Kaltumformung vs. Warmumformung
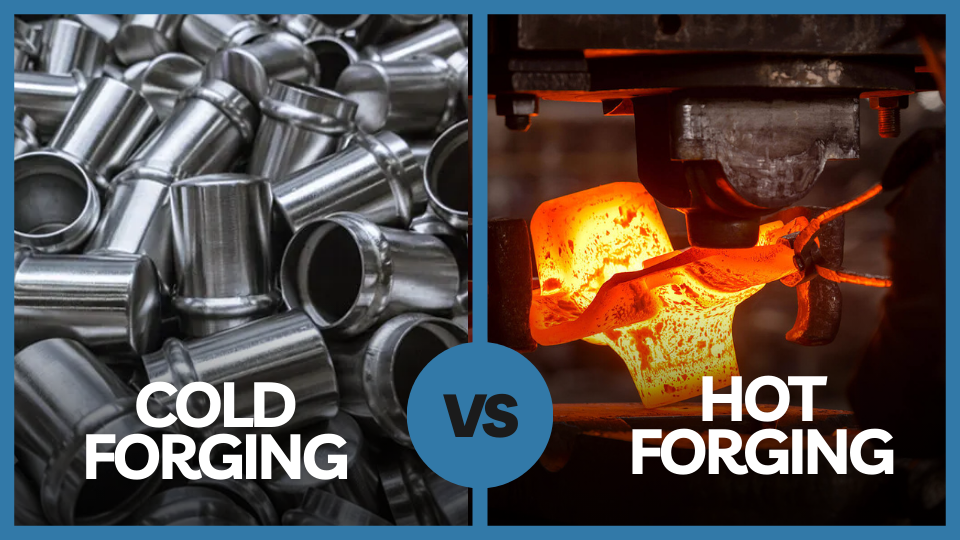
Cold Forging vs Hot Forging In advanced manufacturing, choosing cold and hot forging can significantly impact your components’ quality, strength, and cost-effectiveness. At Prototek, we specialize in delivering superior forging solutions tailored to meet the exacting demands of various industries. This article explores the differences, advantages, and applications of cold and hot forging, showcasing how Prototek’s expertise can elevate your production processes. Understanding Cold Forging Cold forging, or cold working, involves molding metal at or close to room temperature. Through this process, the material holds its unique glass-like structure, which results in expanded hardness and rigidity. The process is not like hot fashioning because the metal isn’t warmed, instead it’s worked in its room-temperature state, below its recrystallization state. Precision in Cold Forging Cold forging involves shaping metal at room temperature or slightly above, using high-pressure dies to form the desired shape. This process is ideal for producing intricate components with excellent dimensional accuracy and surface finish. At Prototek, our cold forging capabilities are backed by state-of-the-art equipment and seasoned craftsmanship, ensuring reliable performance for diverse applications. Advantages of Cold Forging at Prototek: 1. Material Conservation: Cold forging minimizes waste using precise die designs and controlled deformation. This efficiency translates into cost savings and environmental benefits for our clients. 2. Enhanced Mechanical Properties: Due to strain hardening, components forged through cold forging exhibit superior strength, toughness, and surface hardness. Prototek optimizes forging parameters to achieve optimal mechanical properties. 3. Complex Geometries: Cold forging produces complex shapes and features with tight tolerances. Prototek’s engineering expertise and CAD/CAM capabilities ensure seamless design and production integration. 4. Cost-Effective Solutions: Cold forging offers a cost-effective solution for high-volume production runs by reducing machining and material costs. Prototek’s streamlined processes and efficient workflow deliver competitive pricing without compromising quality. 5. Versatility Across Industries: From automotive and aerospace to consumer electronics and medical devices, cold forging serves a wide range of industries where precision and reliability are paramount. Delving into Hot Forging Hot forging, or hot working, includes shaping metal at raised temperatures, usually between 700°C and 1,200°C. The metal is heated to provide flexibility and make it more bendable. Strength and Durability in Hot Forging Hot forging involves heating metal above its recrystallization temperature and then shaping it using dies. This process enhances the material’s plasticity, allowing for easier deformation and superior mechanical properties in the finished parts. Prototek’s hot forging capabilities leverage advanced technology to deliver robust solutions for demanding applications. Advantages of Hot Forging at Prototek: 1. High Strength-to-Weight Ratio: Hot forged parts exhibit exceptional mechanical properties, including high tensile strength, impact resistance, and fatigue strength. Prototek optimizes forging temperatures and dwell times to achieve desired material characteristics. 2. Dimensional Accuracy: Hot forging allows for precise control over grain structure and flow lines, resulting in parts with excellent dimensional stability and uniformity. Prototek’s meticulous process controls ensure consistent quality across production batches. 3. Complex Part Designs: While suitable for simpler geometries, hot forging is particularly practical for parts requiring significant deformation or thick cross-sections. Prototek’s engineering team collaborates closely with clients to optimize designs for hot forging feasibility. 4. Cost-Efficiency in Bulk Production: Hot forging offers economies of scale in large-scale production runs despite higher initial setup costs. Prototek’s strategic tooling and process optimization approach maximizes efficiency and minimizes per-part costs. 5. Wide Application Spectrum: From industrial machinery components to specialized fittings and fasteners, hot forging serves industries demanding robust, high-performance parts subjected to extreme conditions. Making the Right Choice with Prototek Why Choose Prototek for Forging Solutions? 1. Expertise and Innovation: With decades of experience in precision manufacturing, Prototek combines industry-leading expertise with innovative forging technologies to meet evolving market demands. 2. Customized Solutions: Whether you require prototype development, small-batch production, or full-scale manufacturing, Prototek offers tailored forging solutions to optimize performance and reduce time-to-market. 3. Quality Assurance: Prototek adheres to stringent standards throughout the forging process, ensuring every component meets or exceeds customer expectations for durability, reliability, and performance. 4. Collaborative Partnership: We prioritize client collaboration, providing responsive communication, flexible solutions, and proactive project management to ensure seamless project execution and satisfaction. 5. Comprehensive Service Offering: From initial design consultation to final inspection and delivery, Prototek offers end-to-end forging solutions under one roof, streamlining processes and enhancing overall project efficiency. Conclusion In conclusion, choosing between cold and hot forging depends on specific project requirements, including material properties, part complexity, production volume, and cost considerations. At Prototek, we empower you to make informed decisions by offering unparalleled expertise, cutting-edge technology, and a commitment to excellence in every forging solution we deliver. Contact Prototek today to discuss your forging needs and discover how we can optimize your production processes with precision, strength, and reliability—partner with Prototek to forge solutions that elevate your products to new heights of performance and durability. If you have any needs, contact us via email at Lynnyao@prototekparts.com or phone: +86-0792-86372550 Tags: Social Network: Recently Posts Online Help! +(86) 0791-86372550 Have Questions? Want To Discuss In Detail? Contact Our Consultant Now CONTACT
CNC-Fräsen vs. CNC-Drehen
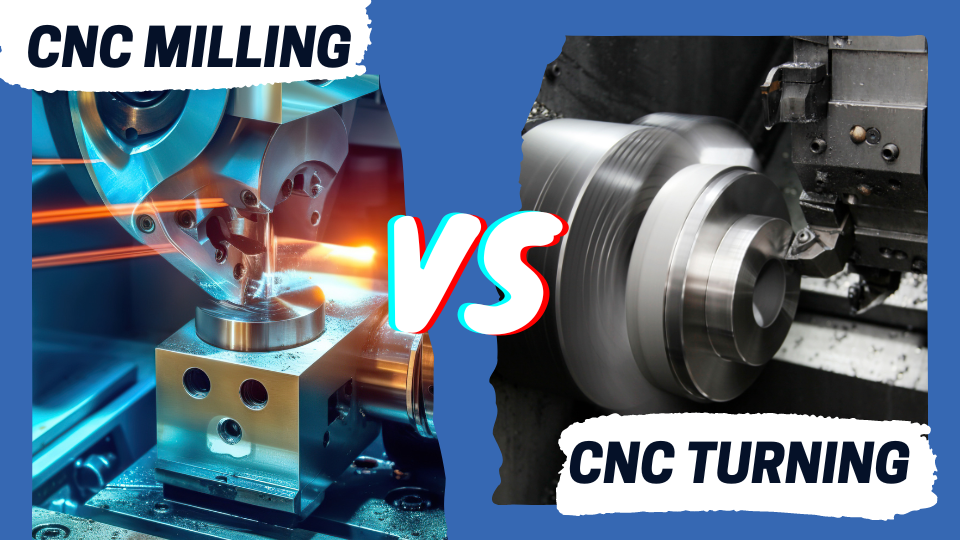
CNC Milling vs CNC Turning In today’s rapidly evolving manufacturing landscape, precision and efficiency are paramount. Choosing the proper machining process is crucial in aerospace, automotive, medical devices, or any other industry requiring intricate components. At Prototek, we deliver high-quality CNC machining solutions tailored to meet diverse client needs. This article explores the differences, advantages, and applications of CNC milling and turning, empowering you to make informed decisions for your projects. Understanding CNC Milling The Art of CNC Milling CNC milling involves using rotary cutting tools to remove material from a workpiece, creating complex shapes and features. This process is ideal for producing components with detailed designs and strict dimensional tolerances. At Prototek, our CNC milling capabilities are at the forefront of precision manufacturing, allowing us to cater to various industries and applications. Advantages of CNC Milling at Prototek 1. Precision and Versatility: CNC milling excels in machining parts that require high precision and intricate geometries. Our state-of-the-art milling machines and CAD/CAM software ensure consistent accuracy, meeting even the most demanding specifications. 2. Material Flexibility: CNC milling accommodates various materials, from aluminum and stainless steel to plastics and composites. This versatility enables Prototek to serve clients across multiple industries, from prototyping to production. 3. Complexity Handling: We leverage advanced technologies to efficiently tackle complex designs involving 3-axis, 4-axis, or 5-axis milling. Prototek’s engineering expertise ensures optimal tool paths and machining strategies for each project. 4. Rapid Prototyping and Short Runs: With efficient programming and setup, Prototek delivers rapid prototyping services and seamlessly handles small to medium production runs. This agility is crucial for accelerating product development cycles and meeting tight deadlines. 5. Quality Assurance: Rigorous quality control measures, including in-process inspections and final checks, guarantee that every component meets the highest standards before leaving our facility. Delving into CNC Turning Mastering CNC Turning Techniques CNC turning revolves around rotating a workpiece while cutting tools remove material to create cylindrical shapes and symmetrical parts. This process is highly efficient for producing axially symmetric components with minimal setup times, making it cost-effective for large-scale production runs. Advantages of CNC Turning at Prototek 1. Efficiency and Speed: CNC turning produces cylindrical parts quickly and efficiently. Prototek’s advanced turning centers and skilled operators ensure consistent performance and rapid turnaround times for our clients. 2. Cost-Effectiveness: CNC turning offers significant cost advantages over other machining methods for high-volume production runs. Prototek optimizes material usage and production processes to deliver competitive pricing without compromising quality. 3. Versatility in Component Size: Whether small precision parts or more significant components up to a specific diameter and length, CNC turning accommodates a wide range of sizes and shapes. This versatility caters to diverse industry needs, from automotive components to medical instruments. 4. Surface Finish and Tolerance Control: Prototek ensures superior surface finishes and tight dimensional tolerances in every turned component with fine-tuned cutting parameters and tooling selection. This attention to detail is critical for meeting functional and aesthetic requirements. 5. Consistency and Reliability: Prototek maintains stringent quality controls throughout the turning process, from initial setup to final inspection. Our commitment to reliability ensures that each part meets customer specifications and exceeds expectations. Choosing the Right Methodology Factors Influencing Your Decision When deciding between CNC milling and CNC turning for your project, several factors come into play: 1. Part Complexity: Complex geometries and features often favor CNC milling because they can maneuver in multiple axes and perform intricate cuts. 2. Material Type: Consider the material’s hardness, machinability, and specific properties. CNC milling is versatile and uses a wide range of materials, while CNC turning is efficient for softer metals and plastics. 3. Production Volume: CNC milling offers flexibility and rapid turnaround for small batches and prototypes. Conversely, CNC turning is optimal for high-volume production due to its efficiency and lower per-part cost. 4. Tolerance Requirements: Evaluate the required dimensional accuracy and surface finish. Both processes can achieve tight tolerances, but the approach may vary based on part geometry and material. 5. Lead Time and Cost: Assess project timelines and budget constraints. Prototek’s streamlined processes ensure competitive pricing and timely delivery, supporting your project’s success. Prototek’s Commitment to Excellence Why Choose Prototek? At Prototek, we are more than a CNC machining service provider – your strategic partner in innovation and manufacturing excellence. Here’s why clients trust us: 1. Advanced Technology: Our cutting-edge CNC equipment and software investment ensures superior precision and efficiency across all projects. 2. Expertise and Experience: With decades of experience in precision machining, our team of engineers and machinists delivers innovative solutions tailored to your needs. 3. Quality Assurance: From initial design consultation to final inspection, Prototek adheres to rigorous quality standards to deliver flawless components that meet or exceed industry requirements. 4. Customer Focus: We prioritize client satisfaction, offering responsive communication, flexible solutions, and proactive project management to ensure your expectations are met and exceeded. 5. End-to-End Solutions: Whether you need rapid prototyping, small-batch production, or full-scale manufacturing, Prototek provides comprehensive CNC machining services under one roof. Conclusion In conclusion, CNC milling and turning are integral to modern manufacturing, each offering unique advantages depending on project requirements. At Prototek, we leverage our expertise, advanced technology, and commitment to quality to deliver exceptional results for our clients. Whether launching a new product, refining an existing design, or scaling production, our CNC machining capabilities empower you to achieve your goals efficiently and cost-effectively. Contact Prototek today to discuss your CNC machining needs and discover how we can elevate your projects from concept to reality—partner with us for precision, reliability, and innovation in manufacturing. If you have any needs, contact us via email at Lynnyao@prototekparts.com or phone: +86-0792-86372550 Tags: Social Network: Recently Posts Online Help! +(86) 0791-86372550 Have Questions? Want To Discuss In Detail? Contact Our Consultant Now CONTACT