Core Applications of CNC Machining in The Automotive Industry
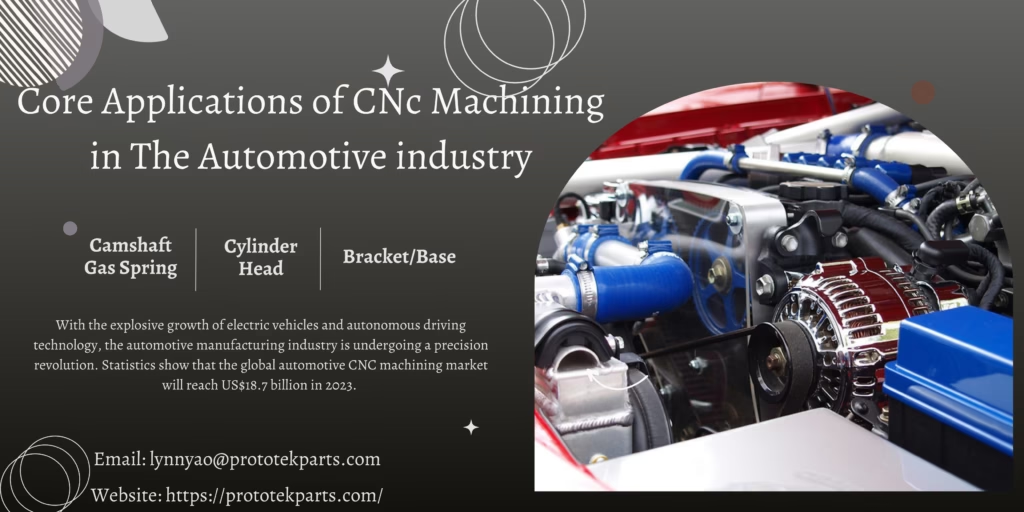
Core Applications of CNC Machining in The Automotive Industry Advantages of CNC Machining for the Automotive Industry High precision and consistency CNC machining controls the movement of mechanical equipment through computer numerical control programs, which can achieve extremely high precision and repeatability. For automotive parts, precision is critical, especially in key systems such as engines, transmissions, chassis, etc. Precision parts such as engine cylinders, brake systems, transmission gears, etc. High production efficiency CNC machining has a high degree of automation and can work 24 hours a day (under proper maintenance and management). It is much more efficient than traditional manual processing methods. Through mass production, CNC machining can significantly reduce the production cycle, and in multi-variety small batch production, the setting and adjustment time of CNC equipment is relatively short, which improves production flexibility. Mass production of automotive parts, such as car wheels, suspension systems, etc. Processing capabilities of complex parts CNC machining can efficiently process parts with complex shapes and geometries, which is essential for the manufacture of many complex parts in modern automotive designs. Traditional processing methods may not be able to handle complex curves or small holes, but CNC technology can easily meet these challenges. Engine parts (such as cylinder blocks, and pistons) and body structural parts. Reduce manual errors Since CNC machining is controlled by computers, errors and deviations in manual operations are reduced. This is especially important for the automotive industry, as any minor error may result in unqualified products and affect the performance and safety of the car. various precision parts, especially those that require high safety and reliability (such as brake systems, airbag components, etc.). Flexibility and customized production CNC machining is not only suitable for large-scale production but also flexible for small-batch customized production. For the automotive industry, when producing parts of various models and styles, the flexibility of CNC machining can be quickly adjusted according to different product requirements, avoiding stagnation of production lines and waste of resources. customized production of chassis components, engine accessories, and interior accessories for different models. High material utilization CNC machining can maximize material utilization by precisely controlling the cutting process. Compared with traditional machining methods, CNC machining can usually reduce waste and reduce material costs more effectively. Processing parts of high-strength steel or aluminum alloy materials reduces the waste of raw materials. Complex surface treatment capabilities CNC machining can not only realize the manufacturing of complex shapes but also can be combined with surface treatment processes (such as spraying, anodizing, coating, etc.) to complete high-demand surface quality treatment. Surface treatment of body appearance parts, engine housings, wheels, and other parts. Rapid prototyping and sample manufacturing CNC machining can quickly produce prototypes and samples, helping design engineers to quickly verify design concepts in the early stages of automotive product development. Through feedback on samples, designs can be adjusted in time to avoid errors in the later production process, thereby accelerating the product development process. Rapid manufacturing of engine prototypes, body design samples, internal structural parts, etc. Improve product quality and consistency CNC machining ensures the consistency of the processing process and reduces deviations caused by human operations, especially in mass production. Automakers mass-produce parts with high precision requirements such as engines, transmissions, and brake systems. Reduce tool wear and increase tool life CNC machining can extend tool life by optimizing cutting parameters, thereby reducing the frequency and cost of tool replacement. The processing of precision aluminum alloy parts produced in large quantities can extend tool life and reduce the frequency of replacement. How is CNC machining used for prototyping in the automotive industry? CNC machining plays a vital role in automotive prototyping, which can quickly and accurately produce functional prototypes and help engineers verify design concepts. Through CNC machining, automakers can produce high-precision prototypes in a short time for testing, evaluation and modification, reducing development costs and shortening R&D cycles. Here are the specific ways how CNC machining is used for automotive prototyping: Rapid prototyping CNC machining can create prototypes based on CAD data (computer-aided design) in a shorter time. By importing design files directly into CNC equipment, the machine can accurately perform operations such as cutting, drilling, milling, etc. to produce precise prototype parts. Compared with traditional manual methods, CNC machining is faster and can complete the processing of multiple complex parts in one operation. Application scenarios: For example, design prototypes of automotive exterior and interior parts, such as dashboards, door linings, engine components, etc. Design verification and testing CNC machining can produce prototypes that are almost identical to the final product, which allows automakers to perform functional verification and performance testing before production. The prototype can be tested for structural strength, assembly, aerodynamics, etc. to ensure the feasibility of the design. Through actual testing, engineers can find design defects earlier and avoid expensive modifications later. Application scenarios: body aerodynamic performance test, collision test, component assembly verification, etc. Integrated testing and assembly The high precision and high consistency of CNC machining ensure that the various components can be assembled together smoothly, so that the prototype can pass more complex assembly and functional tests. CNC machining can be used to make multiple components and can be integrated and assembled at the prototype stage to verify the overall working performance of the automotive system. Application scenarios: Integrated assembly and testing of engines, wheels, suspension systems, etc. during the development process. Which auto parts can be mass-produced using CNC machining technology? Automotive machining can manufacture several other automotive parts, including but not limited to suspension components, exhaust components, carburetor housings, fluid system components, bushings, and valve retainers. This manufacturing technology is also particularly useful for customizing vehicles and their specific automotive parts, as CAD allows for rapid changes in part design and the manufacture of custom parts. Transmission Components: CNC machining is fundamental to prototyping transmission components such as gears and clutches. Precision is critical to ensure that the parts can withstand the stress of operation without failure. CNC technology allows for rapid prototyping and testing of