The Difference Between Galvanized And Stainless Steel
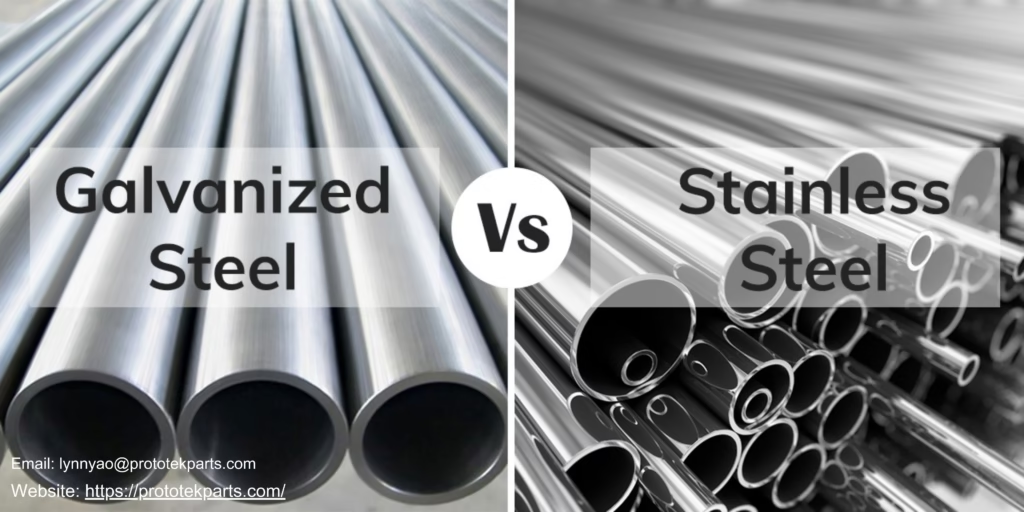
The Difference Between Galvanized And Stainless Steel Material selection in CNC machining is an integral component of its success and must be considered carefully to produce results with optimal performance, durability and cost-efficiency. Galvanized steel and stainless steel are among the many available metals; two commonly utilized choices are galvanized steel and stainless steel; both offer distinct properties suitable for various applications – but understanding their differences is crucial for making informed decisions. In this article, we explore their characteristics, advantages and limitations to help you choose an appropriate material for your CNC machining needs. Introduction to Galvanized Steel and Stainless Steel Galvanized steel is essentially carbon steel that has been coated with a layer of zinc to protect it from corrosion. The galvanization process involves immersing the steel in a bath of molten zinc, which forms a protective layer on the surface. This layer acts as a barrier, preventing moisture and oxygen from reaching the underlying steel, thereby extending its lifespan. Stainless steel, on the other hand, is an alloy of iron, carbon, and a minimum of 10.5% chromium. The chromium content is what gives stainless steel its corrosion-resistant properties. When exposed to oxygen, chromium forms a thin, invisible layer of chromium oxide on the surface, which prevents further oxidation and corrosion. Stainless steel is available in various grades, each with specific properties tailored to different applications. How is galvanized steel made? Hot-dip galvanizing steel typically involves submersion of it in a molten bath of zinc. This method produces a thick, uniform coating that adheres firmly to the steel surface. Before submersion begins, however, steel must first be cleaned of any contaminants such as grease, dirt and rust as any residual substances may hinder adhesion of zinc coating. Once steel has been prepared for galvanizing, it must first be heated in a furnace to remove moisture and reach an ideal temperature for galvanization. Next, it is immersed in a bath of molten zinc solution to coat its surface completely – creating intermetallic layers between zinc and steel which help strengthen bonds between both materials. Once removed from this bath of liquid zinc solution, steel must cool in its environment before solidifying its new durable coat. Electro-galvanizing is another method for galvanizing steel surfaces, using electricity to deposit zinc onto its surface. While this produces a thinner coat than hot-dip galvanizing, electro-galvanization may be ideal for applications requiring smoother finishes and requires less preparation time overall. No matter which approach is taken when galvanizing steel, its results remain unchanged: galvanized steel shows increased corrosion resistance and longevity when compared with untreated steel making it an appealing material in many industries. Types of stainless steel Stainless steel can be divided into several distinct types based on its microstructure and composition of alloying elements, with primary categories including austenitic, ferritic, martensitic, duplex and precipitation-hardening stainless steels as the most widely used types. Each has specific properties tailored specifically for various applications providing an extensive variety of performance characteristics for various tasks. Austenitic stainless steel is one of the most frequently utilized types, known for its superior corrosion resistance and formability. Containing high levels of chromium and nickel which enhance its weldability and ductility. Due to this property it’s often used in kitchen equipment, chemical processing facilities, architectural projects as well as to prevent staining.Ferritic stainless steel contains lower amounts of nickel and has magnetic properties, making it less ductile than austenitic but offering excellent resistance to stress corrosion cracking. Ferritic stainless steel can be found in automotive applications, kitchen sinks and other environments where magnetic properties may prove advantageous. Martensitic stainless steel is known for its superior strength and hardness, making it suitable for applications requiring wear resistance such as cutting tools and surgical instruments. Duplex stainless steel combines properties from both austenitic and ferritic types for increased strength as well as corrosion resistance – perfect for oil and gas applications. Advantages of galvanized steel & stainless steel 1. Corrosion Resistance Galvanized steel offers excellent corrosion resistance due to the zinc coating. However, the level of protection depends on the thickness of the zinc layer and the environment in which the steel is used. In mild environments, galvanized steel can last for decades without significant corrosion. However, in more aggressive environments, such as coastal areas with high salt content, the zinc layer may degrade faster, leading to corrosion of the underlying steel. Stainless steel is inherently more corrosion-resistant than galvanized steel, especially in harsh environments. The chromium oxide layer provides a self-healing mechanism; if the surface is scratched or damaged, the chromium reacts with oxygen to reform the protective layer. This makes stainless steel ideal for applications where exposure to moisture, chemicals, or salt is a concern. 2. Strength and Durability Galvanized steel is known for its strength and durability. The zinc coating not only protects against corrosion but also adds to the overall toughness of the material. However, the mechanical properties of galvanized steel are largely dependent on the base carbon steel. While it is strong, it may not be as durable as stainless steel in certain applications, especially those involving high stress or impact. Stainless steel is generally stronger and more durable than galvanized steel. The addition of alloying elements such as nickel, molybdenum, and titanium enhances its mechanical properties, making it suitable for high-stress applications. Stainless steel also has excellent fatigue resistance, which is crucial for components subjected to cyclic loading. 3. Machinability Galvanized steel is relatively easy to machine, especially when compared to some stainless steel grades. The zinc coating does not significantly affect the machinability of the base steel, allowing for smooth cutting, drilling, and shaping. However, the presence of the zinc layer can lead to increased tool wear, particularly if the coating is thick or uneven. Stainless steel can be more challenging to machine due to its hardness and work-hardening properties. Certain grades, such as austenitic stainless steels (e.g., 304 and 316), are particularly prone to work hardening, which can lead to increased tool wear