What is Deep Drawing and How Does the Process Work
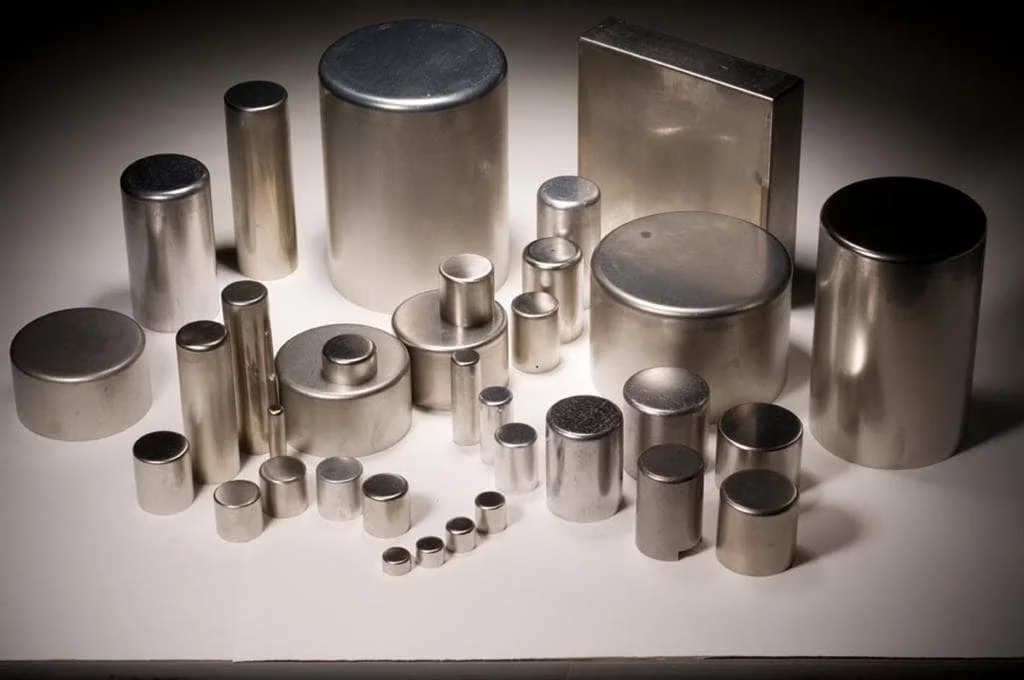
What is Deep Drawing and How Does the Process Work Deep drawing is an essential metal-forming process that transforms flat sheets of metal into intricate three-dimensional shapes. This technique is widely employed to produce a variety of hollow, cylindrical parts, including cups, cans, pots, and automotive components, where the depth exceeds the diameter. The deep drawing process In its simplest form, deep drawing creates a tall, smooth, closed-ended part with the same sheet thickness as the blank by forcing a sheet metal blank into a die chamber with a punch. The punch’s diameter must be within an acceptable size range for the material, the lead-in of the die and the punch’s nose must be radiused, and the clearances between the punch and die must be carefully controlled to promote metal flow. The portion will wrinkle if there is too much clearance. If you use too little, the portion will tear. To reduce flaws and enable deeper draws, many deep draw systems include a blank holder and pressure pad. consists of several critical steps: Blanking: A flat sheet of metal, known as a blank, is precisely cut from a larger sheet to achieve the desired size and shape. Drawing: The blank is positioned over a die with a cavity that corresponds to the desired final shape. A punch forcefully drives the blank into the die cavity, effectively stretching and bending it into the required form. Redrawing: In many cases, multiple drawing operations are necessary to achieve the specified depth and shape. Redrawing involves passing the partially formed part through a series of dies, further refining its shape. Trimming: Excess material is systematically trimmed from the formed part to ensure it meets the final specifications and dimensions. Deep drawing stands out as a versatile and cost-effective manufacturing process capable of producing complex shapes with precise tolerances. Advantages The deep drawing process in sheet metal has the following advantages when manufacturing sheet metal parts in large production volumes. Manufacture hollow cylindrical, rectangular, square, and other complex geometries Low manufacturing /labor cost. Less material consumption. High productivity. Highly precise parts. High strength and minimum weight parts. Low tool construction cost compared to progressive stamping tool Application When to use deep drawing? Deep drawing works best with ductile metals. In general, any metal that can be cold rolled into a sheet should have sufficient ductility to be deep drawn, but material properties like work hardening or anisotropy also may need to be considered. Appropriate materials include aluminum alloys, brass, copper, and copper alloys, titanium, cold rolled low carbon sheet steel and some stainless steel. Ideal shapes for deep drawing include rectangles and axisymmetric structures like cylinders or hemispheres, but the process can handle more complex shapes, too. Tooling and setup costs can vary widely depending on the shape being produced. For simple shapes, costs can be lower than other processes, but with increased complexity comes increased cost. In some cases, that cost may be offset by deep drawing’s minimal downtime, low maintenance, and reduced technical labor requirements over the product’s lifetime. Factors that can increase complexity include: Presence and location of part features Direction of features Protrusion of features Part size and proportions, including material thickness Deep drawing parts can be used in a wide range of industries, including: Construction: Bending components for construction projects such as roofing and siding Automotive: Bending sheet metal for use in body parts such as doors, hoods, and fenders Aerospace: Bending sheet metal for use in the manufacturing of fuselage, doors, and fenders. Advertising: Bending sheet metal for signage and advertising, including signs and billboards Food processing: Bending sheet metal for beverages, kitchen equipment Transportation: Bending sheet metal parts for cars, trains, buses, and aircraft Art: Bending sheet metal for use in building cladding Common Problems During the Deep Drawing Process Deep-drawn sheet metal parts can exhibit several defects if deep-drawing part design guidelines are not followed or if the manufacturing process parameters are not properly set. The following are common issues: Wrinkling Wrinkling defects appear in the vertical wall or flange of deep-drawn sheet metal parts due to high radial and tangential compressive stresses. This issue can be prevented through effective tool and process design. Tearing and Thinning Tearing and thinning occur in the inner section of the deep-drawn part as a result of high shank holder pressure, which restricts the free movement of the material, leading to elevated tensile stresses in that region. Additionally, tearing may occur due to a small corner radius. Surface Defects Surface defects, such as scratches and tool or die marks, can arise from a small clearance between the tool and die or inadequate lubrication. Earing Earing defects cause irregular features on the flange of deep-drawn parts and result from the anisotropic behavior of the material. By addressing these issues, manufacturers can improve the quality of deep-drawn components. If you have any needs, contact us via email at Lynnyao@prototekparts.com or phone: +86-0792-86372550 Tags: Social Network: Recently Posts Online Help! +(86) 0791-86372550 Have Questions? Want To Discuss In Detail? Contact Our Consultant Now CONTACT