Revolutionizing Manufacturing with Aluminum Casting Parts
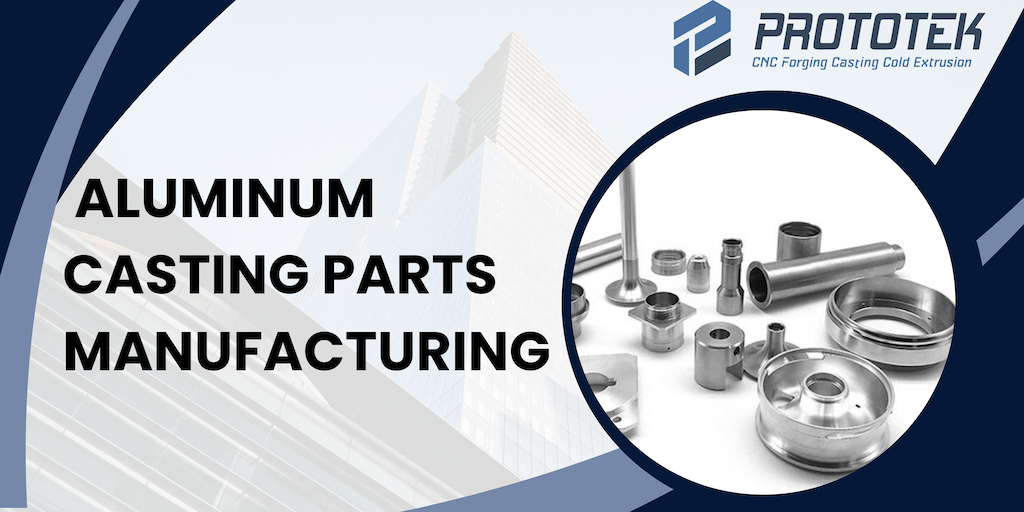
Revolutionizing Manufacturing with Aluminum Casting Parts Aluminum casting parts have emerged as pivotal components in modern manufacturing, offering unparalleled versatility and efficiency across diverse industries. This revolutionary technology leverages aluminum’s inherent properties to deliver lightweight, durable, and intricately designed components crucial in automotive, aerospace, electronics, and various other sectors. Aluminum castings are essential raw materials for equipment production in oil and gas mining, wind power generation, and machinery. They are foundational to the national economy’s basic parts industry, strongly supported by the State. The “14th Five-Year Plan” is a crucial phase for China to achieve industrialization and join the ranks of manufacturing powers. The coordinated development of China’s castings and industries, such as automotive, aerospace, rail transit, equipment manufacturing, and energy, is vital for the domestic manufacturing industry’s growth. Recent policies like the “Guiding Opinions on Promoting the High-Quality Development of the Casting and Forging Industry” and “Guiding Opinions on Accelerating the Green Development of the Manufacturing Industry” encourage enterprises to conduct core technology research, improve casting technology and equipment, and enhance innovation capabilities. These policies promote industrial structure optimization, industry regulation, green and low-carbon transformation, and rapid industry development. Industrial Chain The casting industry relies on upstream raw materials such as steel, copper, and aluminium. Fluctuations in steel prices significantly impact the industry’s overall gross margin. With socio-economic development and industrial manufacturing innovations, the precision casting industry’s downstream application fields have expanded, encompassing instrumentation, shipbuilding, automotive, construction machinery, oil and gas, and aerospace sectors. Market Analysis and Advantages The global market for aluminum casting parts has witnessed significant growth driven by the expanding automotive and aerospace sectors. Lightweighting initiatives aimed at improving fuel efficiency and reducing emissions have propelled the demand for aluminium components. Moreover, aluminium’s recyclability aligns with sustainable manufacturing practices, further boosting its popularity. Domestic and International Applications In the domestic market, aluminium casting parts are extensively used in the automotive industry for engine components, transmission housings, and structural parts due to their high strength-to-weight ratio. Internationally, aerospace applications capitalize on aluminum’s corrosion resistance and thermal conductivity, making it ideal for aircraft structural components and interiors. Casting Industry Development Trends a. Increased Industry Concentration and Scaling Despite a large number of enterprises, China’s foundry industry has seen a reduction in smaller, less efficient companies due to national environmental protection regulations and market stabilization. According to the “14th Five-Year” development plan by the China Foundry Association, there are more than 1,000 enterprises with annual casting production exceeding 10,000 tons and nearly 200 enterprises with over 50,000 tons. The trend towards industrial concentration and scaling is evident. b. Industrial Transformation Towards Intelligence and Digitization The integration of artificial intelligence and digital technologies with manufacturing is a significant trend. Utilizing advanced technologies and modern machinery, such as 3D printing and digital production workshops, helps reduce labour costs, improve product quality, decrease energy consumption, enhance production efficiency, and promote industry upgrades. c. Case Studies and Success Stories Several companies have successfully integrated aluminium casting technologies. In the automotive sector, leading manufacturers have achieved substantial weight reductions without compromising performance or safety. In aerospace, aluminium casting adoption has streamlined production processes and enhanced aircraft efficiency and reliability. d. Future Prospects and Innovations Future advancements in aluminum casting technologies will likely focus on enhancing material properties, optimizing production cycles, and expanding design capabilities. Innovations like rapid prototyping and 3D printing are poised to revolutionize manufacturing, enabling faster development and customization of aluminium casting parts to meet evolving market demands. Aluminium casting parts represent a cornerstone of modern manufacturing, offering unparalleled versatility, durability, and sustainability across various industries. As global industries prioritize lightweight materials and sustainable practices, aluminium casting remains at the forefront, driving innovation and reshaping the future of engineering and manufacturing. Jiangxi Prototek Imp and Exp Co. Ltd Prototek is a leading innovator in aluminium casting technology, dedicated to delivering cutting-edge solutions that redefine manufacturing excellence. With a commitment to quality, sustainability, and customer satisfaction, Prototek continues to pioneer advancements in aluminium casting parts, empowering industries worldwide to achieve new heights of performance and efficiency. If you have any needs, contact us via email at Lynnyao@prototekparts.com or phone: +86-0792-86372550 Tags: Social Network: Recently Posts Online Help! +(86) 0791-86372550 Have Questions? Want To Discuss In Detail? Contact Our Consultant Now CONTACT