Qual è la differenza tra forgiatura ed estrusione?
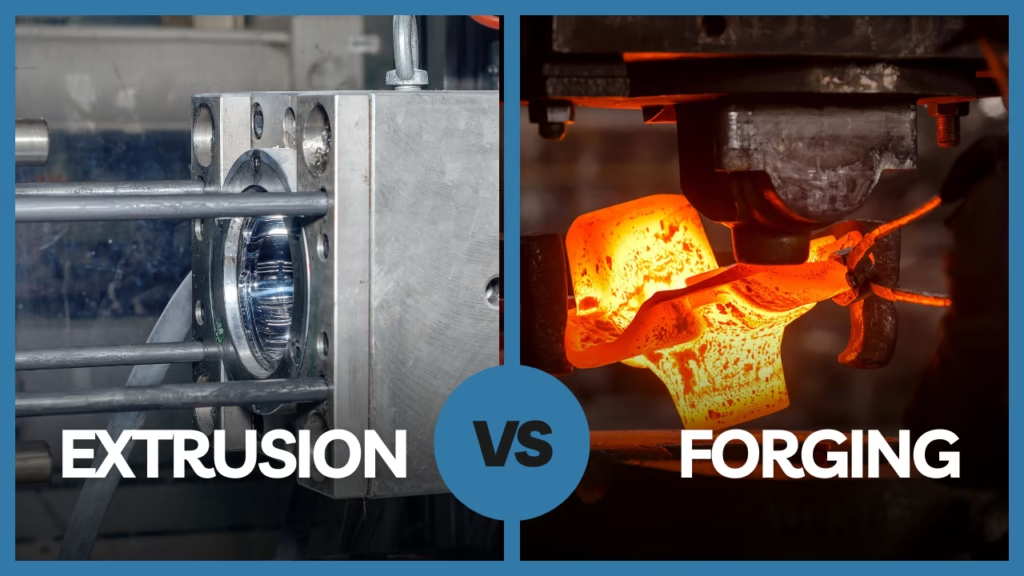
What is the Difference Between Forging and Extrusion Definition and Process Overview ✅ Forging Definition: Forging is a manufacturing process in which metal is shaped by compressive forces, usually applied with a hammer, press, or die. Process: The metal is heated to a malleable temperature (for hot forging) or processed at room temperature (for cold forging). It is then shaped using impact or pressure to achieve the desired form. Can be done manually (open-die forging) or with precision dies (closed-die forging). ✅ Extrusion Definition: Extrusion is a manufacturing process where metal is pushed or drawn through a die to create objects with a constant cross-sectional profile. Process: The material is either heated (hot extrusion) or kept at room temperature (cold extrusion). It is forced through a mold or die opening, creating a continuous shape with a uniform cross-section. Common for producing rods, pipes, and complex profiles. What is extruded aluminum? Extrusion, including extruded aluminum, is a process that forms a product with a fixed cross-sectional profile over its entire length. The process starts with a fixed-shape die and a length of stock (usually a round stock) that is forced through the die to conform to its shape. This requires the stock to be larger than the shape of the die, so it is simultaneously narrowed and shaped by thick steel dies and powerful presses. A sister process to extrusion is called “drawing,” which simply pulls the stock through the die, rather than pushing it through it. This process often limits the number of consecutive extrusion steps that can be performed quickly and is usually only used for simpler extruded shapes, such as wire and round tubes. Extrusion can be performed on hot or cold material, but hot extrusion is essential for materials with complex shapes and drastic shape changes. Extrusion can be performed on many different types of materials and is very useful for producing tubing and small or medium-sized identical parts that can be cut from a long extruded billet. The surface finish of the extruded billet is very good, and brittle materials can be easily extruded due to the support of the die and the simple forces present during the extrusion process. What is Forging? Forging is the process of forming metal into a specific shape using heat and pressure, through which forging transforms the raw metal without melting it. Forging is therefore often similar to the extrusion process, but forging usually only processes one part at a time. Forging is similar to extrusion and can include the use of multi-ton presses, but can also fall under the umbrella of hammer forging and roll forging: Hammer forging: Hammer forging uses a powerful steam, electricity, or air pressure-driven hammer to strike the workpiece quickly and repeatedly. This can quickly reshape heavy or thick metal pieces with a smaller hammer and lower overall pressure than required with a press. However, hammer forging is only used for open-die forging. Press forging: A press applies continuous force to the top and bottom of the material to shape it. Generally, a press requires higher power input and more pressure than a hammer but can reshape the material into a variety of shapes and has more forming capabilities than a hammer. Press forging can be used with open dies (the die does not surround the workpiece) or closed dies (the die surrounds the workpiece). Closed presses are almost always used to create parts with three-dimensional shapes. Roll Forging: Roll forging is the process of heating a material and passing it through heavy steel rolls to reduce the size and lengthen the material. Roll forging does not necessarily produce round parts; roll forging can produce square and rectangular billets, and patterns can be added to the rolls to impart that pattern to the workpiece. Key differences What is the difference between forging and extrusion? Due to the properties of aluminum, extrusion and forging can subject aluminum billets to very high stresses that other metals, such as steel, cannot withstand. Aluminum’s ductility and elasticity make it an ideal material for extrusion and forging. Aluminum can also take on more complex and extreme shapes than steel without suffering possible damage. So what are the advantages of forged aluminum over extruded aluminum? There are two main ones: Complex Forming: The disadvantage of metal extrusion is that it requires a round billet and a specific set of die standards. Creating a center hole or other closed cavity in the center of the billet requires complex tooling, and other complex shapes are impossible to extrude. In contrast, forging can easily produce these shapes with minimal complex engineering. Closed-die forging, in particular, can produce almost any shape that may be difficult to produce with extrusion. In addition, forging works in three dimensions, while extrusion only works in two dimensions, which means that angles that are impossible in extrusion can be easily produced with forging. Versatility: Due to the difference in forming capabilities, extrusion is not practical for many common forms and shapes. Extrusion is suitable for long or tubular shapes that require a consistent 2D cross-sectional shape that can be cut into many parts but is not suitable for anything that requires 3D shapes or angles. Converting extruded aluminum to these shapes requires a complex post-extrusion process that nearly negates the speed gains of the extrusion process. Extrusion is a necessary process for forming metal for specific uses. However, many of the most common applications in the aerospace industry require strong and complex parts that cannot be achieved with the extrusion process. Feature Forging Extrusion Process Type Shaping by compressive force Shaping by pushing through a die Material Flow Deformation occurs by compression Deformation occurs by flow through a die Shape Produced Complex,non-uniform shapes Uniform cross-sectional shapes Temperature Can be hot or cold forging Can be hot or cold extrusion Strength High-strength parts due to grainrefinement Good strength but lower than forged parts Precision Less precise than extrusion Highly precise and consistent cross. sections Surface Finish Rougher surface finish Smoother surface finish