. It involves various operations, from milling to turning, and has become ubiquitous in various industries. The Need for Customized CNC Machining Parts In the realm of modern manufacturing, the demand for customized CNC machining parts has surged, driven by the unique requirements of diverse industries and individual projects. This section delves into the multifaceted reasons behind the growing need for tailored solutions, highlights the advantages over standardized components, and explores real-world success stories that underscore the impact of customization. Reasons for the Demand The demand for customized CNC machining parts stems from the inherent diversity of projects across industries. Standardized components often fall short in meeting the specific and intricate requirements of applications ranging from aerospace and automotive to medical and electronics. Customization allows for precision engineering, ensuring that each part aligns perfectly with the unique specifications of a given project. The ability to adapt designs to specific functionalities, tolerances, and environmental conditions is a driving force behind the increasing preference for customization. Industries, especially those at the forefront of technological advancements, seek tailored solutions to stay ahead in a competitive landscape. Comparison with Standard Parts A fundamental distinction between customized CNC machining and standard parts lies in adaptability. While standard parts offer mass-produced solutions suitable for broad applications, they often require more precision and specificity for cutting-edge projects. On the other hand, customized parts are crafted with meticulous attention to detail, ensuring an exact fit for the intended purpose. This tailored approach minimizes unnecessary material usage and streamlines manufacturing, resulting in optimized performance and efficiency. Success Stories in the Industry The success stories associated with customized CNC machining parts vary across industries. 1. Aerospace Advancements In the aerospace industry, where precision and reliability are non-negotiable, customized CNC machining parts have played a pivotal role in achieving breakthroughs. Tailored components designed to withstand extreme conditions and reduce weight have enhanced fuel efficiency and overall aircraft performance. 2. Medical Marvels The demand for custom CNC parts has surged in the medical field due to the need for specialized equipment and implants. Customization allows for intricate designs that match the complexity of the human body, leading to more effective and personalized medical solutions. 3. Automotive Innovations Automotive manufacturers increasingly turn to customized CNC machining to produce components that improve vehicle performance, safety, and aesthetics. From lightweight parts for fuel efficiency to intricate designs for advanced driver-assistance systems, customization drives innovation in the automotive sector. 4. Electronics Precision In the electronics industry, where miniaturization and precision are paramount, customized CNC machining parts enable the production of intricate components for devices ranging from smartphones to sophisticated electronic systems. This level of customization ensures optimal functionality and performance in electronic applications. These success stories highlight the transformative impact of customized CNC machining parts across diverse sectors. The ability to tailor components to specific needs enhances performance, fosters innovation, and pushes the boundaries of what is achievable in manufacturing. In conclusion, the burgeoning need for customized CNC machining parts is a testament to the evolving landscape of modern manufacturing. As industries continue to advance, customization becomes increasingly pivotal, offering a pathway to innovation, efficiency, and superior performance. Materials for Customized CNC Machining Customized CNC machining involves a meticulous selection of materials based on the specific requirements of each project. The choice of materials not only influences the physical properties of the finished components but also plays a crucial role in determining their performance, durability, and suitability for diverse applications. This section provides an in-depth exploration of the considerations involved in selecting different materials for customized CNC machining. Selection of Different Materials The versatility of customized CNC machining lies in its ability to work with a wide array of materials. The selection process begins with a comprehensive understanding of the project’s specifications, including mechanical, thermal, and chemical requirements. Common materials employed in customized CNC machining include metals, plastics, and composites, each offering unique characteristics that cater to specific needs. Metals Metals such as aluminum, steel, titanium, and brass are frequently chosen for their exceptional strength, durability, and heat resistance. The selection of a particular metal depends on factors like the application’s load-bearing requirements, corrosion resistance, and weight considerations. Plastics Plastics like ABS, PVC, and nylon find extensive use in customized CNC machining, particularly in industries where lightweight components and corrosion resistance are paramount. These materials are valued for their versatility, ease of machining, and suitability for applications requiring intricate designs. Composites Composite materials, combining elements like carbon fiber or fiberglass with resins, balance strength and lightness. They find applications in aerospace, automotive, and sports equipment manufacturing, where the demand for high-performance components is prevalent. Impact of Materials on Part Performance The performance of CNC-machined parts is intricately tied to the materials chosen for fabrication. The mechanical, thermal, and chemical properties of selected materials directly influence the functionality and longevity of the final components. Mechanical Properties A material’s tensile strength, hardness, and elasticity impact its ability to withstand mechanical stress and deformation. Tailoring material selection to the mechanical requirements of a project ensures the production of components capable of withstanding specific loads and forces. Thermal Properties In applications where temperature variations are a concern, thermal properties such as conductivity and expansion coefficient become critical. Choosing materials with appropriate thermal characteristics ensures stability and reliability under varying temperature conditions. Chemical Compatibility Industries exposed to harsh chemicals or corrosive environments necessitate materials with high chemical resistance. Selecting materials that can withstand exposure to specific chemicals is crucial for ensuring the longevity and performance of CNC-machined parts. Commonly Used Customization Materials Understanding the characteristics of commonly used materials in customized CNC machining is