Лучшая сталь для обработки - руководство от Prototek

Blog Details Machining stands as a crucial aspect of the manufacturing industry, and the selection of the right steel is paramount for ensuring the success of the manufacturing process. In this comprehensive guide by Prototek, we delve into the key factors involved in selecting the most suitable steel for machining applications. Basic properties of steel Strength and hardness: one of the most fundamental properties of steel is its strength and hardness. Strength indicates the ability of a material to resist deformation and destruction, while hardness reflects the ability of a material to resist external pressure. In machining, the selection of appropriate strength and hardness of steel is the key to ensuring the durability and performance stability of parts. Toughness and plasticity: toughness refers to the ability of steel to resist cracking under impact or vibration, while plasticity refers to the ability of a material to deform without breaking during processing. For parts that need to withstand impact loads or require complex shapes, steel with good toughness and plasticity is essential. Corrosion Resistance: the corrosion resistance of steel determines its performance in harsh environments. Especially in wet or chemically corrosive environments, corrosion-resistant steel can extend the service life of parts and reduce maintenance costs. Steel classification Carbon Steel: High Carbon Steel: high carbon content, high hardness, suitable for cutting tools and high strength parts. Medium Carbon Steel: medium carbon content, with good strength and plasticity, widely used in machine parts manufacturing. Low carbon steel: relatively low carbon content, easy to process, used for welding and manufacturing parts requiring plasticity. Alloy Steel: Chromium alloy steel: containing chromium to improve hardness and corrosion resistance, suitable for manufacturing cutting tools and bearings. Tungsten Alloy Steel: contains tungsten, which increases cutting performance and wear resistance, and is used in high-speed cutting tools. Nickel alloy steel: nickel-containing, excellent corrosion resistance and high-temperature stability, suitable for chemical and aviation fields. Other categories: Stainless steel: excellent corrosion resistance for applications requiring appearance and durability. Tool Steel: designed to make tools with high hardness and abrasion resistance. Spring Steel: has good elasticity and fatigue strength, for the manufacture of springs and elastic components. Key elements of machining Cutting performance: in the machining process, cutting performance is one of the key factors. This involves the reaction of steel undercutting with a tool, including friction and heat generation between the tool and the workpiece. The selection of steel with good cutting performance can improve machining efficiency, reduce tool wear, and ensure the stability of the machining process. Heat Treatment Adaptability: The heat Treatment Adaptability of steel refers to its performance changes after high-temperature treatment. In machining, some parts need to undergo heat treatment to improve their hardness, strength, and other properties. Therefore, the selection of steel with good adaptability to heat treatment is the key to ensuring the final product quality. Machining stability: the machining stability of steel is related to the stability and controllability of the machining process. Some steels may cause dimensional inconsistency or shape distortion due to deformation or instability during processing. Therefore, it is very important to select steel with good machining stability to ensure the machining of high-precision parts. The most suitable steel for machining Drilling: recommended steel: high-speed steel with good machinability and wear resistance, such as M2 high-speed steel. Milling: recommended steel: alloy steel suitable for milling, such as AISI 4140 alloy steel, with good machinability and strength. Turning: recommended steel: easy to process low carbon steel, such as AISI 1018 low carbon steel, suitable for turning and surface processing. High-speed cutting: recommended steel: Tungsten alloy steel with high hardness and machinability, such as Tungsten Carbide. Welding: recommended steels: easy-to-weld low-carbon structural steels, such as AISI 1020, for welded structural components. Corrosion resistance requirements: recommended steel: stainless steel, such as AISI 316, with good corrosion resistance, suitable for chemical and marine environments. Practical applications and case studies High-strength components in aerospace: Application: manufacturing aircraft engine parts, such as turbine blades. Steel selection: use nickel base alloy steel, such as the Inconel series, to ensure that the parts are at high temperatures, in a high-pressure environment with good strength and corrosion resistance. Engine parts in automobile manufacture: Application: manufacturing the crankshaft of an automobile engine. Steel selection: select high carbon alloy steel, such as AISI 4340, to obtain excellent strength and wear resistance, to ensure that the crankshaft at high load conditions with excellent performance. Tool manufacturing: Application: production of high-speed cutting tools, such as milling cutters. Steel selection: use high-speed steel, such as M2, to ensure that the tool has good cutting performance and wear resistance, suitable for high-speed cutting applications. Corrosion-resistant components in chemical equipment: Application: manufacturing corrosion-resistant linings in chemical reactors. Steel selection: stainless steel, such as AISI 316L, to ensure that parts are in a corrosive chemical environment with good corrosion resistance. Machine tool structural parts: Application: manufacturing machine tool bed. Steel selection: use structural alloy steel, such as AISI 4140, to obtain good strength and cutting performance, to ensure the stability and durability of machine tool structure. Surface treatment of parts: Application: the production of high-surface quality parts, such as motorcycle crankshaft surfaces. Steel selection: choose easy-to-process low-carbon steel, such as AISI 1045, to ensure the stability and accuracy of surface processing. To select suitable steel for machining needs to consider the properties, classification of steel, and the factors of the machining process. Through in-depth understanding and practical application verification, manufacturers can improve production efficiency, reduce costs, and produce high-quality products. Future development will focus on the development of new materials and the application of more intelligent machining technology to promote the progress of manufacturing. If you have any needs, contact us via email: Lynnyao@prototekparts.com or phone: +86-0792-86372550 Tags: Social Network: Recently Posts Online Help! +(86) 0791-86372550 WANT TO DISCUSS IN DETAIL Contact Our Consultant Now CONTACT NOW
Навигация в индустрии оптовой торговли автомобильными запчастями: Подробный обзор с Prototek
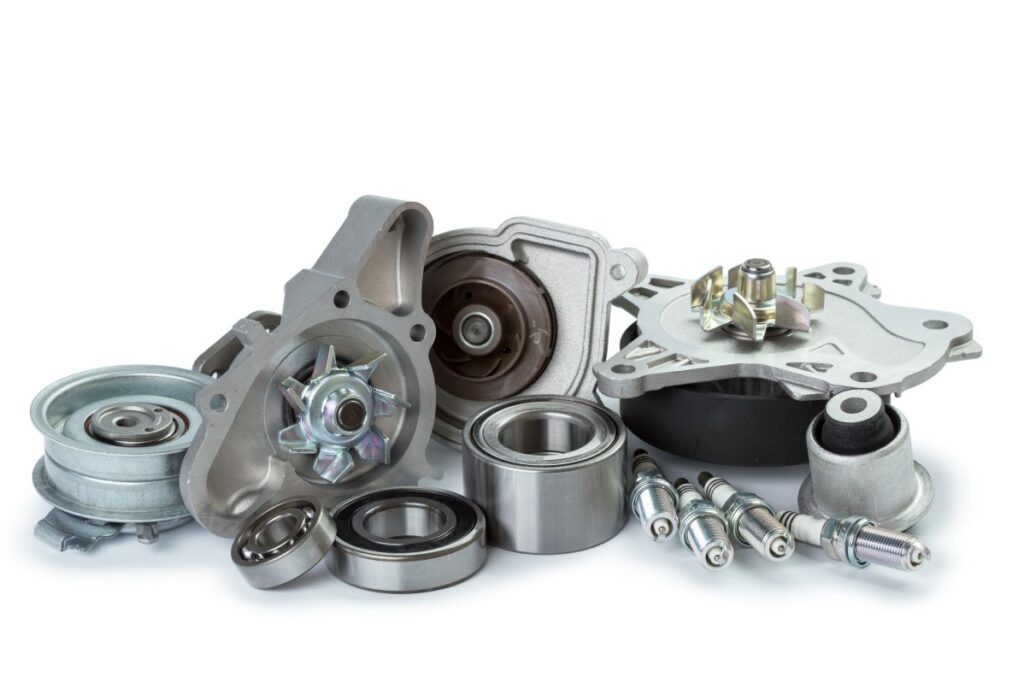
Blog Details The automotive industry stands as a complex ecosystem, encompassing vehicle manufacturing, aftermarket services, and an extensive network of automotive parts. As a cornerstone of global economic growth and technological advancement, this industry holds a pivotal role for companies like Prototek. Wholesale operations, represented by Prototek, play a crucial role within the automotive parts market, acting as the primary link between manufacturers and retailers. They ensure a smooth flow of components and accessories, facilitating timely availability for repair, maintenance, and upgrade purposes. Overview of the Wholesale Automotive Parts Market The wholesale automotive parts market, where Prototek actively participates, is experiencing significant growth. This growth is fueled by the expanding global vehicle fleet and the increasing complexity of vehicle components. Rising demand for aftermarket parts, driven by vehicle aging, maintenance needs, and consumer preferences for customization, further contributes to the flourishing market. Additionally, the industry’s evolution is shaped by regulatory changes emphasizing vehicle safety, emissions standards, and technological advancements like electric and autonomous vehicles. The market encompasses a diverse array of stakeholders, with Prototek leading the way alongside traditional distributors, aftermarket specialists, OEMs, and online platforms. The emergence of e-commerce and online marketplaces has disrupted conventional distribution channels, offering consumers a wider range of options and intensifying competition among wholesalers like Prototek. Innovation, service differentiation, and customer-centric strategies are increasingly vital for Prototek to establish and sustain its market position. Automotive parts cover a vast spectrum, ranging from critical engine components to interior and exterior accessories. Prototek actively responds to market dynamics, adapting to trends such as the growing interest in electric vehicles, leading to increased demand for electric drivetrain components and associated technologies. Similarly, the trend toward connected vehicles has elevated the demand for advanced sensors and communication modules. Wholesale Automotive Parts Distribution Process Prototek’s procurement strategies involve meticulous supplier selection, negotiation of favorable terms, and the establishment of robust partnerships. Ensuring a diversified supplier base and maintaining close relationships with manufacturers and suppliers facilitate timely access to quality parts while mitigating supply chain risks. Efficient inventory management practices are essential for Prototek to optimize stock levels, minimize carrying costs, and ensure the availability of parts as per market demands. Incorporating advanced technologies like RFID and automated inventory systems streamlines warehouse operations, enhancing accuracy and enabling agile responses to fluctuating market demands. Developing an effective distribution network and sales strategies involves tailoring approaches based on regional demands, customer preferences, and technological adoption. With the surge in e-commerce platforms, Prototek leverages online channels to reach a broader customer base. Implementing omnichannel strategies, providing value-added services like technical support, and ensuring efficient logistics contribute to competitive advantages. Challenges Faced by Prototek and Solutions Intense market competition and pricing pressures compel Prototek to seek innovative strategies. Implementing dynamic pricing models based on market fluctuations and consumer behavior analysis can help maintain competitiveness. Moreover, focusing on value-added services, such as technical support, warranties, and efficient logistics, can create differentiation and justify premium pricing. The rapid integration of new technologies profoundly impacts Prototek’s wholesale operations. Investment in upskilling the workforce to handle sophisticated technologies and embracing automation, AI-powered inventory management systems, and predictive analytics optimize operational efficiency and enhance responsiveness to market changes. Disruptions in the supply chain, whether caused by geopolitical tensions, natural disasters, or global crises, pose significant risks. Prototek addresses these challenges by developing resilient supply chains through diversification, adopting just-in-time inventory systems, and fostering collaborative relationships with multiple suppliers across regions, mitigating risks, and ensuring continuity in the face of disruptions. Analysis of Successful Wholesale Automotive Parts Businesses Examining case studies of thriving wholesale automotive parts businesses like Prototek reveals multifaceted strategies. From a focus on niche markets to embracing digital transformations, these case studies emphasize the importance of agility and adaptation. Strategies like personalized customer experiences, data-driven decision-making, and innovative logistics solutions stand out as drivers of success. Market Positioning and Strategic Analysis Prototek strategically positions itself within the market by identifying underserved niches or emerging trends. Crafting tailored solutions, emphasizing quality, and leveraging relationships with OEMs or specialized manufacturers create competitive advantages. Moreover, fostering strong partnerships across the supply chain and investing in sustainable practices contribute to Prototek’s long-term growth and market resilience. Future Trends and Prospects Technological advancements, including electrification, AI, and IoT, will redefine the automotive parts landscape. Prototek understands that embracing these innovations will be key to staying competitive. As the industry evolves, Prototek identifies new market opportunities and anticipates challenges. Opportunities may arise from emerging markets, sustainable practices, or new service models, while challenges might stem from regulatory changes and shifting consumer preferences. The wholesale automotive parts industry, led by adaptable companies like Prototek, thrives on innovation, strategic alignment, and a commitment to excellence. Key aspects encompass efficient supply chain management, adaptation to technological shifts, and strategic market positioning. Future growth for Prototek and the industry as a whole hinges on agility in embracing technological advancements, mitigating risks, and capitalizing on emerging market trends. The journey ahead involves continuous adaptation, innovation, and a commitment to delivering high-quality automotive parts to meet the evolving needs of the global market. In conclusion, as the wholesale automotive parts industry undergoes transformative changes, Prototek stands at the forefront of innovation and adaptability. Navigating the complex landscape of vehicle components and emerging technologies, Prototek ensures a seamless flow of automotive parts, meeting the demands of a dynamic market. If you are in search of high-quality automotive parts, look no further than Prototek. With a commitment to excellence, strategic market positioning, and a deep understanding of evolving industry trends, Prototek is poised to meet your automotive needs. As the industry embraces electrification, AI, and IoT, Prototek remains dedicated to providing cutting-edge solutions. Choosing Prototek means choosing a partner that not only keeps pace with technological advancements but also anticipates future trends. Whether you are an automotive retailer, a repair shop, or a consumer seeking reliable parts, Prototek is your trusted source. Experience the difference with Prototek – where quality meets innovation in the world of wholesale automotive parts. .If
Понимание ударной экструзии алюминия
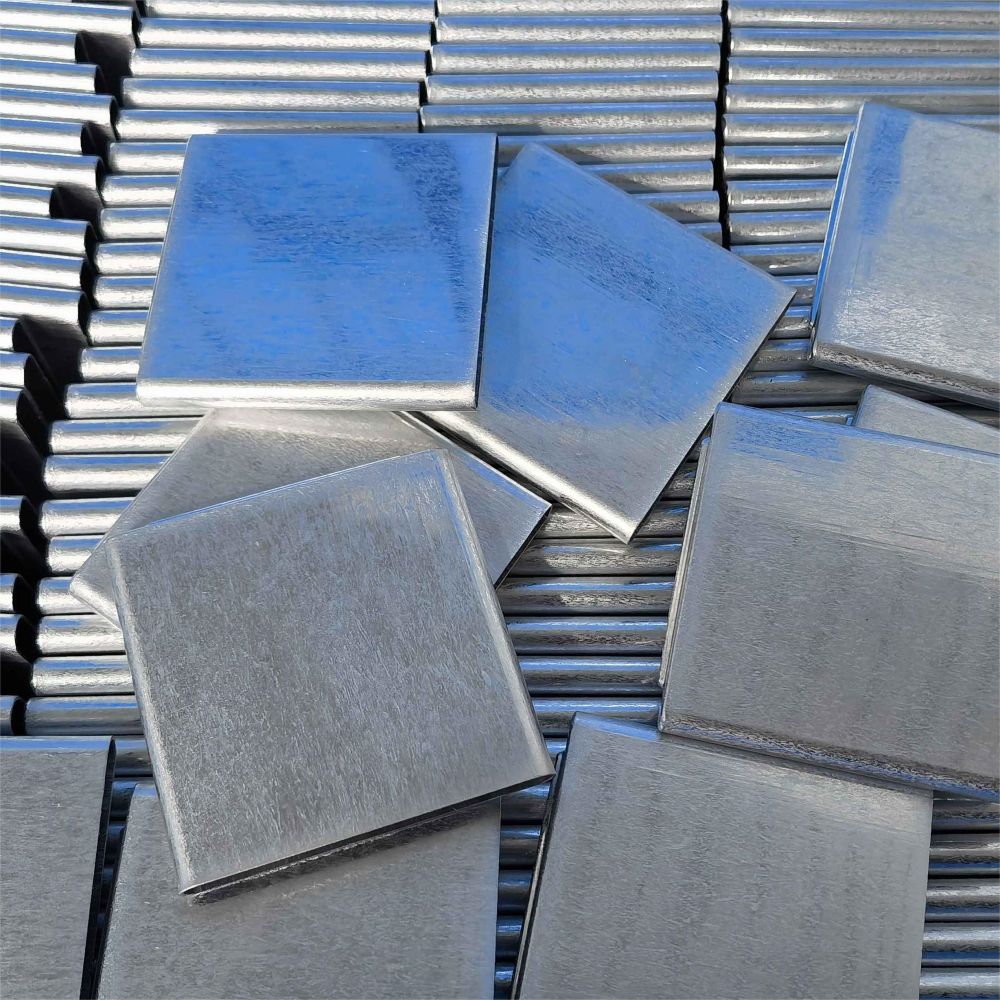
Blog Details Aluminum, renowned for its versatility and lightweight properties, undergoes various manufacturing processes. One increasingly popular and versatile method is Impact Extrusion Aluminum, a technique embraced by Prototek. What is Impact Extrusion Aluminum? Prototek recognizes Impact Extrusion Aluminum as a method involving exerting extreme pressure on aluminum blanks to shape them into precise forms using a die. This controlled deformation process allows for the creation of intricate and accurately designed products, offering a unique manufacturing solution. Applications Across Industries Prototek acknowledges the extensive harnessing of impact extrusion aluminum across industries. In the automotive sector, this method empowers the creation of lightweight yet robust components, enhancing vehicle performance and fuel efficiency. Prototek witnesses its application in engine components and structural elements, benefiting from the material’s exceptional properties. Furthermore, in the packaging industry, Prototek notes the pivotal role of impact extrusion aluminum. It’s instrumental in producing durable containers and packaging solutions that prioritize the safe storage and transportation of food and beverage products. Its corrosion-resistant nature also proves beneficial in pharmaceutical packaging. Moreover, the aerospace sector leverages impact extrusion aluminum for its high-strength and lightweight properties. Prototek acknowledges its contribution to the construction of aircraft components requiring reliability and reduced weight. Why the Popularity? Prototek acknowledges the multifaceted appeal of impact extrusion aluminum. Its lightweight nature significantly reduces overall product weight without compromising strength, making it an ideal choice for industries aiming for improved efficiency and reduced fuel consumption. Furthermore, the cost-effectiveness of the process, coupled with the material’s recyclability, contributes to its popularity. It aligns with sustainability goals, offering an eco-friendly alternative without compromising performance. The Process Unveiled Prototek understands the meticulous process involved in impact extrusion aluminum. Initially, aluminum blanks, typically cylindrical in shape, are precisely prepared. These blanks are then placed in a chamber where extreme pressure is applied, forcing the metal into a die. The result is a precisely formed product, intricately designed as per the die’s specifications. This controlled deformation process ensures the creation of products with high accuracy and intricate detailing, catering to various industry needs. Looking Ahead Prototek acknowledges the role of innovation in driving advancements in impact extrusion aluminum. Current trends emphasize improving process efficiency and exploring new applications. Future developments might witness its integration into previously unexplored industries and the creation of even more intricate shapes with heightened precision. Impact extrusion aluminum exemplifies the ingenuity of manufacturing processes. Its adaptability, cost-efficiency, and environmental sustainability, as recognized by Prototek, position it as a pivotal method across various industries. As technological advancements persist, Prototek anticipates its further integration and expanded applications, solidifying its integral role in modern manufacturing practices. For any inquiries or consultations, please don’t hesitate to contact Prototek. We are committed to providing comprehensive solutions and expertise in impact extrusion aluminum and other innovative manufacturing techniques.If you have any needs, contact us via email: Lynnyao@prototekparts.com or phone: +86-0792-86372550 Tags: Social Network: Recently Posts Online Help! +(86) 0791-86372550 WANT TO DISCUSS IN DETAIL Contact Our Consultant Now CONTACT NOW
Исследование лучшего алюминия для обработки на станках с ЧПУ
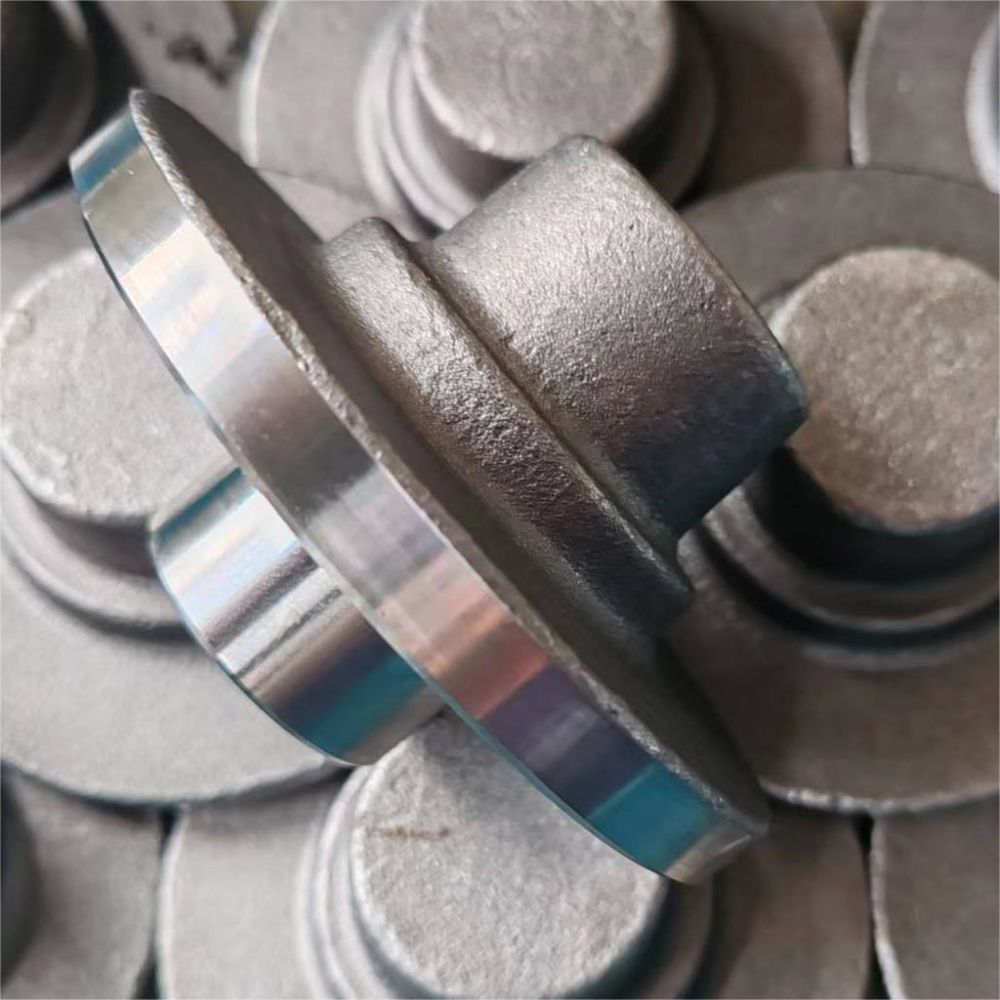
Blog Details Aluminum, a versatile metal widely used in manufacturing, undergoes CNC machining for various applications. Selecting the right aluminum is pivotal to the machining process. Let’s delve into the essentials of choosing the best aluminum for CNC machining. The importance of aluminum in CNC machining cannot be overstated. CNC machining, a precise manufacturing technique, relies heavily on aluminum for its properties of being lightweight yet durable. The versatility of aluminum finds its way into multiple industries, making it a cornerstone in CNC machining for companies like Prototek. Significance of Choosing the Right Aluminum The choice of aluminum alloy profoundly impacts the CNC machining process and the final product’s quality. Here’s a deeper dive into why selecting the appropriate aluminum is critical: Influence on Machining Properties Different aluminum alloys exhibit varying characteristics such as hardness, strength, and machinability. Alloys like the 6XXX series offer a favorable balance of these properties, enabling efficient CNC machining without compromising on structural integrity. The right aluminum can significantly ease the machining process, reducing production time and costs for companies like Prototek. Please confirm if the following revised version meets your requirement: “Please consider the effect on the product’s performance.” The properties of the chosen aluminum directly affect the performance and durability of the final product. For instance, in applications demanding high strength, alloys from the 7XXX series like 7075 excel due to their superior strength-to-weight ratio, ensuring reliability in critical components. Conversely, for projects prioritizing corrosion resistance, alloys from the 5XXX series, such as 5083, provide optimal protection against environmental factors, extending the product’s lifespan—important considerations for Prototek’s diverse clientele. Cost-efficiency and Material Optimization Selecting the most suitable aluminum alloy ensures efficient use of resources for Prototek. By choosing an alloy that meets specific requirements without unnecessary over-engineering, manufacturers can optimize material usage and reduce production costs. This approach fosters cost-efficiency without compromising the quality or performance of the machined parts manufactured by Prototek. Adaptability to Manufacturing Processes Aluminum alloys tailored for CNC machining streamline the manufacturing process for Prototek. Alloys with excellent formability and machinability, like those from the 6XXX series, facilitate intricate designs and precise machining, enhancing the adaptability of the material to various manufacturing techniques and equipment used by Prototek. Environmental Impact Considering the environmental implications of aluminum selection is crucial for Prototek. Some alloys may require specific treatments or processing methods that impact the environment differently. Choosing alloys with properties that align with environmental sustainability goals or those that require fewer resources for processing can contribute to more eco-friendly manufacturing practices by Prototek. Regulatory Compliance and Standards Certain industries necessitate adherence to specific standards and regulations, an aspect carefully considered by Prototek. The chosen aluminum should meet these compliance requirements, ensuring the final product’s suitability for its intended use and industry guidelines. The significance of selecting the right aluminum for CNC machining extends beyond the immediate manufacturing process for Prototek. It influences the performance, cost-effectiveness, and environmental implications throughout the product’s lifecycle, making it a pivotal decision in the production chain. A Glimpse into Aluminum Alloys Aluminum alloys encompass a spectrum of options, each with its own unique properties, making them suitable for distinct applications: 1XXX Series: Pure Aluminum Comprising almost entirely of aluminum, this series boasts exceptional corrosion resistance and high thermal conductivity. However, its strength is relatively low compared to alloyed counterparts, limiting its use in high-stress applications. 2XXX Series: Aluminum-Copper Alloys Known for their strength, these alloys possess excellent machinability and are often utilized in aerospace applications due to their high strength-to-weight ratio. However, they may be susceptible to corrosion under certain conditions. 3XXX Series: Aluminum-Manganese Alloys These alloys offer improved strength and are commonly used in applications requiring moderate strength and good formability. They exhibit excellent weldability, making them suitable for various welding techniques. 5XXX Series: Aluminum-Magnesium Alloys Notable for their high corrosion resistance and good weldability, these alloys are widely applied in marine environments and structural components due to their strength and formability. 6XXX Series: Aluminum-Silicon-Magnesium Alloys Highly versatile, this series combines strength, machinability, and corrosion resistance. It finds extensive use in CNC machining applications due to its excellent balance of properties, making it suitable for various industries including automotive, construction, and electronics—industries serviced by Prototek. 7XXX Series: Aluminum-Zinc-Magnesium Alloys Renowned for their exceptional strength, these alloys are commonly employed in aerospace applications where high strength and toughness are crucial. However, they may possess lower corrosion resistance compared to other series. Optimal Aluminum for CNC Machining Among the array of aluminum alloys, the 6XXX series stands out as an optimal choice for CNC machining due to its well-rounded properties. Alloys within this series, such as 6061 and 6063, strike a balance between strength, machinability, and corrosion resistance, making them highly sought after in manufacturing processes, including those conducted by Prototek. Their excellent extrudability and formability further contribute to their popularity in CNC machining, enabling intricate designs and precise manufacturing across various industries. Showcasing Engaging Examples Example 1: Automotive Industry (6XXX Series – 6061 Alloy) In the automotive sector, the 6061 alloy from the 6XXX series finds extensive use in CNC machining for Prototek. Its superior strength, excellent machinability, and corrosion resistance make it ideal for manufacturing components like engine parts, chassis, and wheels. The alloy’s ability to maintain structural integrity under stress while being easily milled or turned in CNC machines makes it a top choice in automotive manufacturing processes at Prototek. Example 2: Marine Applications (5XXX Series – 5083 Alloy) Alloys like 5083 from the 5XXX series excel in marine environments due to their high corrosion resistance, benefiting Prototek’s manufacturing of CNC-machined components such as boat hulls, shipbuilding components, and offshore structures. These components endure harsh marine conditions, relying on the strength and resistance to saltwater corrosion provided by the 5083 alloys. Example 3: Aerospace Engineering (7XXX Series – 7075 Alloy) In the aerospace industry, the 7075 alloy, belonging to the 7XXX series, takes center stage for Prototek. This alloy’s exceptional strength-to-weight ratio and toughness make it a preferred choice for CNC machining
Применение алюминиевых кованых деталей
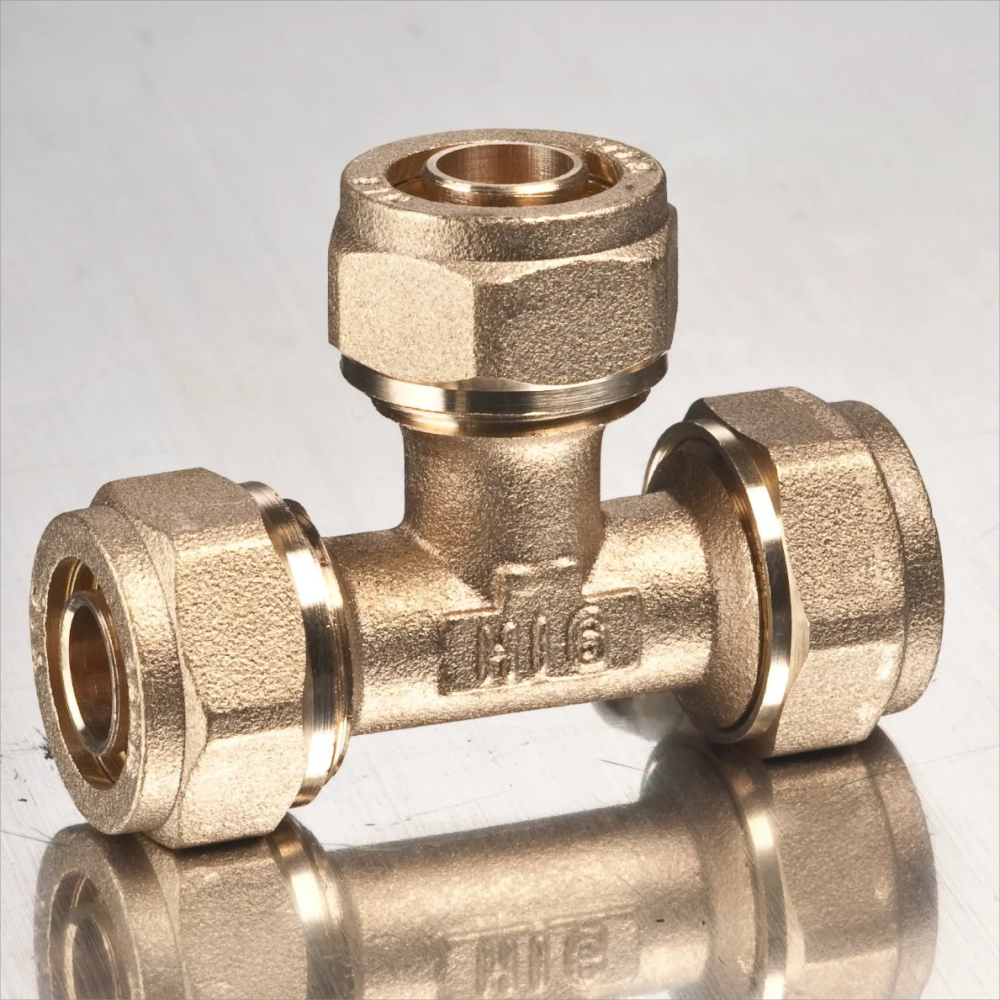
Blog Details In today’s industrial manufacturing realm, aluminum forgings parts have garnered significant attention due to their unique properties and wide array of applications. Crafted through precise techniques and technologies, they bring forth numerous astounding advantages. The Mastery of Manufacturing Processes Plastic Deformation under High Temperature and Pressure The plastic deformation during the manufacturing process of aluminum forgings parts stands as a pivotal element of its intricate craftsmanship. By subjecting aluminum alloys to high temperatures and pressures, the material gains excellent plasticity, allowing it to be precisely forged into desired shapes. For instance, in crafting engine crankshafts, aluminum alloys, when subjected to forging processes at high temperatures, yield products that are more uniform and possess higher strength. Precise Control in Process Steps Every step in the manufacturing of aluminum forgings parts demands precise control to ensure the quality and performance of the final product. The preheating stage requires precise temperature and time control to ensure that the aluminum alloy reaches its optimum plastic state. During forging, controlling pressure and speed is critical to prevent material defects during deformation. Control during the cooling stage affects the final product’s grain structure and strength. Application of Automation Technologies Modern aluminum forging manufacturing extensively employs automation technologies such as CNC machine tools and robots. These technologies enable precise control over each manufacturing step, enhancing production efficiency and product consistency. For example, utilizing CNC machine tools ensures precise control over the machining process of aluminum forgings, ensuring that product dimensions and surface quality meet requirements. Manufacturing Unconventional Shapes Aluminum forging technology also enables the production of unconventional shapes of aluminum alloy products. Through precise mold design and control, complex-shaped aluminum forgings like blades and turbine blades in aerospace engine components, which demand high precision in manufacturing processes, can be produced. Diversity in Application Fields Aluminum forgings parts showcase their versatility and wide-ranging applications across various industries. In the automotive industry, they find extensive use in engine components, vehicle body structures, among other aspects, owing to their lightweight and high-strength characteristics. Simultaneously, in the aerospace industry, aluminum forgings play a vital role in manufacturing critical components like aircraft structures and aviation engines. Manifestation of Characteristics and Advantages Lightweight Characteristics Aluminum forgings are widely used in automotive manufacturing, such as in vehicle body structures, engine components, and suspension systems. For instance, some modern automobiles utilize engine components made of aluminum forgings, like crankshafts and connecting rods, reducing the overall vehicle weight and enhancing fuel efficiency. Strength and Corrosion Resistance In the aerospace industry, aluminum forgings are employed in manufacturing aircraft wings and components of aviation engines. For example, the aluminum forgings used in aircraft wing structures can withstand enormous aerodynamic pressures during high-speed flight, possessing excellent corrosion resistance to ensure long-term flight safety. Sustainability and Environmental Friendliness Aluminum forgings not only find application in the automotive and aerospace fields but also play a significant role in the construction and electronics industries. For instance, some architectural structures utilize aluminum forgings in their manufacturing processes, contributing to sustainable practices and facilitating material recycling, thus reducing material waste and promoting sustainable development. Future Outlook and Development Trends New Technologies and Material Applications With the advancement of 3D printing technology, the aluminum forging industry is exploring its utilization. Through 3D printing, complex-shaped aluminum forgings can be manufactured more precisely, offering more efficient and customized solutions across various industries. Innovation and Development Directions The research and improvement of aluminum alloys stand as a key direction for future development. Scientists and engineers are striving to develop new types of aluminum alloys to enhance their strength, wear resistance, and high-temperature performance, meeting the ever-changing and increasingly stringent industrial demands. The continuous innovation in aluminum alloys and forging techniques promises a broader development landscape for the aluminum forging industry in the future. Prototek has been offering professional custom aluminum forging parts machining parts for over 13 years. If you have any needs about metal manufacturing services, contact us via email: Lynnyao@prototekparts.com or phone: +86-0792-86372550 Tags: Social Network: Recently Posts Online Help! +(86) 0791-86372550 WANT TO DISCUSS IN DETAIL Contact Our Consultant Now CONTACT NOW
The Difference Between Cold Extrusion and Cold Heading

Blog Details Cold extrusion is to put the metal blank in the cold extrusion cavity, at room temperature, through the press fixed punch to the blank pressure, so that the metal blank plastic deformation of the processing method, obviously, cold extrusion processing is to rely on the mold to control the flow of metal, by a large number of metal volume transfer to form parts. In terms of extrusion equipment, China has the ability to design and manufacture extrusion presses at all levels of tonnage. In addition to general mechanical presses, hydraulic presses and cold extrusion presses, friction presses and high speed and high energy equipment have been successfully used for cold extrusion production. The cold heading process is one of the new pressure machining processes for metal with little or no cutting. It is a processing method that uses the plastic deformation of the metal under the action of external force, and with the help of the mold, the metal volume is redistributed and transferred, so as to form the required parts or blanks. The cold heading process is most suitable for the production of bolts, screws, nuts, rivets, pins and other standard fasteners. The common equipment used in cold heading process is the special cold heading machine. If the production volume is not too large, it can also be replaced by a crank press or friction. Cold heading and cold extrusion are basically deformation processing under the same conditions, but the mode of operation is not the same. Cold heading belongs to the forging deformation of smaller workpieces and is often used in fastener industry. Cold extrusion belongs to the extrusion deformation of larger workpieces, which is widely used. Cold heading is equivalent to a branch of cold extrusion, simply speaking, in the process of making bolts, the hexagonal head forming is cold heading, and the rod part shrinking is cold extrusion (extrusion). Non-cutting hexagonal flange bolts (multi-station forming) have both cold heading and cold extrusion. Before forming hexagonal nuts, only cold heading is available, and the hole extrusion in the back process is cold extrusion (positive and negative extrusion). Prototek has been offering professional custom CNC machining parts for over 13 years. If you have any needs about metal manufacturing services, contact us via email: Lynnyao@prototekparts.com or phone: +86-0792-86372550 Tags: Social Network: Recently Posts Online Help! +(86) 0791-86372550 WANT TO DISCUSS IN DETAIL Contact Our Consultant Now CONTACT NOW