The Ultimate Knowledge of Stainless Steel Machining Parts
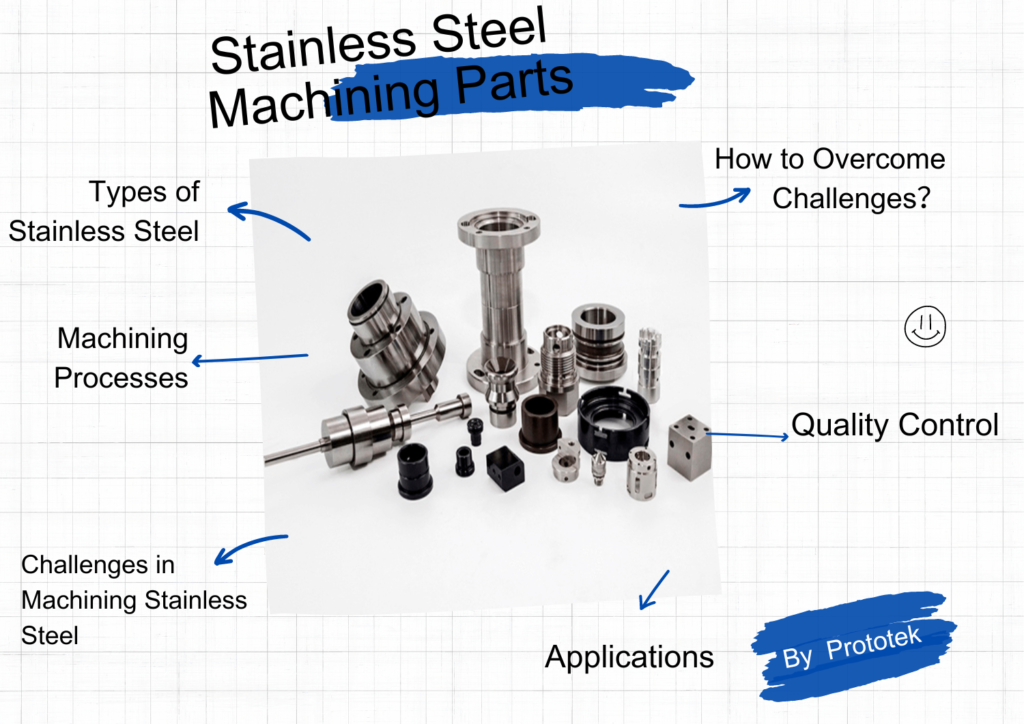
Blog Details Stainless steel machining parts are essential for various industries due to their durability, corrosion resistance, and aesthetic appeal. These parts are crafted using various machining processes, ensuring they meet the precise specifications required for different applications. Understanding the types of stainless steel used, the machining processes, and the challenges involved can help you make informed decisions about using stainless steel for your projects. Types of Stainless Steel Used in Machining Stainless steel comes in various grades, each offering unique properties suitable for different applications and machining processes. Understanding the characteristics of these grades can help select the right type of stainless steel for specific needs. 304 Stainless Steel Properties and Advantages Composition: Contains 18% chromium and 8% nickel, making it an austenitic stainless steel. Corrosion Resistance: High resistance to corrosion, particularly against various acids found in food processing environments. Weldability: Excellent weldability without the need for post-weld annealing. Formability: Good formability, making it easy to shape and fabricate. Temperature Tolerance: Performs well in both high and low temperatures. Typical Uses Food Processing Equipment: Due to its resistance to corrosion and ease of cleaning, it is widely used in kitchen sinks, countertops, and brewing equipment. Chemical Containers: Suitable for storing chemicals that are not highly corrosive. Architectural Applications: Used in exterior accents and structures due to its aesthetic appeal and durability. 316 Stainless Steel Properties and Advantages Composition: Contains 16% chromium, 10% nickel, and 2% molybdenum, which enhances its corrosion resistance. Enhanced Corrosion Resistance: Superior resistance to chlorides and industrial solvents, making it ideal for harsh environments. Strength and Durability: Maintains strength and toughness at both high and low temperatures. Weldability and Fabrication: Similar to 304, it has good weldability and is easy to fabricate. Typical Uses Marine Applications: Often used in marine environments due to its resistance to saltwater corrosion. Medical Devices: Common in surgical instruments and implants because of its biocompatibility. Chemical Processing: Used in equipment that handles corrosive chemicals. 410 Stainless Steel Properties and Advantages Composition: Contains 11.5% to 13.5% chromium, making it a martensitic stainless steel. High Strength: Known for its high mechanical strength and hardness. Heat Treatment: Can be heat treated to achieve a wide range of hardness and mechanical properties. Moderate Corrosion Resistance: Provides adequate resistance to corrosion for many applications. Typical Uses Cutlery and Tools: Used in the production of knives and cutting tools due to its hardness. Surgical Instruments: Suitable for certain surgical instruments that require high strength. Valves and Pumps: Used in manufacturing parts that require both strength and moderate corrosion resistance. 416 Stainless Steel Properties and Advantages Composition: Contains 12-14% chromium and added sulfur, making it a free-machining variation of 410. Machinability: Enhanced machinability due to the addition of sulfur, which improves chip breaking. High Strength: Retains the high strength and hardness characteristics of 410. Corrosion Resistance: Similar to 410, with adequate resistance for many applications. Typical Uses Fasteners: Commonly used in screws, bolts, and other fasteners that require precise machining. Gears: Ideal for gears and shafts due to its machinability and strength. Automotive Components: Used in various automotive parts where machinability and moderate corrosion resistance are needed. Comparison of Different Grades Each grade of stainless steel offers distinct properties, making them suitable for different machining and application requirements: 304 vs. 316: While both are austenitic and highly corrosion-resistant, 316 offers superior resistance to chlorides and harsh chemicals due to adding molybdenum. This makes 316 more suitable for marine and medical applications. 410 vs. 416: Both are martensitic and offer high strength, but 416’s enhanced machinability makes it preferable for parts requiring intricate machining. However, it has slightly lower corrosion resistance compared to 410. Overall: The choice between these grades depends on factors such as corrosion resistance requirements, strength, machinability, and the specific environmental conditions the parts will be exposed to. Machining Processes for Stainless Steel Parts Machining stainless steel involves various techniques that shape and form the material to meet specific design and functional requirements. Each process offers distinct advantages and is chosen based on the desired outcome of the machined parts. Turning Turning is a machining process where a cutting tool removes material from a rotating stainless steel workpiece. This process is typically performed on a lathe, which creates cylindrical parts. Process Details Lathe Setup: The workpiece is secured in a chuck and rotated at high speed. Tool Movement: A cutting tool moves linearly along the axis of rotation to remove material. Precision: Allows for high precision and smooth finishes. Applications Shafts and Rods: Commonly used for producing shafts, rods, and other cylindrical components. Threaded Parts: Ideal for creating threads on screws, bolts, and other fasteners. Milling Milling involves using rotary cutters to remove material from a stationary workpiece. This versatile process can produce a wide range of shapes and features. Process Details Milling Machines: Utilizes either horizontal or vertical milling machines. Cutting Tools: Employs various cutting tools such as end mills, face mills, and ball nose cutters. Movement: The workpiece can move along multiple axes to achieve the desired shape. Applications Complex Shapes: Suitable for parts with complex geometries, slots, holes, and pockets. Flat Surfaces: Often used to create flat surfaces, grooves, and intricate patterns. Drilling Drilling creates holes in stainless steel parts using rotary cutting tools called drill bits. Process Details Drill Press: Performed using a drill press or a CNC machine. Drill Bits: Various drill bits, such as twist and center drills, are used. Coolant Use: Coolants are often applied to reduce heat and improve tool life. Applications Fastener Holes: Commonly used for creating holes for screws, bolts, and other fasteners. Fluid Passages: Essential for parts requiring precise fluid or gas passages. Grinding Grinding uses abrasive wheels to achieve high surface quality and precise dimensions on stainless steel parts. Process Details Abrasive Wheels: Different abrasive wheels, such as grinding wheels and belts, are used. Surface Finish: Capable of achieving very fine surface finishes. Precision: Provides high dimensional accuracy and smooth surfaces. Applications Surface Finishing: Often used as a finishing process to achieve the