Why Is Stainless Steel So Hard to Machine?
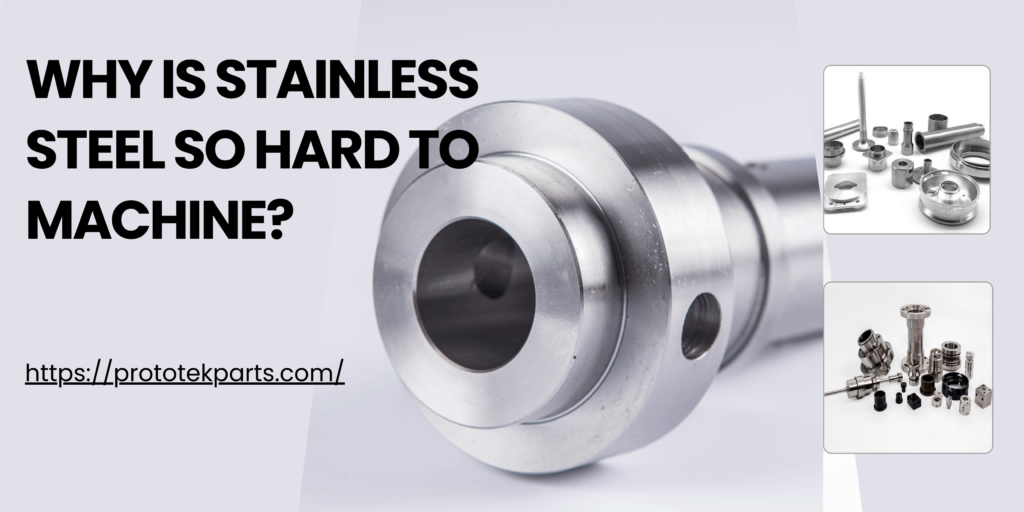
Why is Stainless Steel So Hard To Machine Stainless steel is a material renowned for its durability, corrosion resistance, and sleek appearance. It is a major processed product in industries ranging from aerospace to food processing. However, despite its many advantages, machining stainless steel poses significant challenges. As industries increasingly depend on this versatile metal, understanding the intricacies of its machinability becomes essential. This article delves into why stainless steel is so hard to machine and explores the strategies and technologies being developed to address these difficulties. The History and Development of Stainless Steel The history of stainless steel dates back to the early 20th century when German metallurgists Benno Strauss and Eduard Maurer first developed the precursor to modern stainless steel, known as 20-7 stainless steel. This early alloy contained 18% chromium and 8% nickel, leading to the development of the widely used 18/8 stainless steel (also known as 304 stainless steel). The addition of chromium and nickel to iron-based alloys significantly enhanced their corrosion resistance, making them suitable for a range of applications in industries such as construction, automotive, and aerospace. Over the years, advancements in metallurgical technology have led to the development of numerous stainless steel grades, each tailored with unique properties for specific applications. For example, the addition of molybdenum in 316 stainless steel further improves its corrosion resistance, making it ideal for use in harsh environments. Today, stainless steel remains a crucial material across various industries due to its versatility, durability, and corrosion resistance (Strauss and Maurer, 1912; International Stainless Steel Forum, 2021). Types and Grades of Stainless Steel Stainless steel is a versatile material with a wide range of applications due to its unique combination of properties, including corrosion resistance, strength, and ductility. There are over 150 different types and grades of stainless steel, broadly categorized into five groups: austenitic, ferritic, martensitic, duplex, and precipitation-hardening. Austenitic stainless steels, such as grades 304 and 316, are the most commonly used due to their excellent formability and corrosion resistance. Ferritic stainless steels (e.g., grade 430) are known for their good corrosion resistance and magnetic properties but have lower strength and ductility. Martensitic stainless steels (e.g., grade 420) offer high strength and hardness but have lower corrosion resistance. Duplex stainless steels (e.g., grade 2205) combine the properties of both austenitic and ferritic stainless steels, providing high strength and excellent corrosion resistance. Precipitation-hardening stainless steels (e.g., 17-4 PH) offer a unique combination of high strength and corrosion resistance through heat treatment. Each type and grade of stainless steel has specific attributes that make it suitable for a variety of applications, from kitchen utensils to aerospace components (ASM International, 2017; International Stainless Steel Forum, 2021). The Nature of Stainless Steel Stainless steel is primarily composed of iron, carbon, and chromium. The chromium content, which is typically at least 10.5%, is what gives stainless steel its corrosion-resistant properties. Additionally, various grades of stainless steel contain other alloying elements such as nickel, molybdenum, and manganese. which further enhances its properties but also complicates the machining process. One of the key factors affecting machinability is the microstructure of stainless steel. Stainless steel is available in several grades, including austenitic, ferritic, martensitic, and duplex. Each of these has different properties: Austenitic Stainless Steel: Known for its excellent corrosion resistance and good machinability, but it can be challenging to machine due to its work-hardening properties. Ferritic Stainless Steel: Generally easier to machine than austenitic steel but can still be challenging due to its brittleness. Martensitic Stainless Steel: Harder and more abrasive, which makes it more difficult to machine. Duplex Stainless Steel: Combines properties of both austenitic and ferritic stainless steels, offering high strength but also posing significant machining challenges. Factors Contributing to Machining Difficulty Work Hardening: Austenitic stainless steel is particularly notorious for work hardening. As it is machined, the material’s surface becomes harder due to the deformation, which can rapidly dull cutting tools and lead to excessive tool wear. This work hardening necessitates frequent tool changes and can increase production costs and time. High Strength and Toughness: Stainless steel has a high tensile strength and toughness, making it resistant to cutting. Tools need to exert significant force to cut through the material, which can lead to tool deflection, increased friction, and more rapid tool wear. Thermal Conductivity: Stainless steel has relatively poor thermal conductivity, meaning that heat generated during machining is not easily dissipated. This can lead to high temperatures at the cutting edge, further exacerbating tool wear and potentially causing thermal damage to the workpiece. Chipping and Cracking : Due to its brittleness in certain grades and the stress induced during machining, stainless steel can be prone to chipping and cracking, which can affect the surface finish and dimensional accuracy of the machined parts. Chip Formation: Stainless steel often produces long, stringy chips that can interfere with the machining process, leading to additional handling and disposal issues. Effective chip removal is crucial to prevent re-cutting and ensure a smooth operation. Strategies and Technological Advances Addressing the challenges of machining stainless steel requires a combination of advanced techniques and technologies: Optimized Cutting Conditions: Adjusting cutting speeds, feeds, and depths can significantly impact machining efficiency. For instance, lower cutting speeds and higher feed rates can help mitigate work hardening. Additionally, using appropriate cutting fluids can aid in cooling and reducing friction. High-Performance Cutting Tools: Tools made from high-speed steel (HSS) or carbide with specialized coatings, such as titanium nitride (TiN) or titanium carbonitride (TiCN), are designed to withstand the harsh conditions associated with machining stainless steel. These tools offer enhanced durability and reduced wear. Advanced Machining Techniques: Techniques such as high-pressure coolant systems and cryogenic cooling are being explored to manage heat and improve tool life. High-pressure coolant can reduce temperature and clear chips effectively, while cryogenic cooling involves using extremely cold temperatures to maintain tool sharpness and improve machining performance. Innovative Tool Materials and Coatings: The development of new tool materials and coatings continues to advance. For example, tools with diamond-like carbon