Blog Details
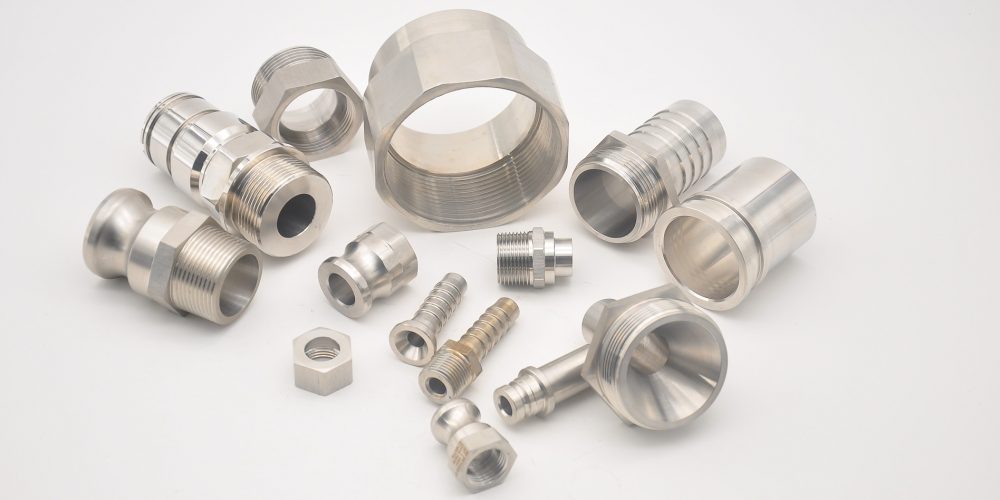
Prototek Unveils the World of Customized CNC Machining Parts
In the dynamic landscape of manufacturing, CNC machining has emerged as a pivotal force, offering precision and efficiency in the production of components. One facet that has gained significant traction is the customization of CNC machining parts, presenting a spectrum of advantages for businesses and individuals.
What is CNC Machining
CNC or Computer Numerical Control, is a sophisticated manufacturing process that utilizes computerized systems to control machine tools. It involves various operations, from milling to turning, and has become ubiquitous in various industries.
The Need for Customized CNC Machining Parts
In the realm of modern manufacturing, the demand for customized CNC machining parts has surged, driven by the unique requirements of diverse industries and individual projects. This section delves into the multifaceted reasons behind the growing need for tailored solutions, highlights the advantages over standardized components, and explores real-world success stories that underscore the impact of customization.
Reasons for the Demand
The demand for customized CNC machining parts stems from the inherent diversity of projects across industries. Standardized components often fall short in meeting the specific and intricate requirements of applications ranging from aerospace and automotive to medical and electronics. Customization allows for precision engineering, ensuring that each part aligns perfectly with the unique specifications of a given project.
The ability to adapt designs to specific functionalities, tolerances, and environmental conditions is a driving force behind the increasing preference for customization. Industries, especially those at the forefront of technological advancements, seek tailored solutions to stay ahead in a competitive landscape.
Comparison with Standard Parts
A fundamental distinction between customized CNC machining and standard parts lies in adaptability. While standard parts offer mass-produced solutions suitable for broad applications, they often require more precision and specificity for cutting-edge projects.
On the other hand, customized parts are crafted with meticulous attention to detail, ensuring an exact fit for the intended purpose. This tailored approach minimizes unnecessary material usage and streamlines manufacturing, resulting in optimized performance and efficiency.
Success Stories in the Industry
The success stories associated with customized CNC machining parts vary across industries.
1. Aerospace Advancements
In the aerospace industry, where precision and reliability are non-negotiable, customized CNC machining parts have played a pivotal role in achieving breakthroughs. Tailored components designed to withstand extreme conditions and reduce weight have enhanced fuel efficiency and overall aircraft performance.
2. Medical Marvels
The demand for custom CNC parts has surged in the medical field due to the need for specialized equipment and implants. Customization allows for intricate designs that match the complexity of the human body, leading to more effective and personalized medical solutions.
3. Automotive Innovations
Automotive manufacturers increasingly turn to customized CNC machining to produce components that improve vehicle performance, safety, and aesthetics. From lightweight parts for fuel efficiency to intricate designs for advanced driver-assistance systems, customization drives innovation in the automotive sector.
4. Electronics Precision
In the electronics industry, where miniaturization and precision are paramount, customized CNC machining parts enable the production of intricate components for devices ranging from smartphones to sophisticated electronic systems. This level of customization ensures optimal functionality and performance in electronic applications.
These success stories highlight the transformative impact of customized CNC machining parts across diverse sectors. The ability to tailor components to specific needs enhances performance, fosters innovation, and pushes the boundaries of what is achievable in manufacturing.
In conclusion, the burgeoning need for customized CNC machining parts is a testament to the evolving landscape of modern manufacturing. As industries continue to advance, customization becomes increasingly pivotal, offering a pathway to innovation, efficiency, and superior performance.
Materials for Customized CNC Machining
Customized CNC machining involves a meticulous selection of materials based on the specific requirements of each project. The choice of materials not only influences the physical properties of the finished components but also plays a crucial role in determining their performance, durability, and suitability for diverse applications. This section provides an in-depth exploration of the considerations involved in selecting different materials for customized CNC machining.
Selection of Different Materials
The versatility of customized CNC machining lies in its ability to work with a wide array of materials. The selection process begins with a comprehensive understanding of the project’s specifications, including mechanical, thermal, and chemical requirements. Common materials employed in customized CNC machining include metals, plastics, and composites, each offering unique characteristics that cater to specific needs.
Metals
Metals such as aluminum, steel, titanium, and brass are frequently chosen for their exceptional strength, durability, and heat resistance. The selection of a particular metal depends on factors like the application’s load-bearing requirements, corrosion resistance, and weight considerations.
Plastics
Plastics like ABS, PVC, and nylon find extensive use in customized CNC machining, particularly in industries where lightweight components and corrosion resistance are paramount. These materials are valued for their versatility, ease of machining, and suitability for applications requiring intricate designs.
Composites
Composite materials, combining elements like carbon fiber or fiberglass with resins, balance strength and lightness. They find applications in aerospace, automotive, and sports equipment manufacturing, where the demand for high-performance components is prevalent.
Impact of Materials on Part Performance
The performance of CNC-machined parts is intricately tied to the materials chosen for fabrication. The mechanical, thermal, and chemical properties of selected materials directly influence the functionality and longevity of the final components.
Mechanical Properties
A material’s tensile strength, hardness, and elasticity impact its ability to withstand mechanical stress and deformation. Tailoring material selection to the mechanical requirements of a project ensures the production of components capable of withstanding specific loads and forces.
Thermal Properties
In applications where temperature variations are a concern, thermal properties such as conductivity and expansion coefficient become critical. Choosing materials with appropriate thermal characteristics ensures stability and reliability under varying temperature conditions.
Chemical Compatibility
Industries exposed to harsh chemicals or corrosive environments necessitate materials with high chemical resistance. Selecting materials that can withstand exposure to specific chemicals is crucial for ensuring the longevity and performance of CNC-machined parts.
Commonly Used Customization Materials
Understanding the characteristics of commonly used materials in customized CNC machining is essential for making informed decisions during the material selection.
Aluminium
It is widely known for its lightweight yet durable properties, so aluminum is a popular choice in aerospace, automotive, and electronic applications. It offers excellent corrosion resistance and is easily machinable.
Stahl
With its exceptional strength and versatility, steel is a staple in CNC machining. Different types of steel alloys cater to a broad spectrum of applications, from precision components to heavy-duty machinery parts.
Titan
Valued for its high strength-to-weight ratio and corrosion resistance, titanium finds applications in aerospace, medical implants, and military components. Its biocompatibility makes it suitable for medical applications.
Plastics
Plastics like ABS, known for its impact resistance, PVC for chemical resistance, and nylon for its versatility, are chosen based on the desired properties for a given application. They are commonly used in consumer products, electronics, and industrial components.
Composites
Carbon fiber and fiberglass composites combine strength, stiffness, and lightness. They are prevalent in high-performance applications, such as sports equipment, automotive components, and aerospace structures.
The meticulous selection of materials in customized CNC machining is a pivotal step in ensuring the success of a project. By understanding the unique properties and considerations associated with various materials, manufacturers can optimize CNC-machined components’ performance, durability, and functionality to meet the exacting demands of diverse applications.
Key Considerations in Designing Custom CNC Parts
The design phase is a critical juncture in the production of customized CNC parts, determining the manufacturing process’s success and the final components’ functionality. This section delves into the fundamental considerations and principles that guide the design of custom CNC parts, emphasizing the role of Computer-Aided Design (CAD), the importance of communication with manufacturers, and strategies for optimizing designs to enhance production efficiency.
Basic Principles of CAD Design
Computer-aided design (CAD) forms the cornerstone of designing custom CNC parts. Leveraging digital tools allows designers to create intricate and precise 3D models that serve as manufacturing blueprints. The following principles highlight the essentials of CAD design in the context of customized CNC parts:
Precision and Accuracy
CAD enables designers to achieve unparalleled precision and accuracy in specifying dimensions, tolerances, and geometric features. This precision ensures that the final CNC-machined parts meet the exact specifications required for optimal performance.
Parametric Design
Utilizing parametric design principles allows for the creation of flexible and adaptable models. Parameters can be adjusted easily, facilitating design modifications based on evolving project requirements or feedback from the manufacturing phase.
Assembly Simulation
CAD tools often include assembly simulation features, allowing designers to visualize how individual components will fit together. This aids in detecting potential interferences, ensuring the seamless integration of custom CNC parts within the larger assembly.
Importance of Communication with Manufacturers
Effective communication between designers and manufacturers is paramount to successfully realizing custom CNC parts. Clear and collaborative communication ensures that the designed components align with the capabilities of CNC machining equipment and meet manufacturing constraints. Key considerations include:
Material Compatibility
Communicating the desired material specifications for CNC machining is crucial. Manufacturers can provide insights into the feasibility and challenges of specific materials, guiding designers in making informed decisions.
Machining Constraints
Understanding the limitations of CNC machining processes is essential. Communication regarding tool access, toolpath complexity, and machining tolerances helps designers optimize their models for manufacturability.
Prototype Iterations
Regular communication throughout the design process facilitates the creation of prototypes for testing and validation. Manufacturers can provide valuable feedback based on the prototyping phase, allowing for iterative improvements before final production.
Optimizing Design for Improved Production Efficiency
Design optimization is central to enhancing production efficiency in customized CNC parts manufacturing. Streamlining designs for manufacturability not only reduces production time but also minimizes material waste. Key strategies for design optimization include:
Minimizing Complex Features
Simplifying geometric features and minimizing complex shapes can enhance machining efficiency. This reduces machining time and lowers the risk of errors and tool wear.
Consistent Material Thickness
Maintaining consistent material thickness across a design contributes to uniform machining conditions. It prevents uneven cutting forces and thermal distortion during CNC machining.
Design for Ease of Fixturing
Considering the ease of fixturing during the design phase is crucial. Well-designed fixturing ensures stable clamping of materials, reducing the likelihood of vibrations and inaccuracies during machining.
In conclusion, the key considerations in designing custom CNC parts involve a meticulous balance between precision, communication, and optimization. By adhering to these principles, designers can harness the full potential of CNC machining, resulting in the efficient production of high-quality, tailor-made components that meet the exacting requirements of diverse applications.
In-Depth Analysis of the CNC Machining Process
Conversion of CAD Design to CNC Programs
The transition from CAD design to CNC programs is a critical step. This process dictates CNC machines’ instructions to produce the desired parts accurately.
Material Preparation and Clamping
Before machining begins, proper material preparation and secure clamping are essential. These steps lay the groundwork for precision and prevent errors in the machining process.
Quality Control Steps During Machining
Continuous quality control measures are integrated throughout the machining process. This ensures that each part meets the specified standards and adheres to quality benchmarks.
Quality Assurance for Custom CNC Parts
Ensuring Part Quality
Quality assurance is a cornerstone of the customization process. Rigorous testing and inspection protocols guarantee that each custom CNC part meets the highest standards.
Inspection and Testing Methods
Various inspection and testing methods, including dimensional checks and material analysis, are employed to validate the integrity of custom CNC parts.
Dealing with Potential Quality Issues
In the event of identified quality issues, proactive measures are taken to address and rectify the issues promptly. This commitment to quality builds trust between manufacturers and clients.
Custom CNC Machining and Cost-effectiveness
Balancing Customization with Cost-effectiveness
While customization offers unparalleled advantages, balancing it with cost-effectiveness is crucial. Strategic decisions in material selection and design optimization contribute to an optimal balance.
Maximizing Return on Investment
Investing in customized CNC machining can yield significant returns over the long term. Tailored solutions often improve efficiency, reduce downtime, and enhance overall performance.
Advantages of Long-term Collaboration
Establishing long-term collaborations with CNC machining partners fosters mutual understanding and efficiency. Consistent quality, timely deliveries, and cost-effectiveness characterize successful long-term relationships.
Industry Trends and Innovations
Current Trends in the CNC Machining Industry
The CNC machining industry is dynamic, with ongoing trends such as automation, smart machining, and sustainable practices shaping its trajectory.
Introduction of Innovative Technologies and Materials
Continuous innovation introduces cutting-edge technologies and materials to the CNC machining landscape. These innovations expand the possibilities for customization and performance improvement.
Outlook for the Future
As technology advances, the future of customized CNC machining holds even greater potential. Anticipated developments include enhanced automation, improved precision, and integrating advanced materials.
Customized CNC machining parts represent a realm of possibilities in the manufacturing landscape. From meeting specific project requirements to pushing the boundaries of innovation, customization stands as a cornerstone in the evolution of CNC machining. As we navigate the future, embracing these opportunities promises superior components and a pathway to groundbreaking advancements in diverse industries.
Wenn Sie einen Bedarf haben, kontaktieren Sie uns per E-Mail: Lynnyao@prototekparts.com oder Telefon: +86-0792-86372550
Tags:
- CNC-Bearbeitung von Teilen