All About Brass as a CNC Manufacturing Material
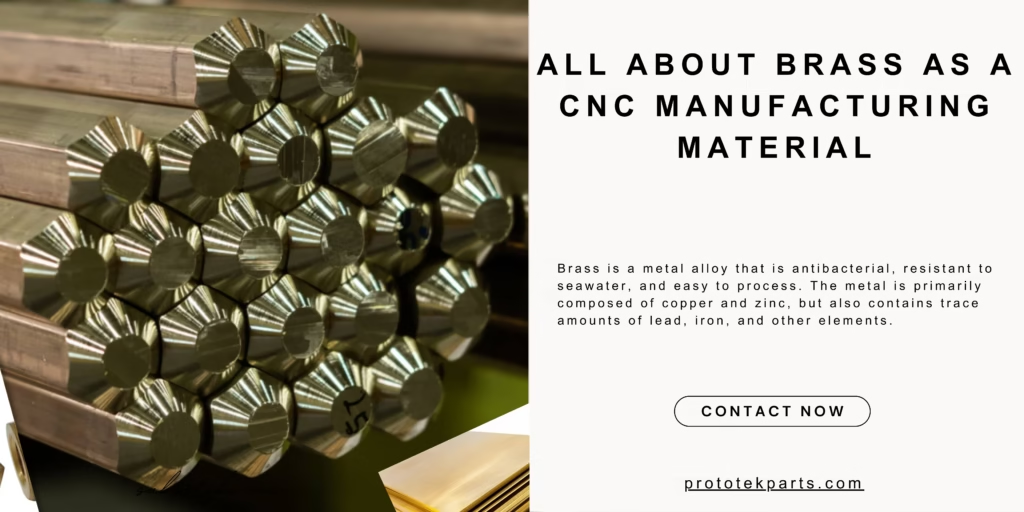
All About Brass as a CNC Manufacturing Material Brass is a metal alloy that is antibacterial, resistant to seawater, and easy to process. The metal is primarily composed of copper and zinc, but also contains trace amounts of lead, iron, and other elements. In 2024, the United States became the world’s sixth largest brass producer, with a total production of 1.1 million tons, a year-on-year decrease of 10%. The largest is Chile (5.3 million metric tons), followed by Congo (3.3 million metric tons) and Peru (2.6 million metric tons). What is brass Brass is a workable, machinable, antibacterial, and anti-biofouling material. As we briefly introduced in the introduction, brass is a metal alloy of copper and zinc, usually golden yellow, but may appear red if the alloy contains a lot of copper. This type is called “red brass”. The content of copper and zinc (or other alloying elements) in brass will determine its type and characteristics. Lead in brass improves its corrosion resistance and machinability while adding iron will make it harder and easier to forge. Due to its excellent mechanical properties, corrosion resistance, and good electrical conductivity, it is widely used in machinery manufacturing, electronic appliances, architectural decoration, musical instruments, and automotive industries. Types of brass: Common brass: Composed of copper and zinc, the zinc content is between 20% and 40%. The higher the zinc content, the higher the strength, but the plasticity decreases. 260 alloy (Cartridge Brass) Composition: 70% Cu, 30% Zn Features: good toughness, deep drawing, good corrosion resistance Application: bullet shells, pipes, decorative parts 280 alloy (Muntz Brass /Muntz Metal) Composition: 60% Cu, 40% Zn Features: high strength, seawater corrosion resistance Application: ship accessories, marine industry, architectural decoration Special brass: It refers to the addition of lead (Pb), aluminum (Al), iron (Fe), silicon (Si), and other elements to a copper-zinc alloy to improve wear resistance, corrosion resistance, or strength. C360 alloy (Free-Machining Brass) Composition: 61.5% Cu, 35.5% Zn, 3% Pb (lead) Features: Adding lead (Pb), extremely easy to cut, suitable for precision machining Application: automatic lathe processing parts, bolts, nuts, electrical connectors (lead improves machinability) 385 alloy (Architectural Bronze) Composition: 57% Cu, 40% Zn, 3% Pb Features: Lead-containing, easy to process, strong weather resistance, suitable for architectural decoration Application: door and window frames, handrails, architectural decoration (lead improves machinability) 464 brass (Naval Brass) Composition: 60% Cu, 39% Zn, 1% Sn (tin) Features: Adding tin (Sn) to improve seawater corrosion resistance Application: ship parts, propellers, seawater pipelines (tin improves seawater corrosion resistance) Properties of Brass . Alloy 260 Alloy 280 Alloy 360 Alloy 385 Alloy 464 Composition (wt %) Cu: 68.5 – 71.5 Zn: 28.5 – 31.5 Fe <= 0.05 Pb <= 0.070 Cu: 59 – 63 Zn: 40 Fe <= 0.070 Pb <= 0.3 Cu: 60-63 Zn: 35.5 Fe <= 0.35 Pb <= 2.5-3.7 Cu: 55 – 59 Zn: 36.65-41.65 Fe <= 0.35 Pb <= 2.5-3.5 Cu: 55 – 59 Zn: 36.65 – 41.65 Zn Fe <= 0.35 Pb <= 2.5-3.5 Density (g/cm3) 8.53 8.39 8.49 8.47 8.41 Hardness, Rockwell (F, B) 54 F 85 F 78 B 65 B 55 B Yield Strength (MPa) 75 145 124-310 138 172-455 Ultimate Tensile Strength (MPa) 300 370 338-469 414 379-607 Elongation @ Break (%) 68 45 53 30 50 Modulus of Elasticity (GPa) 110 105 97 – 100 Machinability (%) 30 40 100 90 30 Common applications of brass: Hardware parts: nuts, screws, valves, bearings, etc. Electronic and electrical: connectors, terminals, heat sinks, etc. Architectural decoration: door handles, lamps, railings, etc. Musical instruments: brass instruments such as trumpets, saxophones, trombones, etc. Shipping industry: propellers, seawater pipes, etc. (special brass resistant to seawater corrosion Advantages and disadvantages Brass has many advantages. In addition to being one of the easiest materials to machine (easy-to-machine brass has a 100% machinability rating), it also has a low coefficient of friction (in layman’s terms, it has a very smooth surface, making it ideal for parts that need to slide against each other without wearing out quickly). The copper content in brass can kill certain types of bacteria, making it a go-to material for high-contact surfaces like door handles. It’s also used in the marine industry due to its biofouling properties, which means algae and barnacles won’t grow on it. The main disadvantage of brass is that it tarnishes easily; if not properly cared for, brass can develop unsightly black stains from oxidation. To prevent this, many people apply a layer of varnish to their brass. Brass is also not hypoallergenic (thanks to the copper and zinc) and may cause some skin irritation for those with sensitive skin. Again, treating brass with a varnish can prevent this. Finally, brass is more expensive than other metals due to its high copper content (copper is notoriously expensive). If you have any needs, contact us via email at Lynnyao@prototekparts.com or phone: +86-0792-86372550 Tags: Social Network: Recently Posts Online Help! +(86) 0791-86372550 WANT TO DISCUSS IN DETAIL Contact Our Consultant Now CONTACT NOW
What are the Types and Uses of Valve Stems
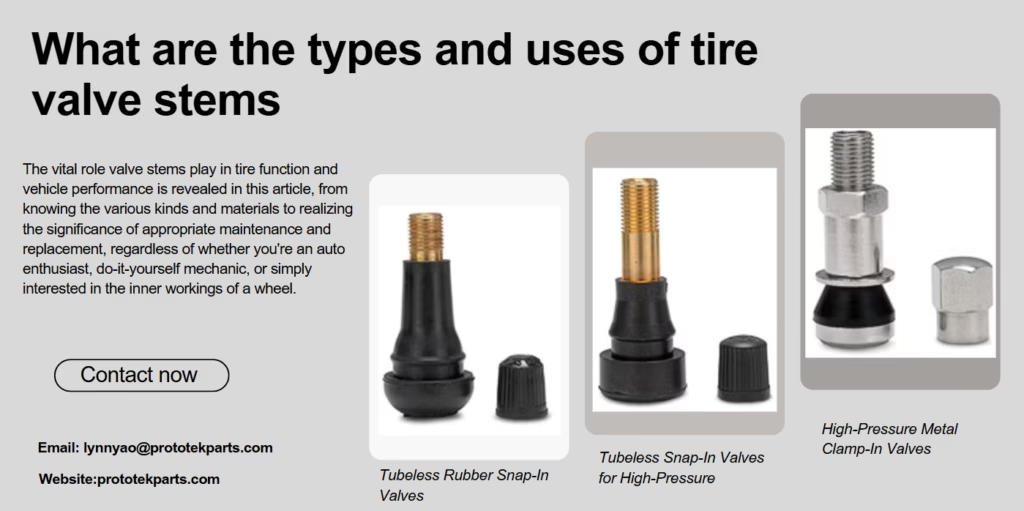
What are the Types and Uses of Valve Stems This article reveals valve stems’ vital role in tire function and vehicle performance. From knowing the various kinds and materials to realizing the significance of appropriate maintenance and replacement. This article is relevant to auto enthusiasts, do-it-yourself mechanics, and anyone simply interested in the inner workings of a wheel. Types of Valve Stems While there are three basic types of tire valves: rubber snap-in, high-pressure snap-in, and high-pressure metal clip-in. The vehicle, desired tire inflation pressure, driving conditions, and wheel design determine which type of valve is appropriate for the application. To complement the wheel styling, the valve can be mounted anywhere on the wheel, from horizontal to vertical. A nearly horizontal valve arrangement is the most common, and many wheel manufacturers use this arrangement to mount the valve-mounted tire pressure monitoring system transmitter. While tire valves can operate at any angle, valves mounted on a vertical axis are more susceptible to pressure loss at high speeds due to centripetal force depressing the valve core and allowing air to escape. Tubeless Rubber Snap-In Valves Tubeless rubber snap-in valves allow for a maximum cold tire inflation pressure of 65 psi and are designed for passenger cars, light trailers, and light trucks, as well as for off-road racing. Rubber snap-in valves fit into either a 0.453-inch or 0.625-inch diameter hole in the rim and are available in effective lengths ranging from 7/8-inch to 2-1/2-inches. While most rubber snap-in valves use a plastic cap, some come with a chrome sleeve and metal cap to help complement the look of custom or alloy wheels. Tubeless Snap-In Valves for High-Pressure High-pressure application tubeless click-in valves are designed for medium- and heavy-duty trucks and trailers and must be used when the recommended cold tire inflation pressure exceeds 65 psi. High-pressure click-in valves for .453″ rim holes allow for a maximum cold tire inflation pressure of 80 psi, while high-pressure click-in valves for .625″ rim holes allow for a maximum cold tire inflation pressure of 100 psi. High-pressure click-in valves are typically used for steel wheels and consist of a thick rubber click-in base, a metal barrel, and a plastic cap. Effective lengths range from approximately 1-1/4″ to 2″. High-Pressure Metal Clamp-In Valves High-pressure metal pinch-in valves can be used with virtually any wheel and are highly recommended for all track activities and situations where vehicle speeds may exceed 130 mph. Metal pinch-in valves use a rubber gasket to seal the wheel when the retaining nut is tightened. While the design and styling of metal pinch-in valves may result in the retaining nut being hidden inside the wheel or visible on the outside, those valves that place the retaining nut on the outside have the practical advantage of being able to check and adjust the tightness of the retaining nut without removing the tire from the wheel. Metal pinch-in valves allow for a maximum operating pressure of 200 psi and are available for .453-inch or .625-inch rim holes, as well as for specialty applications such as 6 mm (.236-inch) or 8 mm (.315-inch) holes. Metal press-in valves use a metal cap and are available in effective lengths ranging from flush to 2 inches, with straight or curved configurations available to accommodate wheels with unique shapes. Low-profile and lightweight alloy press-in valves are also available for racing applications. Importance of Valve Stems Valve stems play a crucial role in the overall functioning and safety of a vehicle. Proper tire pressure ensures better fuel efficiency, improved handling, and reduced tire wear. When valve stems function correctly, they help prevent air from escaping, keeping the tires inflated and safe for driving. Because under-inflated tires can lead to decreased traction and increased stopping distances, posing a significant risk to drivers and passengers alike. Moreover, valve stems contribute to the overall safety of a vehicle. A faulty or damaged valve stem can lead to sudden tire deflation, which can be hazardous while driving, especially at high speeds. Regular inspections of valve stems can help identify potential issues before they escalate into dangerous situations. In addition to safety, valve stems also have a financial impact on vehicle owners. Maintaining proper tire pressure through effective valve stems can extend the life of tires, saving money on replacements and enhancing fuel economy. By investing in quality valve stems and ensuring they are well-maintained, vehicle owners can enjoy long-term savings while ensuring their vehicles operate at peak performance. Materials and Construction of Valve Stems The longevity and functionality of valve stems are greatly impacted by the materials used in their fabrication. The most used material is rubber, which is preferred for its flexibility and capacity to form an airtight seal. A protective layer is usually applied to rubber valve stems to increase their resilience to ozone and UV radiation, which over time can degrade them. Rubber valve stem longevity is greatly increased by this protective covering, particularly in areas with harsh weather. Superior strength and corrosion resistance are provided by metal valve stems, which are frequently composed of materials like brass or stainless steel. In settings where exposure to chemicals and dampness is a problem, these materials are perfect. Metal valve stems are appropriate for heavy-duty and high-performance automobiles because of their design, which also improves heat dissipation. They are a dependable option for demanding applications because of their sturdy structure, which guarantees that they will retain their integrity even under extreme strain. In addition to the fundamental components, the way valve stems are made might affect how effective they are. Reputable valve stems are put through a rigorous testing process to make sure they work and fulfill industry safety standards. Valve stems that can endure the demands of regular use are made using advanced manufacturing techniques like precision machining and quality control procedures. When choosing improvements or replacements for their automobiles, customers can make better judgments if they are aware of the components and construction methods used in valve stems. Common Valve Stem Problems Like any
What is the function of the camshaft
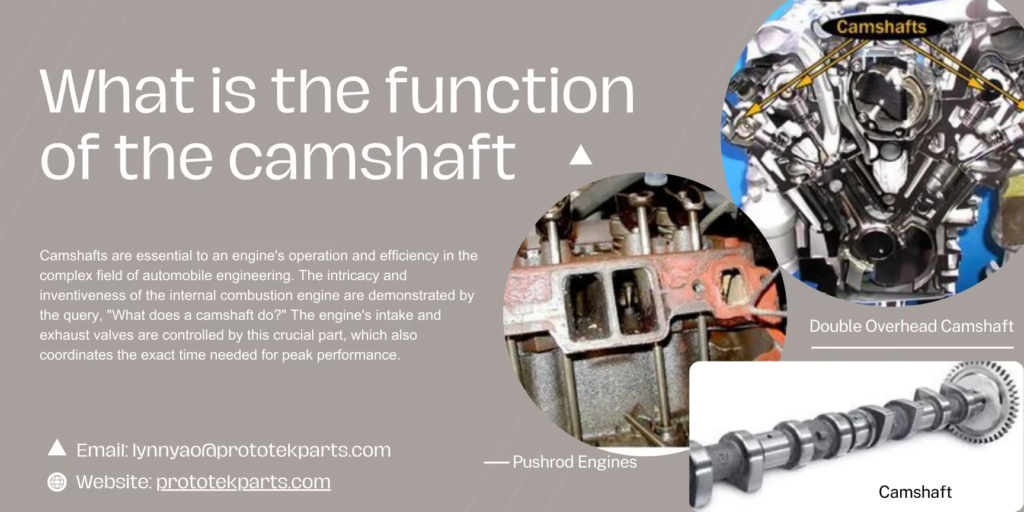
What is the function of the camshaft The functions of the camshaft Camshafts are essential to an engine’s operation and efficiency in the complex field of automobile engineering. The intricacy and inventiveness of the internal combustion engine are demonstrated by the question, “What does a camshaft do?” This crucial part controls the engine’s intake and exhaust valves and coordinates the exact time needed for peak performance. Camshafts make sure that fuel intake and exhaust gas discharge are precisely timed by transforming rotary action into linear motion. One can learn more about the amazing engineering that drives automobiles all around the world by comprehending how a camshaft works. The camshaft, an essential but frequently overlooked part, is at the core of every internal combustion engine. It’s critical to understand how this engineering marvel directly affects your engine’s efficiency and performance. A camshaft’s main job is to control the engine’s intake and exhaust valves opening and closing. It accomplishes this by synchronizing their rotation and timing. Each camshaft lobe—a meticulously designed protrusion—interacts with the valve lifter or pushrod during rotation to accurately regulate the length of time the valve stays open. The engine’s power production and fuel economy are directly impacted by this coordinated action, which makes sure that fuel enters the combustion chamber and exhaust gasses escape at the ideal times. It is impossible to undervalue the camshaft’s function in an internal combustion engine. The camshaft is essential to the engine’s breathing mechanism because it regulates when the valves are open. Whether a car can roar with power or glide down the road with ease depends on how well this mechanism works. The intricacy of contemporary vehicle engineering is demonstrated by the inventiveness of each camshaft lobe’s design and the accuracy of the camshaft’s rotation. These parts are essential to the engine’s ability to capture fuel energy, although they are invisible. They work tirelessly. It’s critical to comprehend how camshafts operate now that you know their purpose. Let’s begin with the fundamentals. Camshaft Basics The key component of a camshaft is the lobe. As the camshaft rotates, the lobe opens and closes the intake and exhaust valves as the piston moves. It turns out that the shape of the cam lobe has a direct relationship to how the engine performs over a range of speeds. To understand why this is the case, imagine that we are running the engine at an extremely slow speed—just 10 or 20 revolutions per minute (RPM)—so that it takes the piston several seconds to complete a cycle. It’s impossible to run a normal engine that slowly, but let’s imagine that we can. At this slow speed, we want the cam lobe to be shaped like this: When the piston begins to move downward during the intake stroke (called the top dead center, or TDC), the intake valve will open. When the piston hits the bottom, the intake valve will close. The exhaust valve will open when the piston hits the bottom at the end of the combustion stroke (called the bottom dead center, or BDC) and close when the piston completes the exhaust stroke. This setup works well as long as the engine is running at this slow speed. But what happens if you increase the RPM? Let’s find out. The 10 to 20 RPM configuration of the camshaft does not work well when increasing RPM. If the engine is running at 4,000 RPM, the valves are opening and closing 2,000 times per minute, or 33 times per second. At these speeds, the piston is moving very fast, so the air/fuel mixture rushing into the cylinder is also moving very fast. When the intake valve opens and the piston begins its intake stroke, the air/fuel mixture in the intake tract begins to accelerate into the cylinder. When the piston reaches the bottom of its intake stroke, the air/fuel is moving at a fairly high speed. If we slam the intake valve shut, all of the air/fuel will come to a stop and will not enter the cylinder. By leaving the intake valve open for a while, the momentum of the fast-moving air/fuel continues to press the air/fuel into the cylinder when the piston begins its compression stroke. Therefore, the faster the engine is running, the faster the air/fuel is moving, and the longer we want the intake valve to stay open. We also want the valves to open wider at higher speeds – a parameter called valve lift, which is controlled by the cam lobe profile. If you have any needs, contact us via email at Lynnyao@prototekparts.com or phone: +86-0792-86372550 Tags: Social Network: Recently Posts Online Help! +(86) 0791-86372550 WANT TO DISCUSS IN DETAIL Contact Our Consultant Now CONTACT NOW
Precision CNC Machining for Valve Bodies
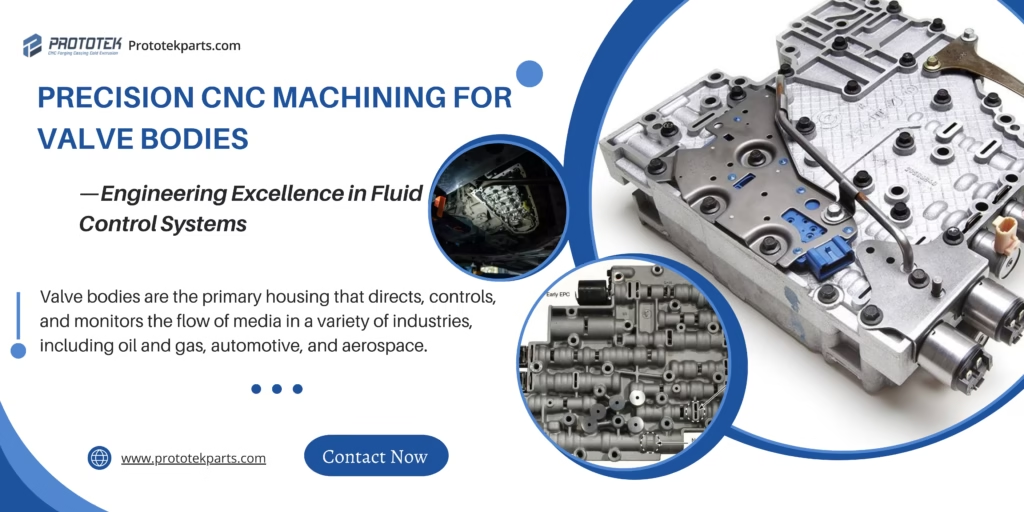
Precision CNC Machining for Valve Bodies Valve bodies are the primary housing that directs, controls, and monitors the flow of media in a variety of industries, including oil and gas, automotive, and aerospace. They are also an important part of fluid and gas control systems. Manufacturing accuracy is critical because the performance of the valve is determined by the accuracy, robustness, and reliability of the valve body. Computer numerical control (CNC) machining is the industry standard for manufacturing quality valve bodies, combining cutting-edge technology with careful engineering design. This article will take a deep look at the role of CNC machining in valve body manufacturing, important design factors, and how Prototek’s experience ensures the quality of valve body production. The Importance of Valve Bodies in Fluid Systems A valve body acts as the structural core of a valve, housing internal components such as the stem, seat, and disc. Its design dictates the valve’s functionality—whether it’s a ball valve, gate valve, or check valve. Key requirements for valve bodies include: Leak-proof performance: To prevent media leakage under high pressure. Corrosion resistance: To withstand aggressive fluids, gases, or environmental conditions. Dimensional accuracy: To ensure proper alignment of internal components and smooth operation. Structural integrity: To endure mechanical stress, temperature fluctuations, and cyclic loading. Given these demands, CNC machining is indispensable for achieving the tight tolerances and complex geometries required for modern valve systems. CNC Machining: The Ideal Solution for Valve Body Production CNC machining offers unmatched precision and repeatability, making it the preferred method for manufacturing valve bodies. Here’s how CNC technology addresses the challenges of valve production: 1. Complex Geometry and Internal Features Valve bodies often feature intricate internal channels, threaded ports, and sealing surfaces. Multi-axis CNC machines (e.g., 5-axis mills) can produce these geometries in a single setup, reducing errors and ensuring consistency. 2. Material Versatility Valve bodies are manufactured from materials such as: Stainless steel (e.g., 316L, 17-4PH): For corrosion resistance in chemical and marine applications. Carbon steel: For high-strength, high-pressure environments. Brass and bronze: For low-pressure plumbing and HVAC systems. Exotic alloys (e.g., Inconel, Hastelloy): For extreme temperatures and corrosive media. CNC machines handle these materials efficiently, adapting tool paths and cutting parameters to optimize surface finish and tool life. 3. Tight Tolerances Valve bodies require tolerances as tight as ±0.001 inches (±0.025 mm) to ensure proper sealing and component alignment. CNC machining achieves this precision consistently, even for high-volume production runs. 4. Surface Finish Requirements Smooth internal surfaces are critical to prevent turbulence, erosion, or contamination. CNC processes like grinding, honing, and polishing can achieve surface finishes as low as 0.2 µm Ra. Key Challenges in Valve Body Machining Despite CNC machining’s advantages, producing valve bodies involves several challenges: Internal Cavity Accessibility: Deep bores and narrow channels require specialized tooling, such as extended-reach end mills or boring bars. Thread Integrity: Precision threading for ports and fittings demands advanced tapping techniques and thread milling. Heat Management: Machining hard materials like stainless steel generates heat, necessitating coolant strategies to prevent warping. Quality Control: Post-machining inspections, including checks of coordinate measuring machines (CMM) and pressure testing, are essential to validate performance. Prototek: Elevating Valve Body Manufacturing Through Expertise At Prototek, we specialize in delivering precision-machined valve bodies that meet the stringent demands of industries worldwide. Our commitment to excellence is reflected in every stage of production: a. Advanced CNC Capabilities Our state-of-the-art CNC facilities include 5-axis machining centers and Swiss-style lathes, enabling us to produce complex valve bodies with unparalleled accuracy. Whether prototyping or scaling to high volumes, we ensure consistent quality across all orders. b. Material Mastery With decades of experience, our team selects and machines materials optimized for your application. From corrosion-resistant stainless steels to high-temperature superalloys, we tailor solutions to enhance valve performance and longevity. c. Precision Finishing Prototek’s secondary services, including passivation, plating, and laser marking, ensure valve bodies meet aesthetic and functional requirements. Our surface treatments enhance corrosion resistance and wear properties, extending component life. d. Rigorous Quality Assurance Every valve body undergoes rigorous inspection using advanced metrology tools, including CMMs and optical comparators. We adhere to ISO 9001 standards and customer-specific certifications, guaranteeing compliance with industry regulations. e. Collaborative Engineering Support Our engineering team partners with clients to optimize designs for manufacturability (DFM). By refining tolerances, material choices, and machining strategies, we reduce costs and lead times without compromising performance. Applications of CNC-Machined Valve Bodies Prototek’s valve bodies are trusted in critical applications such as: Automotive: Fuel systems, turbochargers, and transmission controls. Aerospace: Hydraulic systems and cryogenic fluid management. Oil & Gas: Wellhead controls, pipeline valves, and refinery equipment. Medical: Gas delivery systems and sterilization devices. Conclusion: Trust Prototek for Precision Valve Body Solutions In an era where fluid control systems demand ever-greater precision and reliability, the choice of manufacturing partner is crucial. Prototek stands at the forefront of CNC machining innovation, combining cutting-edge technology, material expertise, and uncompromising quality control to produce valve bodies that excel in the most demanding environments. By partnering with Prototek, you gain access to: Rapid prototyping to accelerate product development. Scalable production with seamless transitions from prototype to volume runs. Industry-specific expertise to meet regulatory and performance standards. For valve bodies that embody precision, durability, and engineering excellence, trust Prototek to deliver solutions that keep your systems flowing flawlessly. If you have any needs, contact us via email at Lynnyao@prototekparts.com or phone: +86-0792-86372550 Tags: Social Network: Recently Posts Online Help! +(86) 0791-86372550 WANT TO DISCUSS IN DETAIL Contact Our Consultant Now CONTACT NOW
Core Applications of CNC Machining in The Automotive Industry
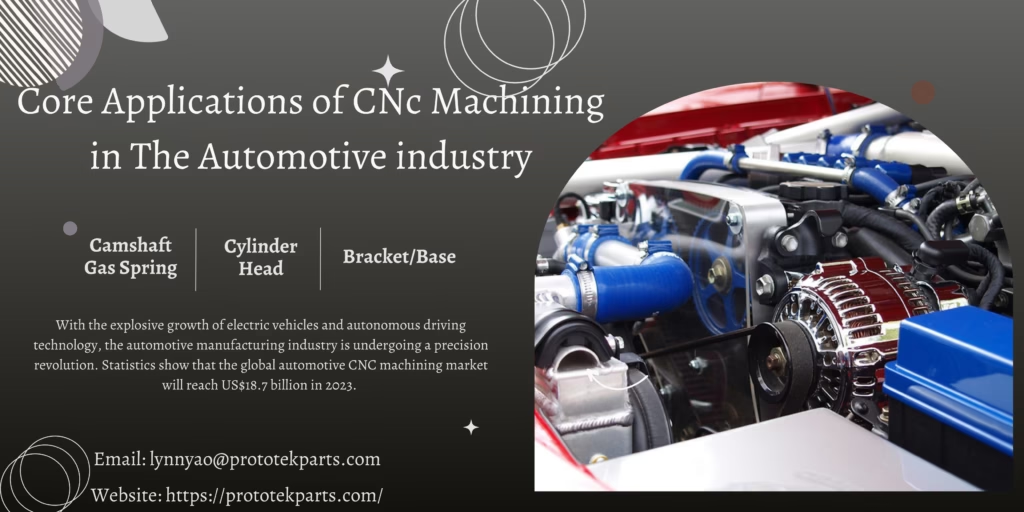
Core Applications of CNC Machining in The Automotive Industry Advantages of CNC Machining for the Automotive Industry High precision and consistency CNC machining controls the movement of mechanical equipment through computer numerical control programs, which can achieve extremely high precision and repeatability. For automotive parts, precision is critical, especially in key systems such as engines, transmissions, chassis, etc. Precision parts such as engine cylinders, brake systems, transmission gears, etc. High production efficiency CNC machining has a high degree of automation and can work 24 hours a day (under proper maintenance and management). It is much more efficient than traditional manual processing methods. Through mass production, CNC machining can significantly reduce the production cycle, and in multi-variety small batch production, the setting and adjustment time of CNC equipment is relatively short, which improves production flexibility. Mass production of automotive parts, such as car wheels, suspension systems, etc. Processing capabilities of complex parts CNC machining can efficiently process parts with complex shapes and geometries, which is essential for the manufacture of many complex parts in modern automotive designs. Traditional processing methods may not be able to handle complex curves or small holes, but CNC technology can easily meet these challenges. Engine parts (such as cylinder blocks, and pistons) and body structural parts. Reduce manual errors Since CNC machining is controlled by computers, errors and deviations in manual operations are reduced. This is especially important for the automotive industry, as any minor error may result in unqualified products and affect the performance and safety of the car. various precision parts, especially those that require high safety and reliability (such as brake systems, airbag components, etc.). Flexibility and customized production CNC machining is not only suitable for large-scale production but also flexible for small-batch customized production. For the automotive industry, when producing parts of various models and styles, the flexibility of CNC machining can be quickly adjusted according to different product requirements, avoiding stagnation of production lines and waste of resources. customized production of chassis components, engine accessories, and interior accessories for different models. High material utilization CNC machining can maximize material utilization by precisely controlling the cutting process. Compared with traditional machining methods, CNC machining can usually reduce waste and reduce material costs more effectively. Processing parts of high-strength steel or aluminum alloy materials reduces the waste of raw materials. Complex surface treatment capabilities CNC machining can not only realize the manufacturing of complex shapes but also can be combined with surface treatment processes (such as spraying, anodizing, coating, etc.) to complete high-demand surface quality treatment. Surface treatment of body appearance parts, engine housings, wheels, and other parts. Rapid prototyping and sample manufacturing CNC machining can quickly produce prototypes and samples, helping design engineers to quickly verify design concepts in the early stages of automotive product development. Through feedback on samples, designs can be adjusted in time to avoid errors in the later production process, thereby accelerating the product development process. Rapid manufacturing of engine prototypes, body design samples, internal structural parts, etc. Improve product quality and consistency CNC machining ensures the consistency of the processing process and reduces deviations caused by human operations, especially in mass production. Automakers mass-produce parts with high precision requirements such as engines, transmissions, and brake systems. Reduce tool wear and increase tool life CNC machining can extend tool life by optimizing cutting parameters, thereby reducing the frequency and cost of tool replacement. The processing of precision aluminum alloy parts produced in large quantities can extend tool life and reduce the frequency of replacement. How is CNC machining used for prototyping in the automotive industry? CNC machining plays a vital role in automotive prototyping, which can quickly and accurately produce functional prototypes and help engineers verify design concepts. Through CNC machining, automakers can produce high-precision prototypes in a short time for testing, evaluation and modification, reducing development costs and shortening R&D cycles. Here are the specific ways how CNC machining is used for automotive prototyping: Rapid prototyping CNC machining can create prototypes based on CAD data (computer-aided design) in a shorter time. By importing design files directly into CNC equipment, the machine can accurately perform operations such as cutting, drilling, milling, etc. to produce precise prototype parts. Compared with traditional manual methods, CNC machining is faster and can complete the processing of multiple complex parts in one operation. Application scenarios: For example, design prototypes of automotive exterior and interior parts, such as dashboards, door linings, engine components, etc. Design verification and testing CNC machining can produce prototypes that are almost identical to the final product, which allows automakers to perform functional verification and performance testing before production. The prototype can be tested for structural strength, assembly, aerodynamics, etc. to ensure the feasibility of the design. Through actual testing, engineers can find design defects earlier and avoid expensive modifications later. Application scenarios: body aerodynamic performance test, collision test, component assembly verification, etc. Integrated testing and assembly The high precision and high consistency of CNC machining ensure that the various components can be assembled together smoothly, so that the prototype can pass more complex assembly and functional tests. CNC machining can be used to make multiple components and can be integrated and assembled at the prototype stage to verify the overall working performance of the automotive system. Application scenarios: Integrated assembly and testing of engines, wheels, suspension systems, etc. during the development process. Which auto parts can be mass-produced using CNC machining technology? Automotive machining can manufacture several other automotive parts, including but not limited to suspension components, exhaust components, carburetor housings, fluid system components, bushings, and valve retainers. This manufacturing technology is also particularly useful for customizing vehicles and their specific automotive parts, as CAD allows for rapid changes in part design and the manufacture of custom parts. Transmission Components: CNC machining is fundamental to prototyping transmission components such as gears and clutches. Precision is critical to ensure that the parts can withstand the stress of operation without failure. CNC technology allows for rapid prototyping and testing of
The Difference Between Galvanized And Stainless Steel
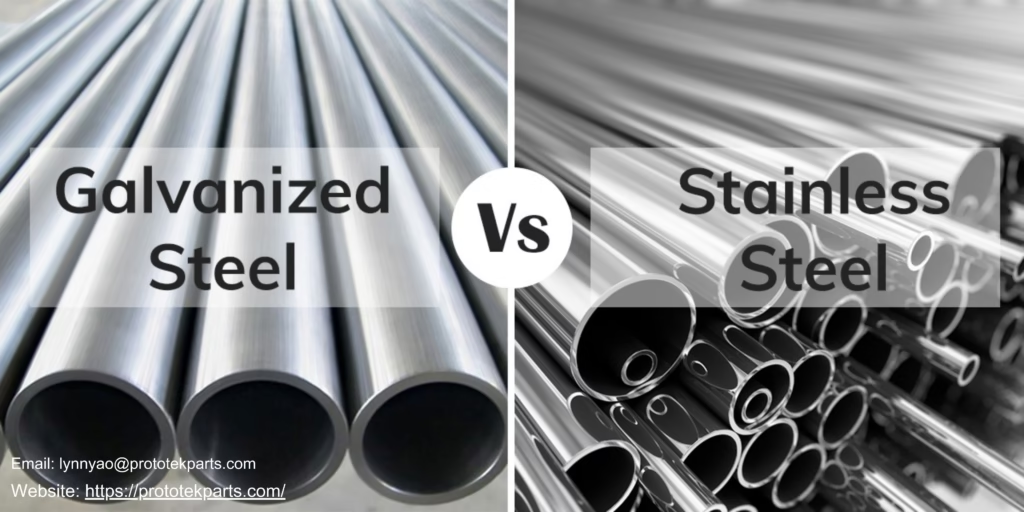
The Difference Between Galvanized And Stainless Steel Material selection in CNC machining is an integral component of its success and must be considered carefully to produce results with optimal performance, durability and cost-efficiency. Galvanized steel and stainless steel are among the many available metals; two commonly utilized choices are galvanized steel and stainless steel; both offer distinct properties suitable for various applications – but understanding their differences is crucial for making informed decisions. In this article, we explore their characteristics, advantages and limitations to help you choose an appropriate material for your CNC machining needs. Introduction to Galvanized Steel and Stainless Steel Galvanized steel is essentially carbon steel that has been coated with a layer of zinc to protect it from corrosion. The galvanization process involves immersing the steel in a bath of molten zinc, which forms a protective layer on the surface. This layer acts as a barrier, preventing moisture and oxygen from reaching the underlying steel, thereby extending its lifespan. Stainless steel, on the other hand, is an alloy of iron, carbon, and a minimum of 10.5% chromium. The chromium content is what gives stainless steel its corrosion-resistant properties. When exposed to oxygen, chromium forms a thin, invisible layer of chromium oxide on the surface, which prevents further oxidation and corrosion. Stainless steel is available in various grades, each with specific properties tailored to different applications. How is galvanized steel made? Hot-dip galvanizing steel typically involves submersion of it in a molten bath of zinc. This method produces a thick, uniform coating that adheres firmly to the steel surface. Before submersion begins, however, steel must first be cleaned of any contaminants such as grease, dirt and rust as any residual substances may hinder adhesion of zinc coating. Once steel has been prepared for galvanizing, it must first be heated in a furnace to remove moisture and reach an ideal temperature for galvanization. Next, it is immersed in a bath of molten zinc solution to coat its surface completely – creating intermetallic layers between zinc and steel which help strengthen bonds between both materials. Once removed from this bath of liquid zinc solution, steel must cool in its environment before solidifying its new durable coat. Electro-galvanizing is another method for galvanizing steel surfaces, using electricity to deposit zinc onto its surface. While this produces a thinner coat than hot-dip galvanizing, electro-galvanization may be ideal for applications requiring smoother finishes and requires less preparation time overall. No matter which approach is taken when galvanizing steel, its results remain unchanged: galvanized steel shows increased corrosion resistance and longevity when compared with untreated steel making it an appealing material in many industries. Types of stainless steel Stainless steel can be divided into several distinct types based on its microstructure and composition of alloying elements, with primary categories including austenitic, ferritic, martensitic, duplex and precipitation-hardening stainless steels as the most widely used types. Each has specific properties tailored specifically for various applications providing an extensive variety of performance characteristics for various tasks. Austenitic stainless steel is one of the most frequently utilized types, known for its superior corrosion resistance and formability. Containing high levels of chromium and nickel which enhance its weldability and ductility. Due to this property it’s often used in kitchen equipment, chemical processing facilities, architectural projects as well as to prevent staining.Ferritic stainless steel contains lower amounts of nickel and has magnetic properties, making it less ductile than austenitic but offering excellent resistance to stress corrosion cracking. Ferritic stainless steel can be found in automotive applications, kitchen sinks and other environments where magnetic properties may prove advantageous. Martensitic stainless steel is known for its superior strength and hardness, making it suitable for applications requiring wear resistance such as cutting tools and surgical instruments. Duplex stainless steel combines properties from both austenitic and ferritic types for increased strength as well as corrosion resistance – perfect for oil and gas applications. Advantages of galvanized steel & stainless steel 1. Corrosion Resistance Galvanized steel offers excellent corrosion resistance due to the zinc coating. However, the level of protection depends on the thickness of the zinc layer and the environment in which the steel is used. In mild environments, galvanized steel can last for decades without significant corrosion. However, in more aggressive environments, such as coastal areas with high salt content, the zinc layer may degrade faster, leading to corrosion of the underlying steel. Stainless steel is inherently more corrosion-resistant than galvanized steel, especially in harsh environments. The chromium oxide layer provides a self-healing mechanism; if the surface is scratched or damaged, the chromium reacts with oxygen to reform the protective layer. This makes stainless steel ideal for applications where exposure to moisture, chemicals, or salt is a concern. 2. Strength and Durability Galvanized steel is known for its strength and durability. The zinc coating not only protects against corrosion but also adds to the overall toughness of the material. However, the mechanical properties of galvanized steel are largely dependent on the base carbon steel. While it is strong, it may not be as durable as stainless steel in certain applications, especially those involving high stress or impact. Stainless steel is generally stronger and more durable than galvanized steel. The addition of alloying elements such as nickel, molybdenum, and titanium enhances its mechanical properties, making it suitable for high-stress applications. Stainless steel also has excellent fatigue resistance, which is crucial for components subjected to cyclic loading. 3. Machinability Galvanized steel is relatively easy to machine, especially when compared to some stainless steel grades. The zinc coating does not significantly affect the machinability of the base steel, allowing for smooth cutting, drilling, and shaping. However, the presence of the zinc layer can lead to increased tool wear, particularly if the coating is thick or uneven. Stainless steel can be more challenging to machine due to its hardness and work-hardening properties. Certain grades, such as austenitic stainless steels (e.g., 304 and 316), are particularly prone to work hardening, which can lead to increased tool wear