What is CNC Aluminum
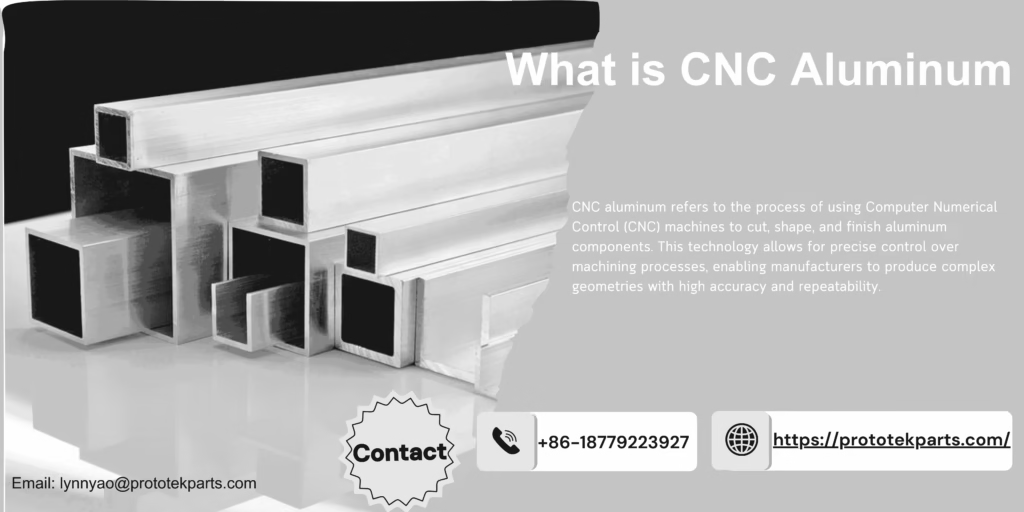
What is CNC Aluminum Do you want to get into the realm of CNC aluminum? Don’t look any further! In this definitive guide that we’ve prepared for you all you must learn about CNC aluminum cutting. No matter if you’re just starting out exploring the possibilities or a professional who is looking to increase the ante, this thorough guide will help you navigate the entire process from start to the very end. We’ll discuss the characteristics and benefits of aluminum to help you choose the right CNC machine for your project. And gain knowledge of various cutting techniques, surface treatments, and machining strategies to achieve the best results. Learn the secrets of CNC aluminum machining and tap into the potential of manufacturing high-quality precision components. With our help, you’ll gain the information and expertise to take your projects to the next level. Get ready to start your aluminum adventure and transform your manufacturing process with what CNC technology can offer. What is CNC Aluminum? CNC aluminum refers to the process of using Computer Numerical Control (CNC) machines to cut, shape, and finish aluminum components. This technology allows for precise control over machining processes, enabling manufacturers to produce complex geometries with high accuracy and repeatability. CNC machining involves the use of computer programs to direct the movements of machine tools, which can include milling, turning, drilling, and grinding. The versatility of CNC machines makes them ideal for working with aluminum, a material renowned for its lightweight and durable properties. Aluminum is a preferred material in many industries due to its lightweight properties as well as its durability, strength-to-weight ratio as well as its rust resistance. The combination of CNC technology with aluminum enables manufacturers to create complex and top-quality designs. Automating the machining process does not just improve efficiency, it reduces human error, resulting in consistently top-quality components. It is a CNC Aluminum Machining process can adapt to a variety of requirements, including prototypes or for mass production runs. This technique is crucial to creating precise parts for industries like aerospace and consumer electronics. A thorough understanding of the CNC aluminum machining concepts is vital to fully utilize the potential of this technology in many projects. Advantages of CNC Aluminum One of the major benefits of CNC aluminum machine is the precision. CNC machines can execute intricate designs with incredible precision with tolerances often within millimeters. This degree of precision is essential in the field where even the smallest deviation can cause major problems or even safety concerns. Automation of CNC machines helps reduce human error and guarantees that every part manufactured meets the dimensions specified and meets the quality standards. Another benefit of using CNC for aluminum is the efficiency it brings to the manufacturing process. CNC machines can operate continuously, reducing downtime and increasing productivity. The capability to program complex patterns means that multiple parts can be machined simultaneously, further speeding up the overall production time. This efficiency translates into cost savings, making CNC aluminum machining an economically viable option for both small-scale and large-scale production. In addition, the properties inherent to aluminum enhance the benefits of CNC machines. Aluminum is light and strong and therefore suitable for a variety of applications where reducing weight is crucial without the structural quality. Its resistance to corrosion as well as its ability to finish allow for a variety of treatments for surfaces, which enhance the aesthetics and functionality. In the end, using CNC technologies and aluminum produces top-quality products that can satisfy the requirements of modern-day manufacturing. Applications of CNC Aluminum CNC aluminum machining finds use across multiple industries. In aerospace, for example, aluminum components are essential due to their lightweight yet strong nature and strength; parts such as brackets, housings, and structural elements often made of aluminum are machined by CNC machining for optimal fuel efficiency and performance. CNC’s precise operation helps meet the stringent safety standards demanded of this industry. CNC aluminum fabrication finds widespread application in the automotive sector. Aluminum is increasingly being utilized for car components like engine components, wheels, and frames due to its lightweight properties that help increase fuel efficiency and performance – key considerations of modern vehicle design. CNC machining allows mass production of high-quality aluminum parts that meet these demands while giving designers the freedom to craft intricate shapes and forms with creative freedom. CNC aluminum machining offers great benefits to the electronics industry, especially smartphones, laptops, and various consumer electronics that use aluminum casings or components for aesthetic and functional reasons. CNC aluminum machining’s capacity to produce intricate designs while remaining cost-effective makes it a popular option among manufacturers looking to expand their offerings while keeping their edge in the market. Types of CNC Aluminum When it comes to CNC aluminum machining, several types of aluminum alloys can be utilized, each with unique properties that cater to specific applications. One of the most common types is 6061 aluminum, which is known for its excellent mechanical properties and corrosion resistance. This alloy is often used in structural applications and is favored for its weldability and versatility. Its balance of strength, workability, and resistance to corrosion makes it a go-to choice for many manufacturers. Another popular alloy is 7075 aluminum, which is known for its high strength and is often used in aerospace applications. This alloy is ideal for parts that must endure high stress and strain, providing superior performance without adding excessive weight. However, it is less workable than other alloys, so specialized machining techniques may be required during the CNC process to achieve the desired results. Additionally, 5052 aluminum is renowned for its excellent corrosion resistance and formability, making it suitable for marine environments and applications where exposure to the elements is a concern. This alloy is often used for fuel tanks, pressure vessels, and marine components. Understanding the different types of aluminum and their properties is crucial for selecting the right material for your CNC machining projects, as it directly impacts the performance and durability of the final product. Choosing