Exploring the World of Aluminum Forging Alloy – A Prototek Perspective
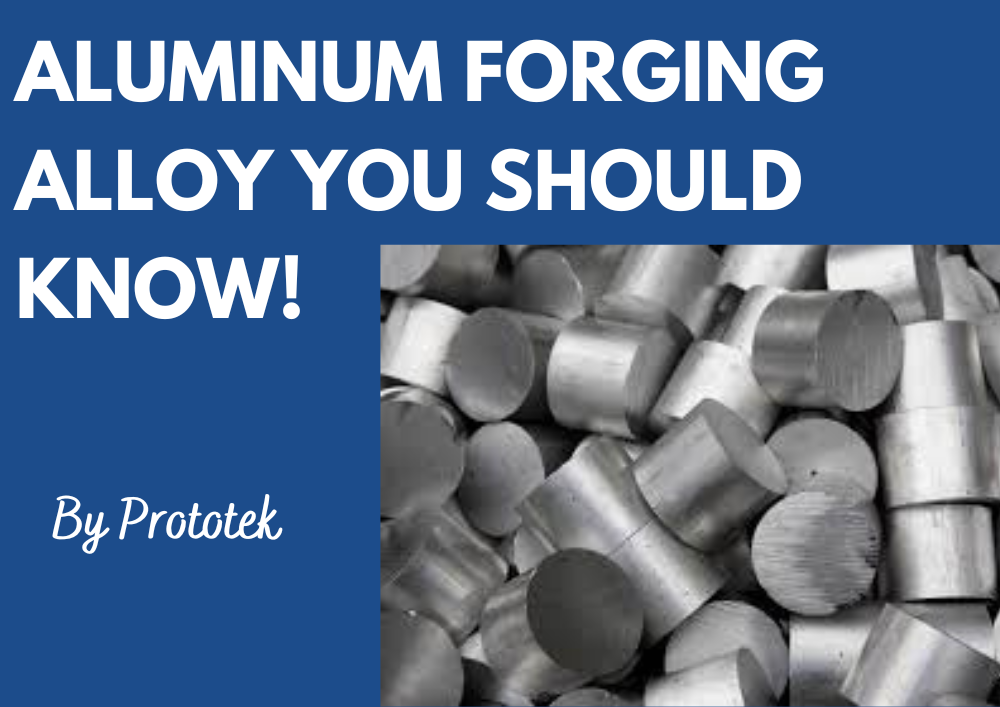
Exploring the World of Aluminum Forging Alloy – A Prototek Perspective Aluminum forging alloys play a pivotal role in various industries, offering lightweight properties, strength, and corrosion resistance. This article delves into the significance, types, characteristics, production processes, applications, and prospects of aluminum forging alloys. Overview of Aluminum Forging Alloys Aluminum forging alloys are essential in various industries for their exceptionally lightweight properties, strength, and corrosion resistance. These alloys undergo the forging process, where aluminum billets are shaped into desired forms under heat and pressure. Resulting in components with superior mechanical properties. Definition: Aluminum forging alloys are specifically formulated materials designed to withstand the rigors of the forging process. They are engineered to exhibit excellent formability, machinability, and mechanical strength. Making them ideal for applications where lightweight yet robust components are required. Applications: The versatility of aluminum forging alloys makes them indispensable in numerous industries. They are extensively used in automotive manufacturing for engine parts, transmission components, and suspension systems. Due to their lightweight nature and high strength-to-weight ratios, these alloys are vital for aircraft structural components, landing gear, and engine parts in the aerospace industry. Additionally, aluminum forging alloys find applications in marine equipment, sporting goods, and architectural structures. Where their corrosion resistance and formability are highly valued. Advantages and Limitations: Aluminum forging alloys offer several advantages, including high strength-to-weight ratios, excellent corrosion resistance, and good machinability. Their lightweight nature contributes to fuel efficiency in automotive and aerospace applications while maintaining structural integrity. However, these alloys may have limitations in terms of weldability and formability, requiring careful consideration during the design and manufacturing process. Types of Aluminum Forging Alloys Aluminum forging alloys are categorized into different series, each with its distinct properties and applications. Among the most commonly used series are the 2XXX and 6XXX series, known for their specific characteristics and widespread industrial usage. 2XXX Series Alloys: The 2XXX series aluminum alloys are characterized by their high strength and excellent fatigue resistance. We are making them well-suited for applications in demanding environments, particularly in the aerospace industry. Alloys such as 2024 and 2014 are prime examples of this series and are extensively utilized in aircraft structural components. Including fuselage frames, wing spars, and bulkheads. These alloys offer exceptional strength-to-weight ratios, essential for maintaining structural integrity while minimizing overall weight. 6XXX Series Alloys: Aluminum alloys within the 6XXX series are renowned for their good formability, weldability, and corrosion resistance, making them versatile materials suitable for various applications. Alloys like 6061 and 6063 are highly sought after in the automotive, marine, and architectural industries due to their excellent combination of mechanical properties and ease of fabrication. They are commonly used in automotive components, extruded profiles, and structural frameworks where lightweight, durable materials are required. Other Important Series: In addition to the 2XXX and 6XXX series, several other notable series of aluminium forging alloys cater to specific industrial needs. For instance, the 7XXX series alloys offer exceptional strength and toughness, making them suitable for high-performance applications such as aerospace and defense. The 5XXX series alloys, on the other hand, are known for their excellent corrosion resistance and are commonly used in marine and chemical processing industries. Each series of aluminium forging alloys is engineered to meet the unique requirements of various applications. They provide manufacturers with a wide array of options based on performance, cost-effectiveness, and processing capabilities. By understanding the characteristics and applications of these alloys, engineers, and designers can select the most suitable materials for their specific manufacturing needs. Characteristics of Aluminum Forging Alloys Aluminium forging alloys possess various characteristics that make them highly desirable materials for various applications across different industries. These characteristics contribute to their widespread use and effectiveness in meeting the demands of modern manufacturing processes. Mechanical Performance: One of the key characteristics of aluminium forging alloys is their impressive mechanical performance. These alloys exhibit excellent strength-to-weight ratios, allowing for the fabrication of lightweight components without compromising on structural integrity. Whether in tension, compression, or shear, aluminium forging alloys demonstrate remarkable mechanical properties. Making them suitable for critical applications where strength and durability are paramount. Corrosion Resistance: Another significant characteristic of aluminium forging alloys is their exceptional corrosion resistance. Aluminium naturally forms a protective oxide layer on its surface, which protects against environmental factors such as moisture, chemicals, and saltwater exposure. This inherent corrosion resistance makes aluminium forging alloys ideal for use in marine environments, chemical processing plants, and other applications where exposure to corrosive elements is a concern. Heat Treatability: Aluminium forging alloys are highly heat treatable, allowing precise control over their mechanical properties through various heat treatment processes. Heat treatment can significantly enhance these alloys’ strength, hardness, and toughness, making them suitable for applications requiring specific performance criteria. By carefully manipulating the material’s microstructure through processes such as quenching and aging. Manufacturers can tailor the properties of aluminium forging alloys to meet the requirements of their intended application. Machinability: Aluminum forging alloys exhibit good machinability, facilitating ease of fabrication and production efficiency. These alloys can be readily machined using conventional methods such as milling, drilling, turning, and grinding, allowing for the creation of complex shapes and intricate designs. Their excellent machinability enables manufacturers to achieve tight tolerances and high-quality surface finishes, resulting in components that meet strict performance standards. Recyclability: A notable characteristic of aluminium forging alloys is their recyclability, contributing to their sustainability and environmental friendliness. Aluminum is one of the most recycled materials in the world, able to be repeatedly recycled without losing its inherent properties. Recycling consumes significantly less energy than primary aluminum production. Making recycled aluminum forging alloys an economically viable and environmentally responsible choice for manufacturers. In summary, aluminum forging alloys’ characteristics, including their mechanical performance, corrosion resistance, heat treatability, machinability, and recyclability, make them versatile and valuable materials for various applications. By leveraging these characteristics, manufacturers can produce high-quality components that meet modern industry’s rigorous demands while promoting sustainability and environmental stewardship. Production Processes for Aluminum Forging Alloys The production of aluminum forging alloys involves several intricate