Everything You Need to Know About CNC Milling
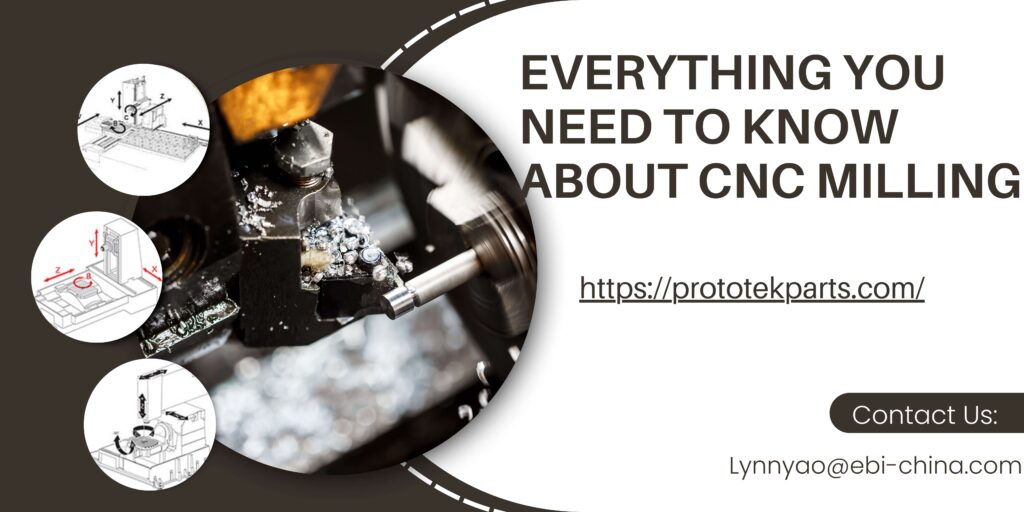
Everything You Need To Know About CNC Milling CNC machining is Computer Numerical Control machining, the manufacturing process that uses computerized controls to control machines. CNC machining allows accurate and precise turning shaping and drilling of a variety of metals. In the following article, you will be focusing on the processes of CNC milling, and the advantages, as well as disadvantages of CNC milling. By understanding CNC milling, it will aid you in finding the best supplier. What is CNC Milling? CNC milling is the exact milling machining procedure that we have come to know and love but with the added benefit of computer-controlled. Milling is the cutting process of materials like plastic, metal, or wood with a tool that rotates. Every aspect, such as the cut toolpath, feed speed, and tool sequencing, is determined by the controls. Many different kinds of CNC milling machines permit various levels of complexity when it comes to cutting. The simplest models typically comprise three axes, however, more advanced models may contain up to five. They are utilized to create more intricate components. A variety of tools are available to help support different variations of the milling process. These range from traditional end mills and drill bits to specialty face milling and profile milling machines. With the many types of CNC cutters and mills virtually any design or shape can be created with the CNC milling equipment. The first commercially-available CNC milling device was designed during 1952 by Richard Kegg, in collaboration with J.F. Reintjes as well as his group from the Massachusetts Institute of Technology. Since then, a variety of advances regarding CNC milling technology have been made and include more advanced CNC milling machines, as well as automated. It makes use of a set of cutting tools that turn to make parts from blocks of material within one cycle. The material is taken off of the workpiece as the blade of the cutter comes into contact with the workpiece while it is rotating. When a milling cut is made, the workpiece is securely held in place while the cutter begins to remove the material. The exact paths of the cutter cutting depths, cut lengths, the XYZ and axis movement as well as spindle RPM all have previously been added to the control software. The process is utilized in a variety of industries, including automotive aerospace and construction, agriculture electronic, consumer goods. To create a variety of components, including components for engines and landing gears, and tanks for fuel in airplanes and surgical devices like surgical scalpels as well as implants. What is the CNC milling machine’s function? Step 1: Design a CAD model Machinists utilize design software to design a CAD-based model of the specific part. Step 2: convert your CAD model to a CNC machine Then, you can transfer the CAD model to The CAM CNC system, which is a computer-aided production. If you do it correctly you’ll have an array of digital instructions that instruct what the machine it should do, also known as G-code. G-code commands allow machines to determine which direction to travel and how quickly to complete it to produce a specific component. Step 3: Configure the CNC milling machine Attach the block of material or workpiece to the machine’s bed. Using metrology instruments and touch probes, ensure that it’s aligned properly. Install the machine’s spindle and follow the steps to set up your milling equipment. Step 4 Start the milling process Launch the program to begin to begin the CNC cutting process. The special cutting tools spin at a high speed or at a set number of revolutions per minute to remove materials from the workpiece until it is able to accurately reproduce the part you’re looking for. What are the 3-, 4– and 5-axis milling machines? 3-axis milling machines permit the cutting tool to move and subtract components through the Z, X, and Y Axes. This type of machining is most well-known due to its low initial cost. It is also employed to make basic parts that have a simple geometrical design. A 4-axis milling machine comes with all the advantages of a three-axis milling machine plus another axis. Additionally, it permits the workpiece to rotate to cut on the A-axis. This is especially helpful for parts that need to be cut in a circle, or the edge of an object. The 5-axis milling machines allow for the movement of three linear axes, as well as the turning of the machine’s head as well as the tool head. These are five axes in one. It produces products with complicated geometries like aerospace products including titanium parts, medical devices, and gas machine components. Since it can perform multidimensional rotation that eliminates the necessity of multiple setups and permits one-step machining that is quicker and more efficient. CNC Milling Methods Many different milling tools can be used to create components. First was plain milling, a technique that cuts flat surfaces that are parallel to the rotation of the tool. Since its initial appearance on the scene of manufacturing, CNC machining has led to various other types of milling being created. This includes: Face milling: It cuts materials to form a surface that is perpendicular to the rotation axis of the cutting tool. Angulous Milling: removes material from the plane surface by making an angle. Form Milling: It also cuts material however this time, to create an irregular surface (i.e. curvatures, etc.). Gang Milling The method used is capable of increasing the speed of production since it employs two cutters, and sometimes more than one, to cut the material. Surface Milling: Used to remove material from the surface of a workpiece to flatten or form a specific shape. Mainly used for machining planes or contour edges, usually using a flat milling cutter or an end mill. Suitable for machining simpler workpiece surfaces such as planes, grooves, holes, etc. Profile Milling: Used to cut on the surface of a workpiece according to a specific contour or curve shape. Can be used to machine complex contours or curve shapes, usually requiring a specific tool to be designed according to the contour