Understanding Mold Making Services: From Prototyping to Mass Production
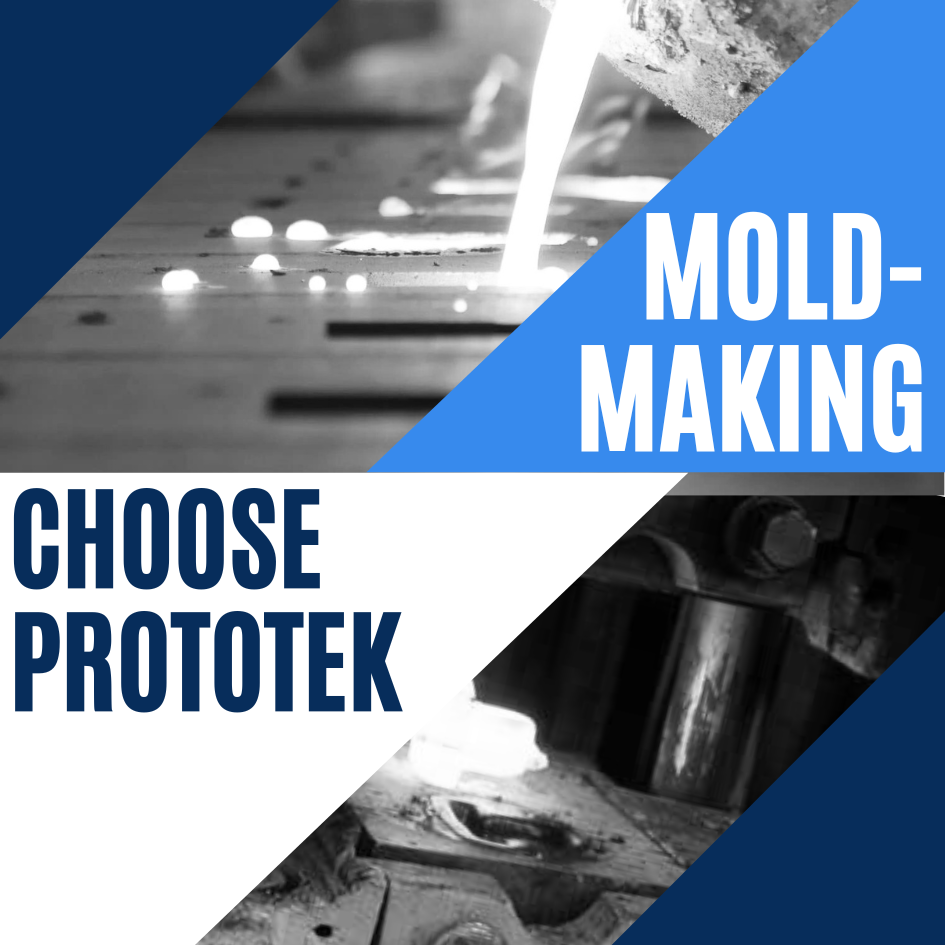
Blog Details In various industries, producing high-quality parts and products often relies on efficient and precise mold making services. These services translate designs into tangible objects, facilitate prototyping, and enable mass production. This article delves into the fundamentals of mold-making services, exploring their processes and benefits and explaining how to choose the right service provider. Basics of Mold Making Understanding Molds Molds are essential tools used in manufacturing to shape raw materials into desired forms. They are the negative space into which materials like plastics, metals, or ceramics are poured or injected, creating finished products. Molds come in various shapes and sizes, ranging from simple one-part molds for basic shapes to complex multi-part molds for intricate designs. The Mold-Making Process The process of mold-making typically involves several distinct stages: 1. Design The design phase is where the specifications and requirements for the mold are established. This includes determining the desired product’s shape, size, and features and selecting the appropriate materials for the mold itself. Modern design tools, such as computer-aided design (CAD) software, are often utilized in this stage to create precise blueprints of the mold. 2. Manufacturing Once the design is finalized, the actual manufacturing of the mold begins. Manufacturing techniques may vary depending on factors like the complexity of the design and the chosen materials. Common methods include machining, casting, and additive manufacturing (e.g., 3D printing). Skilled craftsmen or advanced machinery are employed to transform raw materials into finished mold components. 3. Testing After manufacturing the mold components, they undergo rigorous testing to ensure they meet the specified criteria. Testing may involve verifying dimensional accuracy, assessing material compatibility, and conducting trial runs to simulate real-world production conditions. Any issues or discrepancies discovered during testing are addressed through modifications or adjustments to the mold design or manufacturing process. 4. Revision Based on the results of testing, revisions to the mold design or manufacturing process may be necessary to address any identified issues or optimize performance. This iterative process continues until the mold meets the desired quality, functionality, and reliability standards. Importance of Precision and Accuracy Precision and accuracy are paramount in mold making. Even minor deviations from the intended specifications can result in defective parts or products, leading to waste, rework, and increased production costs. Therefore, meticulous attention to detail and adherence to tight tolerances are critical throughout the mold-making process to ensure consistent, high-quality results. Materials Used in Mold Making The choice of materials for mold making depends on various factors, including the type of product being manufactured, the production volume, and the desired characteristics of the finished mold. Common materials used in mold making include: Metals (e.g., aluminum, steel) for durable, long-lasting molds suitable for high-volume production. Plastics (e.g., epoxy, silicone) are used for cost-effective, flexible molds that are ideal for prototyping and low-volume production. Composites (e.g., fiberglass, carbon fiber) for lightweight, high-strength molds capable of withstanding demanding manufacturing environments. Each material offers unique advantages and considerations in terms of strength, durability, thermal conductivity, and moldability, which must be carefully evaluated to determine the most suitable option for a given application. Types of Mold-Making Services Prototyping Mold-Making Services Prototyping molds plays a crucial role in the product development process by enabling the creation of initial versions of a product for testing, validation, and refinement. These molds are designed to produce prototypes quickly and cost-effectively, allowing designers and engineers to iterate on designs and make necessary modifications before proceeding to mass production. Process and Technologies Prototyping molds employ various advanced manufacturing technologies to rapidly create prototypes with precision and accuracy. Some common techniques include: 3D Printing: Additive manufacturing processes such as stereolithography (SLA), selective laser sintering (SLS), and fused deposition modeling (FDM) are widely used for producing prototype molds directly from digital designs. 3D printing offers fast turnaround times and the ability to create complex geometries with minimal tooling costs. CNC Machining: Computer numerical control (CNC) machining utilizes computer-controlled cutting tools to remove material from a solid block or billet, resulting in highly accurate prototype molds. CNC machining is suitable for producing prototypes from a wide range of materials, including metals, plastics, and composites. Silicone Molding: Silicone molding, also known as rapid tooling or soft tooling, involves creating a silicone mold directly from a master pattern or 3D-printed model. This flexible and cost-effective method allows for producing small-batch prototypes with intricate details and fine surface finishes. Mass Production Mold-Making Services Mass production molds are designed for high-volume manufacturing, allowing businesses to replicate products consistently and efficiently on a large scale. These molds are engineered to withstand continuous production demands while maintaining tight tolerances and dimensional accuracy. Characteristics Mass-production molds are characterized by their durability, precision, and suitability for high-volume production. Key features of mass-production molds include: Durability: Mass-production molds are typically constructed from robust materials such as hardened steel or aluminum to withstand the rigors of prolonged use and repeated molding cycles without experiencing excessive wear or degradation. Precision: Mass production molds are engineered with precision-machined cavities and cores to ensure uniformity and consistency in the molded parts. Tight tolerances are maintained to meet the strict quality standards required for mass-produced components. High-Volume Capability: Mass production molds are optimized for rapid cycle times and efficient material utilization, allowing for producing large quantities of parts within a short timeframe. This scalability makes them ideal for industries with high demand and production volumes. Process and Technologies Mass production molds leverage advanced manufacturing processes and technologies to achieve high productivity and cost efficiency. Some commonly used techniques include: Injection Molding: Injection molding is a versatile manufacturing process that involves injecting molten material (such as plastic resin) into a mold cavity under high pressure. This process allows for the rapid production of large quantities of complex parts with consistent quality and precise details. Die Casting: Die casting is a metal casting process that involves forcing molten metal into a reusable steel mold (called a die) under high pressure. Die casting is well-suited for producing intricate metal parts with excellent surface finish