What Is CNC?– A Comprehensive Guide
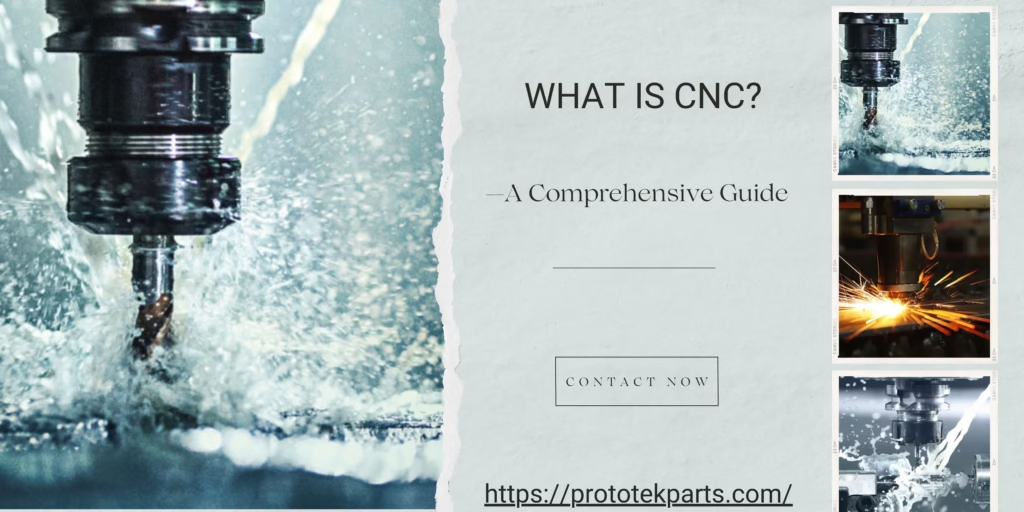
What Is CNC?– A Comprehensive Guide CNC (Computer Numerical Control) technology has emerged as a driving force of modern manufacturing, controlling the movement of machine tools with computers to precisely process complex parts. CNC encompasses various processing methods; two of the more prevalent are CNC milling and turning. What Is CNC? CNC (Computer Numerical Control) is an emerging technology used to operate machine tools precisely via computer programs. Unlike manual operations, it enables more efficient processing of complex parts than is possible through traditional manual means. Typical systems for using CNC include computer control units, drive systems, sensors, and actuators. In addition to machine tools themselves to minimize human errors during automated operations and reduce human mistakes – widely utilized across a range of manufacturing fields for precision parts processing with high production efficiencies. CNC milling and CNC turning are the most common form of CNC processing. 1. CNC Milling CNC milling is a processing technique that utilizes a rotating tool to cut workpieces under computer control, using precise computer programing. Milling machines typically utilize vertical milling, horizontal milling, five-axis milling, or five-axis milling technologies – and can perform complex cutting operations on pieces of various shapes and complexities from metals and plastics alike. Milling can create high-precision surface finishes, which is beneficial in mold making, aerospace production, and automobile assembly – as well as numerous other industries. Face milling This technique involves the milling of flat surfaces that are perpendicular to the cutter axis using cutters with teeth on both the periphery and face, with peripheral teeth performing the cutting action and face teeth providing the finishing touch. Face milling is known for producing high-quality finishes and can be completed either vertically or horizontally. Plain milling (also referred to as Surface or Slab Milling) occurs when the milling cutter axis is parallel with the surface being milled. This process typically occurs with a workpiece mounted directly against the milling machine table with its cutter secured to an arbor standard arbor of standard milling machines. The arbor is held in place horizontally between the milling machine spindle and one or more arbor supports and clamped directly to the table by clamps. Plain milling tools feature teeth on their peripheries as cutting tools. Wide or narrow cutters may be employed, with narrow cutters used for deep cuts while wide cutters provide wider surface coverage. Whenever material needs to be removed in large amounts, an operator typically employs a coarse-toothed cutter with slow cutting speeds and fast feed rates. Followed by finer-toothed cutters with faster cutting speeds and slower feed rates to produce approximate part geometry before switching over to finer-toothed cutters with faster speeds and slower feed rates for details. Angular milling It is used to fabricate flat surfaces by tilting the cutting tool axis at an angle relative to the workpiece surface. A single-angle milling cutter can then create angular surfaces such as chamfers, serrations, grooves, or dovetails depending on design requirements – typically either 45 degrees, 50 degrees 55 degrees, or 60 degrees depending on dovetail milling design specifications. Usually followed by the use of an angle milling cutter that further refines the sides and bases of an angular surface. Form milling It is a milling function designed for irregular surfaces with multiple curves or all curves. It can complete shaping in one cut using a formed milling cutter or fly cutter shaped specifically to the contours of each cut. Commonly half-round recesses and beads on workpieces or quarter-round radii on workpieces using convex, concave, corner rounding cutters that grind to an accurate circular diameter. Form milling can also create intricate patterns or mill multiple complex surfaces at once. Creating intricate patterns or milling several complex surfaces simultaneously using this process. Shaping Hemispherical and semicircular cavities, beads, contours, etc can all be accomplished this way as well. 2. CNC Turning CNC turning is a processing method that involves using a rotating workpiece and a fixed tool for cutting. As opposed to milling, turning is generally used to process parts like shafts and round objects such as shafts. Common types of CNC lathes include turning centers and ordinary lathes. With CNC turning’s precise nature and efficient processing capability, outer circles, inner holes, end faces, outer faces, and other parts can all be efficiently processed at high precision and efficiency levels – perfect for automotive parts, bearings, valves, etc industries alike! The Difference Between CNC Milling and Turning Features CNC Milling CNC Turning Working method The tool rotates, the workpiece is fixed The workpiece rotates, the tool is fixed Applicable workpieces Planes, grooves, complex shapes Shafts, round objects, internal and external circular hole processing Common equipment Vertical milling machine horizontal milling machine five-axis milling machine CNC lathe turning center Advantages Suitable for processing complex shapes with high surface finish Efficient processing of round workpieces with high precision Types of CNC Technology CNC technology is not limited to milling and turning but also includes many other advanced processing methods, such as CNC electrical discharge machining (EDM), CNC laser cutting, CNC wire cutting, etc. These technologies can cope with different materials and processing requirements. For example, EDM is suitable for processing metals with higher hardness, while laser cutting can provide precise cutting capabilities, especially for thin plate processing. Application areas of CNC technology CNC technology has a wide range of applications in many industries: Aerospace: CNC technology can process complex aviation parts, such as aircraft wings, engine components, etc. Automobile manufacturing: In the automotive industry, CNC is used to produce precision engine parts, wheels, etc. Mold manufacturing: CNC can accurately make molds to meet high-quality requirements. Electronic products: The housings and components of electronic equipment are often processed with high precision using CNC technology. Medical equipment: CNC technology helps to manufacture high-precision medical devices, such as surgical tools and implants. If you have any needs, contact us via email at Lynnyao@prototekparts.com or phone: +86-0792-86372550 Tags: Social Network: Recently Posts Online Help! +(86) 0791-86372550 Have Questions? Want To Discuss In Detail? Contact Our Consultant Now CONTACT