Продукты для автоматических винтовых машин
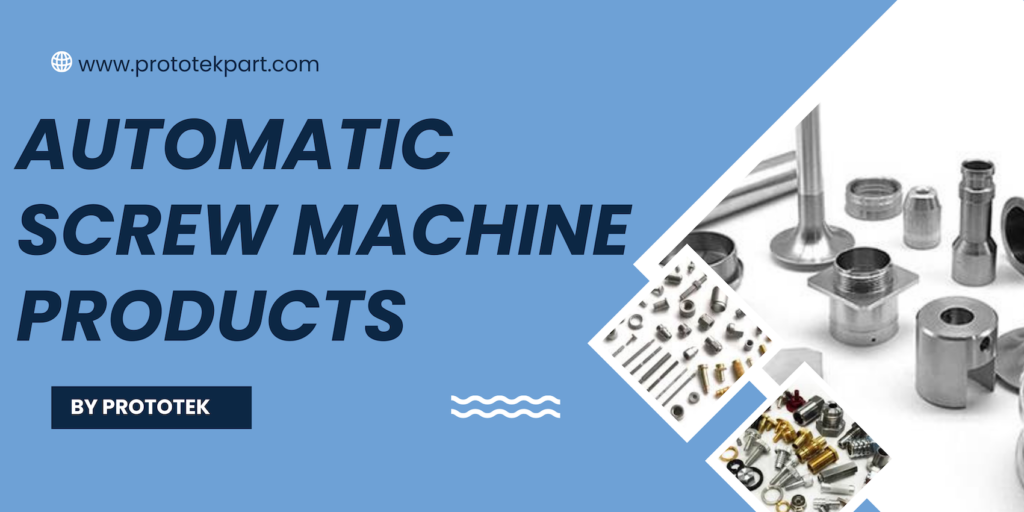
Automatic Screw Machine Products In recent years, driven by advancements in industrial automation, the market for automatic screw machine products has shown significant growth globally. Automatic screw machines, essential equipment in industrial production, are increasingly favored and adopted by manufacturing enterprises for their efficient and precise screw fastening capabilities. Expanding Market Applications Traditional and Emerging Sectors Automatic screw machine products are widely used not only in traditional sectors such as automotive manufacturing and electronics production but also exhibit strong market potential in emerging industries like smart home technology and robotics. Industry experts point out that continuous improvements in the intelligence and automation of automatic screw machines not only enhance production efficiency but also significantly reduce labor costs, making them the preferred choice for enterprises pursuing high efficiency and precision manufacturing. Global Market Growth Market data indicates a rapid increase in demand for automatic screw machine products worldwide. Particularly in the Asia-Pacific region and North American markets, sales volumes and applications of automatic screw machines are expanding noticeably. It is anticipated that in the coming years, with further proliferation and application of Industry 4.0 technologies, the automatic screw machine market will continue to experience robust growth. Technological Advancements R&D Efforts As key participants in the global market for automatic screw machine products, many companies are intensifying their research and development efforts to introduce more intelligent and versatile products that can meet evolving market and customer demands. Concurrently, there is a focus on integrating environmental protection and energy-saving technologies into these advanced solutions. Industrial Efficiency and Innovation This trend underscores the pivotal role of automatic screw machine products in driving industrial efficiency and innovation across diverse sectors, positioning them as pivotal assets in the era of industrial transformation and smart manufacturing. Diverse Applications Automotive Manufacturing Automatic screw machines are extensively used in the automotive industry for assembling components such as engines, transmissions, and electronic modules. They ensure consistent and secure fastening of screws in high-volume production lines. Electronics Assembly In the electronics sector, automatic screw machines play a crucial role in assembling circuit boards, consumer electronics, and precision instruments. They contribute to the reliable fastening of small screws and delicate components. Medical Device Production Automatic screw machines are utilized in the manufacturing of medical devices where precision and cleanliness are paramount. They help in assembling components for devices such as surgical instruments, diagnostic equipment, and implants. Aerospace and Defense The aerospace and defense industries rely on automatic screw machines for assembling aircraft components, missile systems, and defense electronics. They ensure the secure fastening of critical components in stringent operational environments. Appliances and Home Products Automatic screw machines are used in the assembly of household appliances, furniture, and other consumer goods. They contribute to efficient production processes and consistent product quality. Telecommunications Equipment In the telecommunications sector, automatic screw machines are employed in the assembly of networking equipment, mobile devices, and communication infrastructure components. They support the reliable assembly of complex electronic assemblies. Robotics and Automation Automatic screw machines are also integrated into the production of robotic systems and automated machinery. They facilitate the assembly of robotic components, ensuring precise and reliable operation. Renewable Energy Systems In the renewable energy sector, automatic screw machines are used for assembling components of solar panels, wind turbines, and energy storage systems. They help in the efficient production of renewable energy technologies. Advantages of Automatic Screw Machines High Production Rates These machines are designed for high-speed operation, allowing for rapid production of parts once set up. Consistency and Accuracy They can produce parts with high precision and consistency, reducing variability compared to manual machining. Reduced Labor Costs Automation decreases the need for manual labor, which can lead to significant savings in labor costs over time. Versatility Modern automatic screw machines can be programmed to produce a variety of parts with different specifications, making them versatile for various manufacturing needs. Reduced Scrap With precise control and automation, these machines can minimize material waste and scrap, improving overall efficiency. Fast Setup Once programmed and set up, automatic screw machines can begin production quickly, reducing downtime between production runs. Quality Control Automated systems often include built-in quality control measures, ensuring that parts meet specified standards consistently. Lower Unit Costs When considering the overall efficiency, reduced labor costs, and minimized scrap, automatic screw machines can help lower the per-unit cost of production. Overall, these advantages make automatic screw machines a preferred choice in industries where high-volume production of small to medium-sized parts is required with high precision and efficiency. If you have any needs, contact us via email at Lynnyao@prototekparts.com or phone: +86-0792-86372550 Tags: Social Network: Recently Posts Online Help! +(86) 0791-86372550 Have Questions? Want To Discuss In Detail? Contact Our Consultant Now CONTACT
Применение станков с ЧПУ в автомобильной промышленности
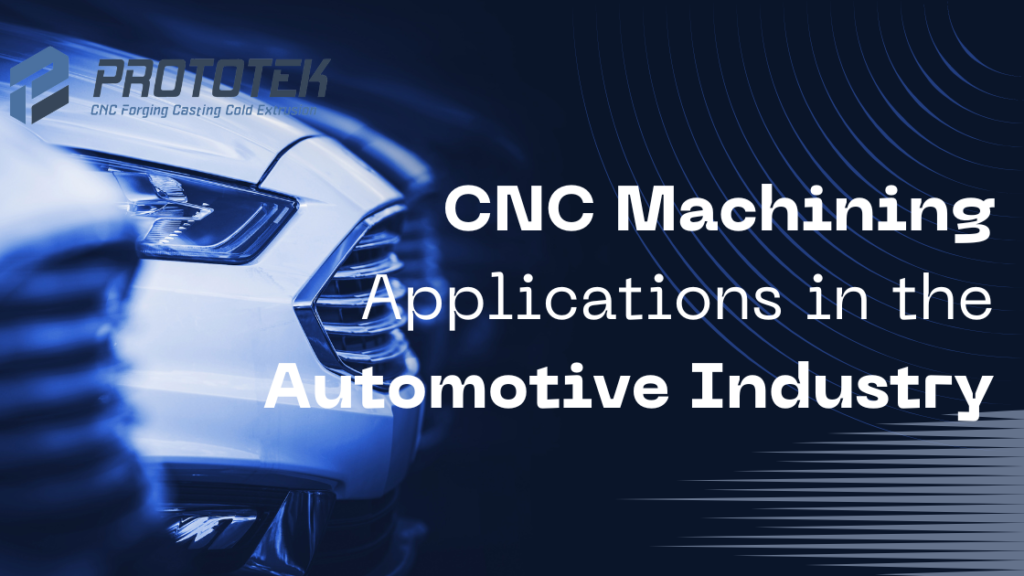
CNC Machining Applications in the Automotive Industry Precision and efficiency are desirable and essential in the fast-paced world of automotive innovation. At Prototek, we are at the forefront of leveraging CNC (Computer Numerical Control) machining to revolutionize automotive manufacturing. Our commitment to excellence ensures that every component we produce meets the highest standards of quality and reliability, pushing the boundaries of what’s possible in vehicle design and performance. Introduction to CNC Machining in Automotive Industry CNC machining has fundamentally transformed the automotive industry by offering unparalleled precision and consistency in part production. Unlike traditional manufacturing methods that rely on manual operations, CNC machines operate under computer control, ensuring each component is machined with exacting accuracy. This capability is crucial in the automotive sector, where parts must fit seamlessly, endure extreme conditions, and contribute to overall vehicle performance. Prototek’s CNC Machining Capabilities At Prototek, we specialize in CNC machining solutions tailored to meet the unique demands of automotive manufacturers. Our state-of-the-art facility houses a diver se range of CNC machines, each equipped with advanced capabilities to handle various materials including metals like aluminum, titanium, and stainless steel, as well as engineering plastics. This versatility allows us to produce everything from engine components and drivetrain parts to intricate interior features with precision and efficiency. Materials Expertise: Enhancing Automotive Performance Materials play a critical role in determining the performance, durability, and even the environmental impact of vehicles. Prototek’s expertise in machining different materials ensures that automotive components meet and exceed industry standards. For high-performance vehicles, lightweight materials like aluminum and titanium are favored for their strength-to-weight ratio, contributing to fuel efficiency and overall vehicle agility. Meanwhile, stainless steel and engineering plastics offer durability and versatility for a wide range of automotive applications. Innovation Driving Automotive Excellence Innovation is at the heart of Prototek’s approach to CNC machining. We collaborate closely with automotive engineers and designers to develop prototypes and production parts that push the possible boundaries. Our team of skilled machinists and engineers leverage their expertise to optimize designs for manufacturability, ensuring that each component is functional and enhances the vehicle’s performance and aesthetics. Precision and Consistency: The CNC Advantage The precision offered by CNC machining is unmatched in the automotive industry. Prototek’s CNC machines operate with micron-level accuracy, ensuring tight tolerances and consistent quality across production runs. This level of precision is critical for components such as engine blocks, transmission parts, and suspension components, where even the smallest deviation can impact performance and reliability. Efficiency Through Automation and Advanced Technologies Automation is another key advantage of CNC machining at Prototek. Our facility is equipped with advanced robotic systems and automated CNC machining centers that operate 24/7. This automation not only reduces labor costs but also enhances efficiency and throughput, allowing us to meet tight deadlines and scale production as needed. Automated processes also minimize human error, ensuring consistent quality and reliability in every component we manufacture. Quality Assurance: Ensuring Excellence Quality assurance is ingrained in every step of Prototek’s CNC machining process. We adhere to stringent quality control measures and inspection protocols to verify the accuracy, functionality, and durability of each part. Our commitment to quality is demonstrated by our ISO 9001 certification, which underscores our dedication to delivering products that meet or exceed customer expectations and industry standards. Environmental Responsibility: Sustainable Manufacturing Practices Beyond precision and performance, Prototek is committed to environmental responsibility. We prioritize sustainable manufacturing practices, including the use of eco-friendly materials and energy-efficient technologies. By reducing waste and minimizing our environmental footprint, we contribute to a greener automotive industry while supporting our customers’ sustainability goals. Future Trends in CNC Machining for Automotive Applications Looking ahead, the future of automotive manufacturing will continue to be shaped by advancements in CNC machining technology. Prototek remains committed to investing in cutting-edge equipment and expanding our capabilities to stay ahead of industry trends. From additive manufacturing techniques to hybrid machining solutions, we are exploring new avenues to further enhance precision, reduce lead times, and drive innovation in automotive component manufacturing. Partner with Prototek for Your CNC Machining Needs Partnering with Prototek means gaining access to industry-leading CNC machining expertise and capabilities. Whether you’re developing a prototype or scaling production for a new vehicle model, our team is dedicated to delivering solutions that elevate automotive excellence. Contact us today to discuss your project requirements and discover how Prototek can help you achieve your goals through precision CNC machining. Conclusion: Driving Forward with Prototek In conclusion, CNC machining has revolutionized automotive manufacturing by offering unmatched precision, efficiency, and versatility. At Prototek, we are proud to be at the forefront of this technological revolution, empowering automotive manufacturers to innovate with confidence. From materials expertise to advanced automation and sustainable practices, Prototek is committed to delivering solutions that meet and exceed customer expectations. Contact us today and let’s drive forward together towards a future of automotive excellence with Prototek. If you have any needs, contact us via email at Lynnyao@prototekparts.com or phone: +86-0792-86372550 Tags: Social Network: Recently Posts Online Help! +(86) 0791-86372550 Have Questions? Want To Discuss In Detail? Contact Our Consultant Now CONTACT
Революция в производстве с помощью деталей, отлитых из алюминия
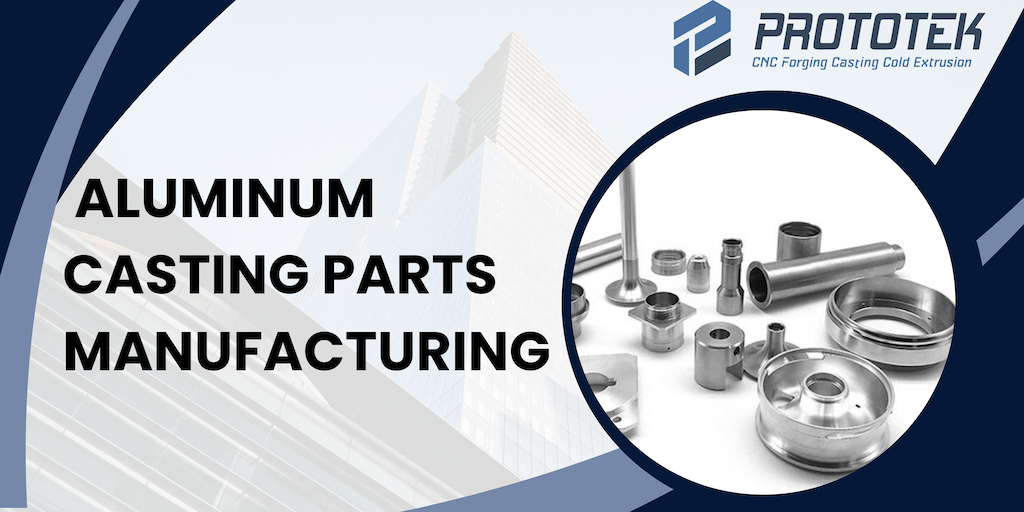
Revolutionizing Manufacturing with Aluminum Casting Parts Aluminum casting parts have emerged as pivotal components in modern manufacturing, offering unparalleled versatility and efficiency across diverse industries. This revolutionary technology leverages aluminum’s inherent properties to deliver lightweight, durable, and intricately designed components crucial in automotive, aerospace, electronics, and various other sectors. Aluminum castings are essential raw materials for equipment production in oil and gas mining, wind power generation, and machinery. They are foundational to the national economy’s basic parts industry, strongly supported by the State. The “14th Five-Year Plan” is a crucial phase for China to achieve industrialization and join the ranks of manufacturing powers. The coordinated development of China’s castings and industries, such as automotive, aerospace, rail transit, equipment manufacturing, and energy, is vital for the domestic manufacturing industry’s growth. Recent policies like the “Guiding Opinions on Promoting the High-Quality Development of the Casting and Forging Industry” and “Guiding Opinions on Accelerating the Green Development of the Manufacturing Industry” encourage enterprises to conduct core technology research, improve casting technology and equipment, and enhance innovation capabilities. These policies promote industrial structure optimization, industry regulation, green and low-carbon transformation, and rapid industry development. Industrial Chain The casting industry relies on upstream raw materials such as steel, copper, and aluminium. Fluctuations in steel prices significantly impact the industry’s overall gross margin. With socio-economic development and industrial manufacturing innovations, the precision casting industry’s downstream application fields have expanded, encompassing instrumentation, shipbuilding, automotive, construction machinery, oil and gas, and aerospace sectors. Market Analysis and Advantages The global market for aluminum casting parts has witnessed significant growth driven by the expanding automotive and aerospace sectors. Lightweighting initiatives aimed at improving fuel efficiency and reducing emissions have propelled the demand for aluminium components. Moreover, aluminium’s recyclability aligns with sustainable manufacturing practices, further boosting its popularity. Domestic and International Applications In the domestic market, aluminium casting parts are extensively used in the automotive industry for engine components, transmission housings, and structural parts due to their high strength-to-weight ratio. Internationally, aerospace applications capitalize on aluminum’s corrosion resistance and thermal conductivity, making it ideal for aircraft structural components and interiors. Casting Industry Development Trends a. Increased Industry Concentration and Scaling Despite a large number of enterprises, China’s foundry industry has seen a reduction in smaller, less efficient companies due to national environmental protection regulations and market stabilization. According to the “14th Five-Year” development plan by the China Foundry Association, there are more than 1,000 enterprises with annual casting production exceeding 10,000 tons and nearly 200 enterprises with over 50,000 tons. The trend towards industrial concentration and scaling is evident. b. Industrial Transformation Towards Intelligence and Digitization The integration of artificial intelligence and digital technologies with manufacturing is a significant trend. Utilizing advanced technologies and modern machinery, such as 3D printing and digital production workshops, helps reduce labour costs, improve product quality, decrease energy consumption, enhance production efficiency, and promote industry upgrades. c. Case Studies and Success Stories Several companies have successfully integrated aluminium casting technologies. In the automotive sector, leading manufacturers have achieved substantial weight reductions without compromising performance or safety. In aerospace, aluminium casting adoption has streamlined production processes and enhanced aircraft efficiency and reliability. d. Future Prospects and Innovations Future advancements in aluminum casting technologies will likely focus on enhancing material properties, optimizing production cycles, and expanding design capabilities. Innovations like rapid prototyping and 3D printing are poised to revolutionize manufacturing, enabling faster development and customization of aluminium casting parts to meet evolving market demands. Aluminium casting parts represent a cornerstone of modern manufacturing, offering unparalleled versatility, durability, and sustainability across various industries. As global industries prioritize lightweight materials and sustainable practices, aluminium casting remains at the forefront, driving innovation and reshaping the future of engineering and manufacturing. Jiangxi Prototek Imp and Exp Co. Ltd Prototek is a leading innovator in aluminium casting technology, dedicated to delivering cutting-edge solutions that redefine manufacturing excellence. With a commitment to quality, sustainability, and customer satisfaction, Prototek continues to pioneer advancements in aluminium casting parts, empowering industries worldwide to achieve new heights of performance and efficiency. If you have any needs, contact us via email at Lynnyao@prototekparts.com or phone: +86-0792-86372550 Tags: Social Network: Recently Posts Online Help! +(86) 0791-86372550 Have Questions? Want To Discuss In Detail? Contact Our Consultant Now CONTACT
Холодная ковка против горячей ковки
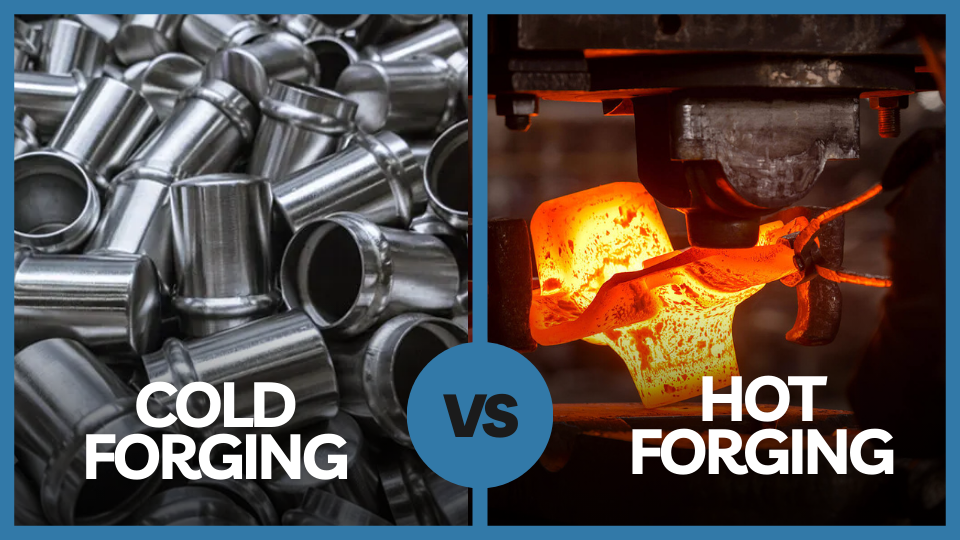
Cold Forging vs Hot Forging In advanced manufacturing, choosing cold and hot forging can significantly impact your components’ quality, strength, and cost-effectiveness. At Prototek, we specialize in delivering superior forging solutions tailored to meet the exacting demands of various industries. This article explores the differences, advantages, and applications of cold and hot forging, showcasing how Prototek’s expertise can elevate your production processes. Understanding Cold Forging Cold forging, or cold working, involves molding metal at or close to room temperature. Through this process, the material holds its unique glass-like structure, which results in expanded hardness and rigidity. The process is not like hot fashioning because the metal isn’t warmed, instead it’s worked in its room-temperature state, below its recrystallization state. Precision in Cold Forging Cold forging involves shaping metal at room temperature or slightly above, using high-pressure dies to form the desired shape. This process is ideal for producing intricate components with excellent dimensional accuracy and surface finish. At Prototek, our cold forging capabilities are backed by state-of-the-art equipment and seasoned craftsmanship, ensuring reliable performance for diverse applications. Advantages of Cold Forging at Prototek: 1. Material Conservation: Cold forging minimizes waste using precise die designs and controlled deformation. This efficiency translates into cost savings and environmental benefits for our clients. 2. Enhanced Mechanical Properties: Due to strain hardening, components forged through cold forging exhibit superior strength, toughness, and surface hardness. Prototek optimizes forging parameters to achieve optimal mechanical properties. 3. Complex Geometries: Cold forging produces complex shapes and features with tight tolerances. Prototek’s engineering expertise and CAD/CAM capabilities ensure seamless design and production integration. 4. Cost-Effective Solutions: Cold forging offers a cost-effective solution for high-volume production runs by reducing machining and material costs. Prototek’s streamlined processes and efficient workflow deliver competitive pricing without compromising quality. 5. Versatility Across Industries: From automotive and aerospace to consumer electronics and medical devices, cold forging serves a wide range of industries where precision and reliability are paramount. Delving into Hot Forging Hot forging, or hot working, includes shaping metal at raised temperatures, usually between 700°C and 1,200°C. The metal is heated to provide flexibility and make it more bendable. Strength and Durability in Hot Forging Hot forging involves heating metal above its recrystallization temperature and then shaping it using dies. This process enhances the material’s plasticity, allowing for easier deformation and superior mechanical properties in the finished parts. Prototek’s hot forging capabilities leverage advanced technology to deliver robust solutions for demanding applications. Advantages of Hot Forging at Prototek: 1. High Strength-to-Weight Ratio: Hot forged parts exhibit exceptional mechanical properties, including high tensile strength, impact resistance, and fatigue strength. Prototek optimizes forging temperatures and dwell times to achieve desired material characteristics. 2. Dimensional Accuracy: Hot forging allows for precise control over grain structure and flow lines, resulting in parts with excellent dimensional stability and uniformity. Prototek’s meticulous process controls ensure consistent quality across production batches. 3. Complex Part Designs: While suitable for simpler geometries, hot forging is particularly practical for parts requiring significant deformation or thick cross-sections. Prototek’s engineering team collaborates closely with clients to optimize designs for hot forging feasibility. 4. Cost-Efficiency in Bulk Production: Hot forging offers economies of scale in large-scale production runs despite higher initial setup costs. Prototek’s strategic tooling and process optimization approach maximizes efficiency and minimizes per-part costs. 5. Wide Application Spectrum: From industrial machinery components to specialized fittings and fasteners, hot forging serves industries demanding robust, high-performance parts subjected to extreme conditions. Making the Right Choice with Prototek Why Choose Prototek for Forging Solutions? 1. Expertise and Innovation: With decades of experience in precision manufacturing, Prototek combines industry-leading expertise with innovative forging technologies to meet evolving market demands. 2. Customized Solutions: Whether you require prototype development, small-batch production, or full-scale manufacturing, Prototek offers tailored forging solutions to optimize performance and reduce time-to-market. 3. Quality Assurance: Prototek adheres to stringent standards throughout the forging process, ensuring every component meets or exceeds customer expectations for durability, reliability, and performance. 4. Collaborative Partnership: We prioritize client collaboration, providing responsive communication, flexible solutions, and proactive project management to ensure seamless project execution and satisfaction. 5. Comprehensive Service Offering: From initial design consultation to final inspection and delivery, Prototek offers end-to-end forging solutions under one roof, streamlining processes and enhancing overall project efficiency. Conclusion In conclusion, choosing between cold and hot forging depends on specific project requirements, including material properties, part complexity, production volume, and cost considerations. At Prototek, we empower you to make informed decisions by offering unparalleled expertise, cutting-edge technology, and a commitment to excellence in every forging solution we deliver. Contact Prototek today to discuss your forging needs and discover how we can optimize your production processes with precision, strength, and reliability—partner with Prototek to forge solutions that elevate your products to new heights of performance and durability. If you have any needs, contact us via email at Lynnyao@prototekparts.com or phone: +86-0792-86372550 Tags: Social Network: Recently Posts Online Help! +(86) 0791-86372550 Have Questions? Want To Discuss In Detail? Contact Our Consultant Now CONTACT
Фрезерная обработка с ЧПУ против токарной обработки с ЧПУ
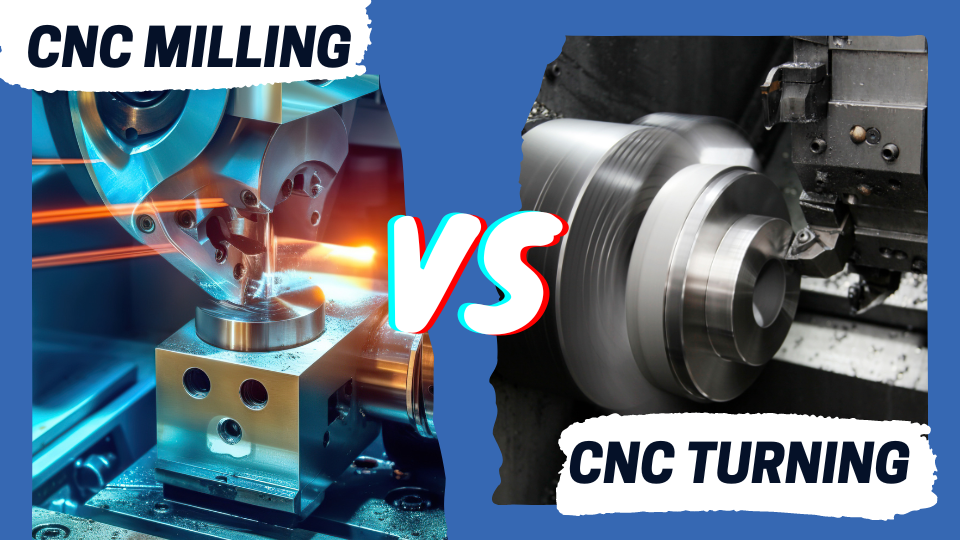
CNC Milling vs CNC Turning In today’s rapidly evolving manufacturing landscape, precision and efficiency are paramount. Choosing the proper machining process is crucial in aerospace, automotive, medical devices, or any other industry requiring intricate components. At Prototek, we deliver high-quality CNC machining solutions tailored to meet diverse client needs. This article explores the differences, advantages, and applications of CNC milling and turning, empowering you to make informed decisions for your projects. Understanding CNC Milling The Art of CNC Milling CNC milling involves using rotary cutting tools to remove material from a workpiece, creating complex shapes and features. This process is ideal for producing components with detailed designs and strict dimensional tolerances. At Prototek, our CNC milling capabilities are at the forefront of precision manufacturing, allowing us to cater to various industries and applications. Advantages of CNC Milling at Prototek 1. Precision and Versatility: CNC milling excels in machining parts that require high precision and intricate geometries. Our state-of-the-art milling machines and CAD/CAM software ensure consistent accuracy, meeting even the most demanding specifications. 2. Material Flexibility: CNC milling accommodates various materials, from aluminum and stainless steel to plastics and composites. This versatility enables Prototek to serve clients across multiple industries, from prototyping to production. 3. Complexity Handling: We leverage advanced technologies to efficiently tackle complex designs involving 3-axis, 4-axis, or 5-axis milling. Prototek’s engineering expertise ensures optimal tool paths and machining strategies for each project. 4. Rapid Prototyping and Short Runs: With efficient programming and setup, Prototek delivers rapid prototyping services and seamlessly handles small to medium production runs. This agility is crucial for accelerating product development cycles and meeting tight deadlines. 5. Quality Assurance: Rigorous quality control measures, including in-process inspections and final checks, guarantee that every component meets the highest standards before leaving our facility. Delving into CNC Turning Mastering CNC Turning Techniques CNC turning revolves around rotating a workpiece while cutting tools remove material to create cylindrical shapes and symmetrical parts. This process is highly efficient for producing axially symmetric components with minimal setup times, making it cost-effective for large-scale production runs. Advantages of CNC Turning at Prototek 1. Efficiency and Speed: CNC turning produces cylindrical parts quickly and efficiently. Prototek’s advanced turning centers and skilled operators ensure consistent performance and rapid turnaround times for our clients. 2. Cost-Effectiveness: CNC turning offers significant cost advantages over other machining methods for high-volume production runs. Prototek optimizes material usage and production processes to deliver competitive pricing without compromising quality. 3. Versatility in Component Size: Whether small precision parts or more significant components up to a specific diameter and length, CNC turning accommodates a wide range of sizes and shapes. This versatility caters to diverse industry needs, from automotive components to medical instruments. 4. Surface Finish and Tolerance Control: Prototek ensures superior surface finishes and tight dimensional tolerances in every turned component with fine-tuned cutting parameters and tooling selection. This attention to detail is critical for meeting functional and aesthetic requirements. 5. Consistency and Reliability: Prototek maintains stringent quality controls throughout the turning process, from initial setup to final inspection. Our commitment to reliability ensures that each part meets customer specifications and exceeds expectations. Choosing the Right Methodology Factors Influencing Your Decision When deciding between CNC milling and CNC turning for your project, several factors come into play: 1. Part Complexity: Complex geometries and features often favor CNC milling because they can maneuver in multiple axes and perform intricate cuts. 2. Material Type: Consider the material’s hardness, machinability, and specific properties. CNC milling is versatile and uses a wide range of materials, while CNC turning is efficient for softer metals and plastics. 3. Production Volume: CNC milling offers flexibility and rapid turnaround for small batches and prototypes. Conversely, CNC turning is optimal for high-volume production due to its efficiency and lower per-part cost. 4. Tolerance Requirements: Evaluate the required dimensional accuracy and surface finish. Both processes can achieve tight tolerances, but the approach may vary based on part geometry and material. 5. Lead Time and Cost: Assess project timelines and budget constraints. Prototek’s streamlined processes ensure competitive pricing and timely delivery, supporting your project’s success. Prototek’s Commitment to Excellence Why Choose Prototek? At Prototek, we are more than a CNC machining service provider – your strategic partner in innovation and manufacturing excellence. Here’s why clients trust us: 1. Advanced Technology: Our cutting-edge CNC equipment and software investment ensures superior precision and efficiency across all projects. 2. Expertise and Experience: With decades of experience in precision machining, our team of engineers and machinists delivers innovative solutions tailored to your needs. 3. Quality Assurance: From initial design consultation to final inspection, Prototek adheres to rigorous quality standards to deliver flawless components that meet or exceed industry requirements. 4. Customer Focus: We prioritize client satisfaction, offering responsive communication, flexible solutions, and proactive project management to ensure your expectations are met and exceeded. 5. End-to-End Solutions: Whether you need rapid prototyping, small-batch production, or full-scale manufacturing, Prototek provides comprehensive CNC machining services under one roof. Conclusion In conclusion, CNC milling and turning are integral to modern manufacturing, each offering unique advantages depending on project requirements. At Prototek, we leverage our expertise, advanced technology, and commitment to quality to deliver exceptional results for our clients. Whether launching a new product, refining an existing design, or scaling production, our CNC machining capabilities empower you to achieve your goals efficiently and cost-effectively. Contact Prototek today to discuss your CNC machining needs and discover how we can elevate your projects from concept to reality—partner with us for precision, reliability, and innovation in manufacturing. If you have any needs, contact us via email at Lynnyao@prototekparts.com or phone: +86-0792-86372550 Tags: Social Network: Recently Posts Online Help! +(86) 0791-86372550 Have Questions? Want To Discuss In Detail? Contact Our Consultant Now CONTACT
Токарные услуги с ЧПУ: Революция в прецизионном производстве
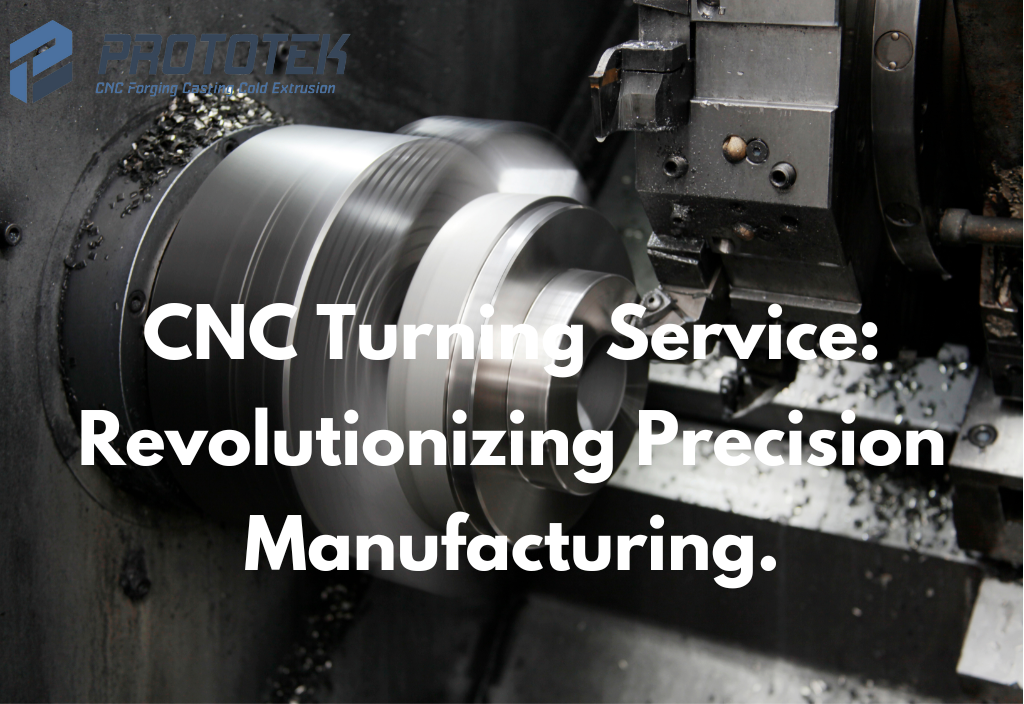
CNC Turning Service: Revolutionizing Precision Manufacturing Computer Numerical Control (CNC) turning service has revolutionized the landscape of precision manufacturing by offering efficient, automated, and high-precision machining capabilities. Jiangxi Prototek Imp & Exp Co., Ltd is at the forefront of leveraging CNC-turning technology to meet the evolving needs of industries worldwide. This paper provides an in-depth exploration of CNC turning service, elucidating its technological advancements, operational principles, applications across industries, and the challenges manufacturers face. Through a comprehensive review of the literature and case studies, this paper highlights the key innovations driving the evolution of CNC turning service, including advancements in machine tool design, cutting-edge software solutions, and integration with Industry 4.0 technologies. Furthermore, it discusses the operational considerations, such as material selection, tooling strategies, and process optimization, essential for achieving optimal performance and quality in CNC turning operations. Moreover, this paper examines the challenges confronting CNC turning service providers like Jiangxi Prototek Imp & Exp Co., Ltd, such as skill shortages, cybersecurity risks, and continuous innovation to meet evolving customer demands. Finally, it outlines future directions and emerging trends in CNC turning service, including adopting artificial intelligence, additive manufacturing techniques, and sustainable machining practices, to address the demands of a rapidly changing manufacturing landscape. Overview of CNC Turning Service Technological Foundations of CNC Turning Service CNC turning service relies on sophisticated machine tools equipped with computer-controlled axes to shape workpieces according to predefined specifications precisely. The integration of servo motors, feedback systems, and advanced control algorithms enables CNC turning machines to execute complex machining operations with unmatched precision and repeatability. Advancements in cutting tool materials, coatings, and geometries have further enhanced the performance and efficiency of CNC turning processes, allowing manufacturers to achieve tighter tolerances, improved surface finishes, and higher productivity levels. Applications Across Industries CNC turning service finds widespread applications across diverse industries, including aerospace, automotive, medical devices, electronics, and energy sectors. Its ability to produce intricate components with high precision and repeatability makes it indispensable for manufacturing critical parts such as shafts, bushings, gears, valves, and connectors. Moreover, CNC turning service enables the production of complex geometries, such as threads, grooves, chamfers, and radii, with exceptional accuracy and surface finish, thereby facilitating the realization of innovative product designs and engineering solutions. Aerospace In the aerospace industry, CNC turning service is extensively used for manufacturing critical components such as turbine blades, engine shafts, landing gear components, and structural fittings. These parts require high precision and reliability to meet stringent safety and performance standards. CNC turning allows aerospace manufacturers to produce complex geometries with tight tolerances, ensuring optimal aerodynamic efficiency and structural integrity of aircraft and spacecraft. Automotive CNC turning service plays a crucial role in the automotive industry for producing engine pistons, transmission shafts, steering system parts, and suspension components. The high precision and repeatability offered by CNC turning ensure the seamless operation and durability of automotive systems. Additionally, CNC turning enables automotive manufacturers to achieve lightweight designs and optimize fuel efficiency without compromising on performance or safety. Medical Devices In the medical device industry, CNC turning service is used to manufacture various implants, surgical instruments, prosthetic components, and medical device enclosures. These components often require biocompatible materials and precise dimensional accuracy to meet medical regulatory standards and ensure patient safety. CNC turning allows medical device manufacturers to produce customized implants and instruments tailored to individual patient needs, facilitating better patient outcomes and improving healthcare delivery. Electronics CNC turning service is integral to producing electronic components such as connectors, housings, heat sinks, and PCB mounting hardware. These components require precise tolerances, smooth surface finishes, and intricate geometries to ensure proper functionality and reliability in electronic devices. CNC turning enables electronics manufacturers to achieve high production volumes, consistent quality, and rapid prototyping, accelerating time-to-market for new products and technologies. Energy In the energy sector, CNC turning service is utilized for manufacturing components for renewable energy systems, power generation equipment, and oil and gas exploration tools. Components such as turbine blades, generator shafts, valve bodies, and drill bits require high precision and durability to withstand harsh operating conditions and ensure uninterrupted energy production. CNC turning enables energy companies to optimize efficiency, reduce downtime, and enhance safety in energy extraction, generation, and distribution processes. Industrial Machinery CNC turning service is widely employed in the production of industrial machinery components such as gears, bearings, shafts, pulleys, and couplings. These components form the backbone of various manufacturing processes and industrial applications, requiring precise dimensions, smooth surfaces, and reliable performance. CNC turning allows machinery manufacturers to meet diverse customer requirements, optimize production workflows, and enhance equipment reliability and longevity. Consumer Goods In the consumer goods industry, CNC turning service is utilized for manufacturing a wide range of products, such as knobs, handles, fittings, and decorative elements. These components often require intricate designs, aesthetic finishes, and functional features to appeal to consumer preferences and enhance product usability. CNC turning enables consumer goods manufacturers to achieve consistent quality, design flexibility, and cost-effective production, meeting market demand and driving customer satisfaction. Operational Considerations Operational considerations, such as material selection, tooling strategies, and process optimization, are essential for achieving optimal performance and quality in CNC turning operations. Challenges in CNC Turning Service Skill Shortages Cybersecurity Risks Need for Continuous Innovation Future Directions and Emerging Trends Adoption of Artificial Intelligence Additive Manufacturing Techniques Sustainable Machining Practices Conclusion CNC turning service represents a cornerstone of precision manufacturing, offering unparalleled efficiency, accuracy, and versatility capabilities. By leveraging advanced technologies, operational best practices, and continuous innovation, CNC turning service providers can overcome challenges, capitalize on emerging opportunities, and drive transformative changes in manufacturing industries worldwide. As the manufacturing landscape continues to evolve, CNC turning service is poised to play a pivotal role in shaping the future of production, enabling the realization of innovative products, sustainable practices, and enhanced customer experiences. If you have any needs, contact us via email at Lynnyao@prototekparts.com or phone: +86-0792-86372550 Tags: Social Network: Recently Posts Online Help! +(86) 0791-86372550 WANT TO DISCUSS IN DETAIL Contact Our Consultant Now