Exploring Metal Stamping Services: From Concept to Practice
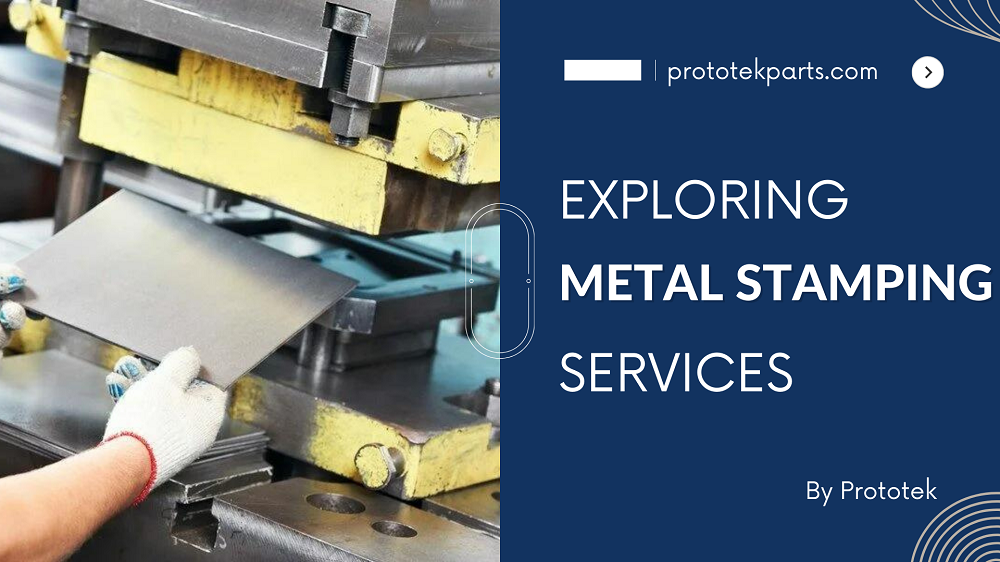
Blog Details Metal stamping services are pivotal in manufacturing, offering efficient solutions for shaping metal components. This article delves into the intricacies of metal stamping, exploring its significance, applications, and considerations for selecting the right service provider. What is Metal Stamping? Metal stamping is a versatile manufacturing process that converts flat metal sheets into various shapes and forms. It involves using presses, dies, and tooling to apply force and manipulate the metal into the desired configuration. The process is commonly employed in automotive, aerospace, electronics, and appliances industries to produce a wide range of components with high precision and efficiency. Process Overview The metal stamping process typically begins with a flat sheet or coil of metal, which is fed into a stamping press. The press applies force to the metal using specialized dies, which are machined to the precise shape and dimensions of the desired part. The metal undergoes various operations such as blanking, piercing, forming, and bending as it progresses through the dies. Each operation is carefully controlled to achieve the desired shape and dimensions of the final part. Blanking and Piercing Blanking is the process of cutting the metal into a specific shape while piercing involves creating holes or openings in the metal sheet. These operations are typically performed in the initial stages of the stamping process to create the basic outline of the part and prepare it for further forming operations. Forming and Bending Forming and bending operations shape the metal into complex geometries and contours. This is achieved by applying controlled pressure to the metal using specialized tooling, which deforms the metal into the desired shape. Forming operations can include drawing, stretching, and deep drawing, depending on the part’s complexity. Secondary Operations After the primary forming operations are complete, the stamped parts may undergo secondary operations such as trimming, machining, welding, or assembly to achieve the final desired specifications. These secondary operations are often necessary to remove excess material, refine features, or join multiple components together. Components of Metal Stamping Presses Presses are the primary machines used in metal stamping, applying force to the metal to deform it into the desired shape. Presses can vary in size and capacity, ranging from small mechanical presses to large hydraulic or servo-driven presses capable of exerting thousands of tons of force. Dies Dies are specialized tooling components that shape and form metal during stamping. They consist of two main parts: the punch, which applies force to the metal, and the die, which provides the desired shape and support for the metal as it is formed. Depending on the application’s requirements, dies can be made from various materials such as tool steel, carbide, or ceramic. Tooling Tooling refers to the various components and accessories used with the presses and dies to facilitate stamping. This includes feeders, grippers, sensors, and safety devices, which help automate and control the stamping operation, ensuring consistent quality and productivity. Advantages of Metal Stamping Metal stamping offers several advantages over other manufacturing processes, including: High Precision: Metal stamping can achieve tight tolerances and intricate geometries, ensuring consistent quality and accuracy in the finished parts. Cost Efficiency: Stamping allows for high-volume production at relatively low per-part costs, making it economical for mass-production applications. Versatility: Metal stamping can be used with various metals, including steel, aluminum, copper, and stainless steel, in various thicknesses and grades. Speed and Efficiency: Stamping processes can be highly automated, allowing for fast cycle times and high production rates, reducing lead times and time-to-market for new products. Types of Metal Stamping Services Single-step Stamping Single-step stamping, or blanking or shallow drawing, involves completing the entire shaping process in a single stroke of the press. This method suits simpler designs and involves basic operations such as cutting, bending, or forming the metal sheet into the desired shape. Single-step stamping often produces flat or shallow parts with minimal complexity. Progressive Stamping On the other hand, progressive stamping is a more advanced technique involving multiple steps or operations performed in sequential dies. As the metal sheet progresses through the press, it undergoes successive operations such as blanking, piercing, forming, and bending in different stages. Each die in the progression performs a specific operation, gradually shaping the metal into the final desired form. Progressive stamping is ideal for producing complex, intricate parts with tight tolerances and high precision. Custom Stamping Custom stamping services cater to unique specifications and low-volume orders, offering flexibility and customization options to meet customers’ specific needs. Custom stamping involves working closely with the client to design and manufacture parts tailored to their requirements, often involving prototype development, tooling design, and testing to ensure the final product meets quality standards. Production Stamping On the other hand, production stamping focuses on the high-volume manufacturing of standardized parts for mass-production applications. Production stamping services are optimized for efficiency, consistency, and cost-effectiveness, emphasizing high-speed operation and repeatability. These services are typically used for producing large quantities of parts with consistent quality and performance, often using automated equipment and processes to maximize productivity. Considerations for Choosing the Right Stamping Service Complexity of Parts The complexity of the parts to be produced is a key factor in determining the type of stamping service required. For simple designs with minimal features, single-step stamping may be sufficient, while complex parts with intricate geometries may require progressive stamping for precision and accuracy. Volume and Scale of Production The volume and scale of production also influence the choice between custom and production stamping services. Custom stamping may be more suitable for low-volume or custom orders, offering flexibility and customization options. Production stamping is often more cost-effective and efficient for high-volume production runs, allowing for large quantities of parts to be produced quickly and consistently. Quality and Precision Requirements The quality and precision requirements of the final parts are critical considerations when selecting a stamping service provider. Both single-step and progressive stamping can achieve high levels of accuracy and repeatability, but the specific capabilities and expertise of the service provider may vary. Choosing a