Forged Forming
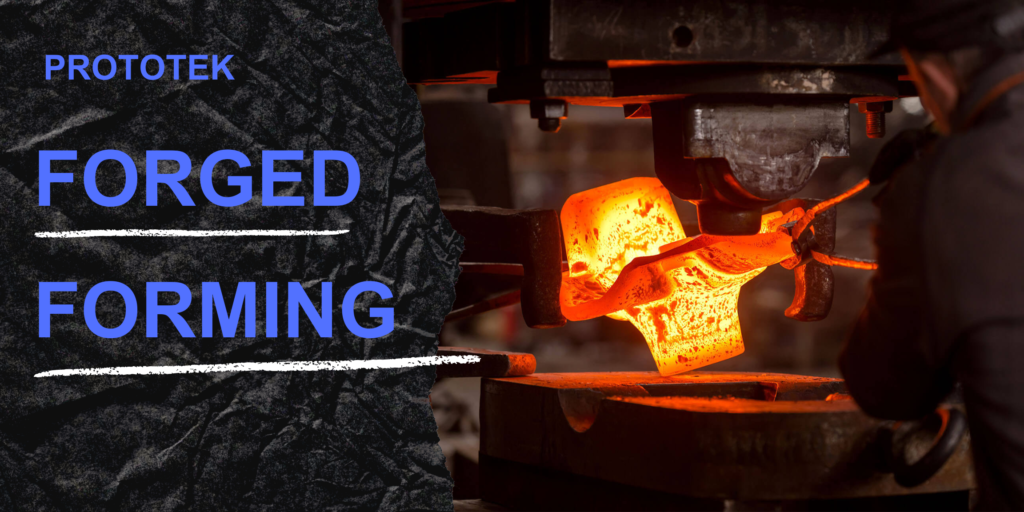
Blog Details Forged forming, a metalworking process involving the application of pressure to reshape metals has become indispensable across various industries. From automotive manufacturing to aerospace engineering and construction, forged forming techniques play critical roles in shaping metals to meet specific requirements. This paper thoroughly reviews forged forming techniques, their applications, advantages, and future prospects. The review encompasses cold and hot forging methods, their principles, and their respective applications in diverse industries. Additionally, it explores the advancements in forged forming technologies, including the integration of artificial intelligence and robotics, and their potential impact on future manufacturing processes. Forged Forming Techniques Cold Forging: Principles and Applications Cold forging is a metalworking process performed at or near room temperature. In this process, the metal is shaped using dies under high pressure. The process involves deforming the metal without heating it significantly, improving dimensional accuracy and surface finish. Cold forging is commonly used for producing small to medium-sized parts with intricate shapes, such as bolts, nuts, and automotive components like gears and shafts. The advantages of cold forging include enhanced mechanical properties, reduced material waste, and minimal post-processing requirements. At Prototek, cold forging is widely used in various industries to produce small to medium-sized components with high dimensional accuracy and surface finish. Some specific applications of cold forging include: Automotive Components Prototek extensively uses cold forging in the automotive industry for manufacturing a wide range of components, including bolts, nuts, screws, and shafts. These components are critical for the assembly of engines, transmissions, steering systems, and suspension systems in vehicles. Cold forging offers improved mechanical properties, cost-effectiveness, and high production efficiency. Aerospace Fasteners Prototek employs cold forging in the aerospace sector for producing high-strength fasteners such as bolts, rivets, and screws used in aircraft assembly. These fasteners require precise dimensions, excellent surface finish, and superior mechanical properties to ensure the safety and reliability of aerospace structures. Cold forging enables the production of aerospace fasteners with tight tolerances and high strength-to-weight ratios. Electrical and Electronic Components Prototek utilizes cold forging to manufacture electrical and electronic components, including connectors, terminals, and contact pins. These components require precise shaping and dimensional accuracy to ensure proper functionality and reliability in electrical circuits and electronic devices. Cold forging allows for the mass production of high-quality electrical and electronic components with consistent performance. Consumer Goods Prototek uses cold forging to produce various consumer goods, such as tools, hardware, and appliances. Components like wrenches, screwdrivers, hinges, and door handles are often manufactured using cold forging due to their durability, precision, and cost-effectiveness. Cold forging enables the production of intricate shapes and designs with minimal material waste. Cold forging is favoured for applications requiring tight tolerances, excellent surface finish, and high production volumes. Its versatility and efficiency make it a preferred choice across industries where precision-engineered components are essential. Hot Forging: Principles and Applications Hot forging, in contrast to cold forging, involves heating the metal above its recrystallization temperature before shaping it using dies and presses. This process allows for greater deformation without the risk of work hardening and enables the forging of complex shapes and larger components. Hot forging is particularly suitable for materials with high strength and low ductility, such as alloy steels and titanium alloys. Common applications of hot forging include aerospace structural components, automotive crankshafts, and industrial machinery parts. The main advantages of hot forging include improved material flow, better formability, and reduced energy consumption compared to cold forging. Prototek employs hot forging in shaping metal parts by heating them above their recrystallization temperature and applying compressive forces using dies and presses. This process is suitable for producing large, complex components with superior mechanical properties. Some specific applications of hot forging include: Aerospace Structural Components Prototek extensively uses hot forging in the aerospace industry to manufacture critical structural components such as turbine disks, landing gear parts, wing spars, and engine mounts. These components require high strength, fatigue resistance, and dimensional stability to withstand the demanding conditions of aerospace operations. Hot forging ensures the uniform flow of material and the formation of fine-grained microstructures, resulting in parts with enhanced mechanical properties. Automotive Crankshafts Prototek employs hot forging to produce automotive crankshafts, essential components of internal combustion engines. Crankshafts undergo significant mechanical stresses during engine operation, requiring them to be made from materials with high strength and fatigue resistance. Hot forging allows for the production of crankshafts with complex geometries, precise tolerances, and improved mechanical properties, ensuring reliable engine performance. Industrial Machinery Parts Prototek uses hot forging to manufacture various components in industrial machinery, such as gears, shafts, couplings, and valves. These components are subjected to heavy loads, high temperatures, and abrasive environments in industrial applications. Hot forging enables the production of parts with enhanced strength, wear resistance, and dimensional accuracy, contributing to industrial equipment’s overall reliability and efficiency. Oil and Gas Equipment Prototek employs hot forging in the oil and gas industry to produce components used in drilling, extraction, and processing operations. Parts such as drill bits, wellhead components, valves, and pipeline fittings require high strength, corrosion resistance, and toughness to withstand harsh operating conditions. Hot forging allows for the fabrication of robust components with superior metallurgical properties, ensuring the integrity and safety of oil and gas infrastructure. In summary, hot forging is favoured for applications requiring large, complex components with superior mechanical properties and resistance to extreme conditions. Its ability to produce parts with refined microstructures and enhanced mechanical properties makes it indispensable in industries where reliability and performance are paramount Comparison of Cold and Hot Forging Methods Cold and hot forging offers distinct advantages and is chosen based on material properties, part geometry, and production requirements. Cold forging is preferred for smaller parts requiring high dimensional accuracy and surface finish, while hot forging is ideal for larger components with complex shapes and superior mechanical properties. The choice between cold and hot forging depends on material type, production volume, and cost considerations. Advances in Forged Forming Technologies Recent advancements in forged forming technologies have focused on
The Ultimate Knowledge of Stainless Steel Machining Parts
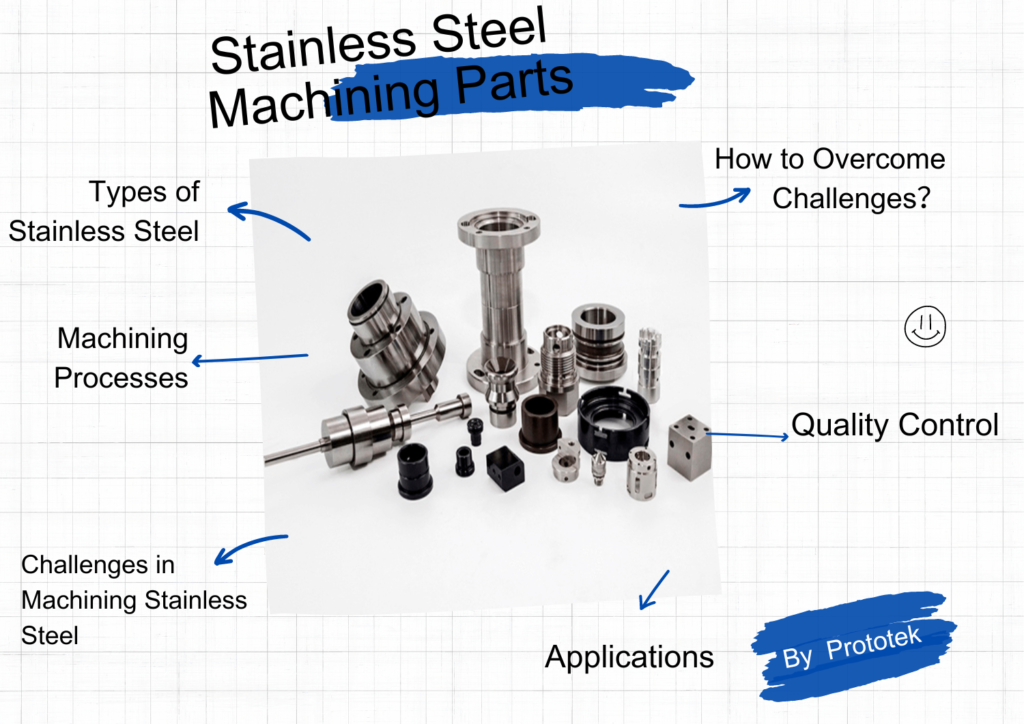
Blog Details Stainless steel machining parts are essential for various industries due to their durability, corrosion resistance, and aesthetic appeal. These parts are crafted using various machining processes, ensuring they meet the precise specifications required for different applications. Understanding the types of stainless steel used, the machining processes, and the challenges involved can help you make informed decisions about using stainless steel for your projects. Types of Stainless Steel Used in Machining Stainless steel comes in various grades, each offering unique properties suitable for different applications and machining processes. Understanding the characteristics of these grades can help select the right type of stainless steel for specific needs. 304 Stainless Steel Properties and Advantages Composition: Contains 18% chromium and 8% nickel, making it an austenitic stainless steel. Corrosion Resistance: High resistance to corrosion, particularly against various acids found in food processing environments. Weldability: Excellent weldability without the need for post-weld annealing. Formability: Good formability, making it easy to shape and fabricate. Temperature Tolerance: Performs well in both high and low temperatures. Typical Uses Food Processing Equipment: Due to its resistance to corrosion and ease of cleaning, it is widely used in kitchen sinks, countertops, and brewing equipment. Chemical Containers: Suitable for storing chemicals that are not highly corrosive. Architectural Applications: Used in exterior accents and structures due to its aesthetic appeal and durability. 316 Stainless Steel Properties and Advantages Composition: Contains 16% chromium, 10% nickel, and 2% molybdenum, which enhances its corrosion resistance. Enhanced Corrosion Resistance: Superior resistance to chlorides and industrial solvents, making it ideal for harsh environments. Strength and Durability: Maintains strength and toughness at both high and low temperatures. Weldability and Fabrication: Similar to 304, it has good weldability and is easy to fabricate. Typical Uses Marine Applications: Often used in marine environments due to its resistance to saltwater corrosion. Medical Devices: Common in surgical instruments and implants because of its biocompatibility. Chemical Processing: Used in equipment that handles corrosive chemicals. 410 Stainless Steel Properties and Advantages Composition: Contains 11.5% to 13.5% chromium, making it a martensitic stainless steel. High Strength: Known for its high mechanical strength and hardness. Heat Treatment: Can be heat treated to achieve a wide range of hardness and mechanical properties. Moderate Corrosion Resistance: Provides adequate resistance to corrosion for many applications. Typical Uses Cutlery and Tools: Used in the production of knives and cutting tools due to its hardness. Surgical Instruments: Suitable for certain surgical instruments that require high strength. Valves and Pumps: Used in manufacturing parts that require both strength and moderate corrosion resistance. 416 Stainless Steel Properties and Advantages Composition: Contains 12-14% chromium and added sulfur, making it a free-machining variation of 410. Machinability: Enhanced machinability due to the addition of sulfur, which improves chip breaking. High Strength: Retains the high strength and hardness characteristics of 410. Corrosion Resistance: Similar to 410, with adequate resistance for many applications. Typical Uses Fasteners: Commonly used in screws, bolts, and other fasteners that require precise machining. Gears: Ideal for gears and shafts due to its machinability and strength. Automotive Components: Used in various automotive parts where machinability and moderate corrosion resistance are needed. Comparison of Different Grades Each grade of stainless steel offers distinct properties, making them suitable for different machining and application requirements: 304 vs. 316: While both are austenitic and highly corrosion-resistant, 316 offers superior resistance to chlorides and harsh chemicals due to adding molybdenum. This makes 316 more suitable for marine and medical applications. 410 vs. 416: Both are martensitic and offer high strength, but 416’s enhanced machinability makes it preferable for parts requiring intricate machining. However, it has slightly lower corrosion resistance compared to 410. Overall: The choice between these grades depends on factors such as corrosion resistance requirements, strength, machinability, and the specific environmental conditions the parts will be exposed to. Machining Processes for Stainless Steel Parts Machining stainless steel involves various techniques that shape and form the material to meet specific design and functional requirements. Each process offers distinct advantages and is chosen based on the desired outcome of the machined parts. Turning Turning is a machining process where a cutting tool removes material from a rotating stainless steel workpiece. This process is typically performed on a lathe, which creates cylindrical parts. Process Details Lathe Setup: The workpiece is secured in a chuck and rotated at high speed. Tool Movement: A cutting tool moves linearly along the axis of rotation to remove material. Precision: Allows for high precision and smooth finishes. Applications Shafts and Rods: Commonly used for producing shafts, rods, and other cylindrical components. Threaded Parts: Ideal for creating threads on screws, bolts, and other fasteners. Milling Milling involves using rotary cutters to remove material from a stationary workpiece. This versatile process can produce a wide range of shapes and features. Process Details Milling Machines: Utilizes either horizontal or vertical milling machines. Cutting Tools: Employs various cutting tools such as end mills, face mills, and ball nose cutters. Movement: The workpiece can move along multiple axes to achieve the desired shape. Applications Complex Shapes: Suitable for parts with complex geometries, slots, holes, and pockets. Flat Surfaces: Often used to create flat surfaces, grooves, and intricate patterns. Drilling Drilling creates holes in stainless steel parts using rotary cutting tools called drill bits. Process Details Drill Press: Performed using a drill press or a CNC machine. Drill Bits: Various drill bits, such as twist and center drills, are used. Coolant Use: Coolants are often applied to reduce heat and improve tool life. Applications Fastener Holes: Commonly used for creating holes for screws, bolts, and other fasteners. Fluid Passages: Essential for parts requiring precise fluid or gas passages. Grinding Grinding uses abrasive wheels to achieve high surface quality and precise dimensions on stainless steel parts. Process Details Abrasive Wheels: Different abrasive wheels, such as grinding wheels and belts, are used. Surface Finish: Capable of achieving very fine surface finishes. Precision: Provides high dimensional accuracy and smooth surfaces. Applications Surface Finishing: Often used as a finishing process to achieve the
Exploring the World of Aluminum Forging Alloy – A Prototek Perspective
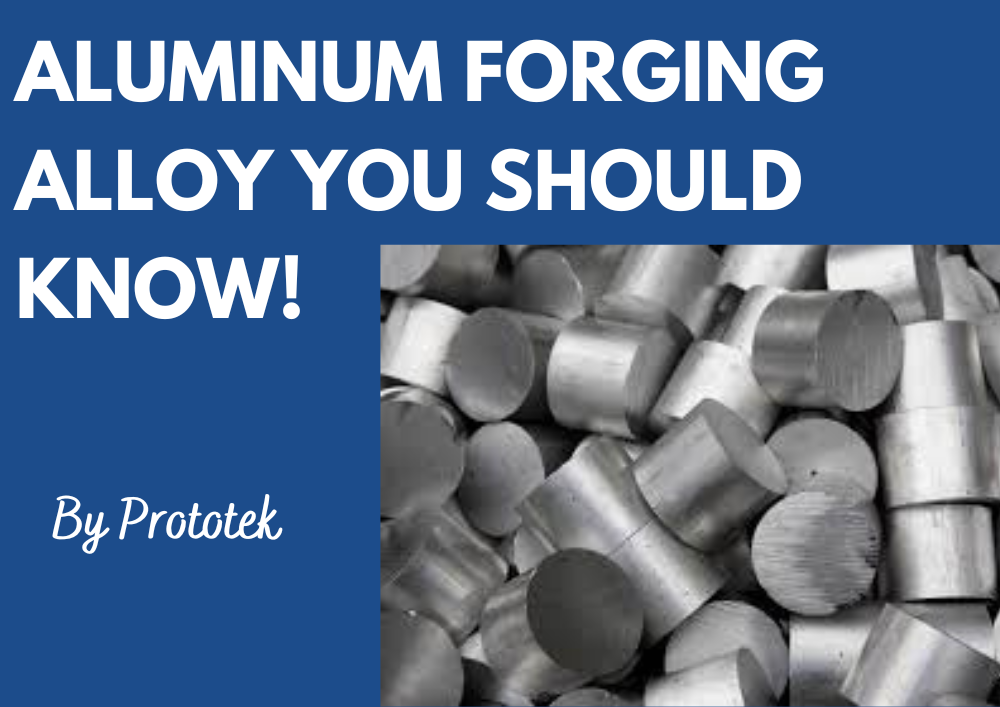
Exploring the World of Aluminum Forging Alloy – A Prototek Perspective Aluminum forging alloys play a pivotal role in various industries, offering lightweight properties, strength, and corrosion resistance. This article delves into the significance, types, characteristics, production processes, applications, and prospects of aluminum forging alloys. Overview of Aluminum Forging Alloys Aluminum forging alloys are essential in various industries for their exceptionally lightweight properties, strength, and corrosion resistance. These alloys undergo the forging process, where aluminum billets are shaped into desired forms under heat and pressure. Resulting in components with superior mechanical properties. Definition: Aluminum forging alloys are specifically formulated materials designed to withstand the rigors of the forging process. They are engineered to exhibit excellent formability, machinability, and mechanical strength. Making them ideal for applications where lightweight yet robust components are required. Applications: The versatility of aluminum forging alloys makes them indispensable in numerous industries. They are extensively used in automotive manufacturing for engine parts, transmission components, and suspension systems. Due to their lightweight nature and high strength-to-weight ratios, these alloys are vital for aircraft structural components, landing gear, and engine parts in the aerospace industry. Additionally, aluminum forging alloys find applications in marine equipment, sporting goods, and architectural structures. Where their corrosion resistance and formability are highly valued. Advantages and Limitations: Aluminum forging alloys offer several advantages, including high strength-to-weight ratios, excellent corrosion resistance, and good machinability. Their lightweight nature contributes to fuel efficiency in automotive and aerospace applications while maintaining structural integrity. However, these alloys may have limitations in terms of weldability and formability, requiring careful consideration during the design and manufacturing process. Types of Aluminum Forging Alloys Aluminum forging alloys are categorized into different series, each with its distinct properties and applications. Among the most commonly used series are the 2XXX and 6XXX series, known for their specific characteristics and widespread industrial usage. 2XXX Series Alloys: The 2XXX series aluminum alloys are characterized by their high strength and excellent fatigue resistance. We are making them well-suited for applications in demanding environments, particularly in the aerospace industry. Alloys such as 2024 and 2014 are prime examples of this series and are extensively utilized in aircraft structural components. Including fuselage frames, wing spars, and bulkheads. These alloys offer exceptional strength-to-weight ratios, essential for maintaining structural integrity while minimizing overall weight. 6XXX Series Alloys: Aluminum alloys within the 6XXX series are renowned for their good formability, weldability, and corrosion resistance, making them versatile materials suitable for various applications. Alloys like 6061 and 6063 are highly sought after in the automotive, marine, and architectural industries due to their excellent combination of mechanical properties and ease of fabrication. They are commonly used in automotive components, extruded profiles, and structural frameworks where lightweight, durable materials are required. Other Important Series: In addition to the 2XXX and 6XXX series, several other notable series of aluminium forging alloys cater to specific industrial needs. For instance, the 7XXX series alloys offer exceptional strength and toughness, making them suitable for high-performance applications such as aerospace and defense. The 5XXX series alloys, on the other hand, are known for their excellent corrosion resistance and are commonly used in marine and chemical processing industries. Each series of aluminium forging alloys is engineered to meet the unique requirements of various applications. They provide manufacturers with a wide array of options based on performance, cost-effectiveness, and processing capabilities. By understanding the characteristics and applications of these alloys, engineers, and designers can select the most suitable materials for their specific manufacturing needs. Characteristics of Aluminum Forging Alloys Aluminium forging alloys possess various characteristics that make them highly desirable materials for various applications across different industries. These characteristics contribute to their widespread use and effectiveness in meeting the demands of modern manufacturing processes. Mechanical Performance: One of the key characteristics of aluminium forging alloys is their impressive mechanical performance. These alloys exhibit excellent strength-to-weight ratios, allowing for the fabrication of lightweight components without compromising on structural integrity. Whether in tension, compression, or shear, aluminium forging alloys demonstrate remarkable mechanical properties. Making them suitable for critical applications where strength and durability are paramount. Corrosion Resistance: Another significant characteristic of aluminium forging alloys is their exceptional corrosion resistance. Aluminium naturally forms a protective oxide layer on its surface, which protects against environmental factors such as moisture, chemicals, and saltwater exposure. This inherent corrosion resistance makes aluminium forging alloys ideal for use in marine environments, chemical processing plants, and other applications where exposure to corrosive elements is a concern. Heat Treatability: Aluminium forging alloys are highly heat treatable, allowing precise control over their mechanical properties through various heat treatment processes. Heat treatment can significantly enhance these alloys’ strength, hardness, and toughness, making them suitable for applications requiring specific performance criteria. By carefully manipulating the material’s microstructure through processes such as quenching and aging. Manufacturers can tailor the properties of aluminium forging alloys to meet the requirements of their intended application. Machinability: Aluminum forging alloys exhibit good machinability, facilitating ease of fabrication and production efficiency. These alloys can be readily machined using conventional methods such as milling, drilling, turning, and grinding, allowing for the creation of complex shapes and intricate designs. Their excellent machinability enables manufacturers to achieve tight tolerances and high-quality surface finishes, resulting in components that meet strict performance standards. Recyclability: A notable characteristic of aluminium forging alloys is their recyclability, contributing to their sustainability and environmental friendliness. Aluminum is one of the most recycled materials in the world, able to be repeatedly recycled without losing its inherent properties. Recycling consumes significantly less energy than primary aluminum production. Making recycled aluminum forging alloys an economically viable and environmentally responsible choice for manufacturers. In summary, aluminum forging alloys’ characteristics, including their mechanical performance, corrosion resistance, heat treatability, machinability, and recyclability, make them versatile and valuable materials for various applications. By leveraging these characteristics, manufacturers can produce high-quality components that meet modern industry’s rigorous demands while promoting sustainability and environmental stewardship. Production Processes for Aluminum Forging Alloys The production of aluminum forging alloys involves several intricate
Exploring Metal Stamping Services: From Concept to Practice
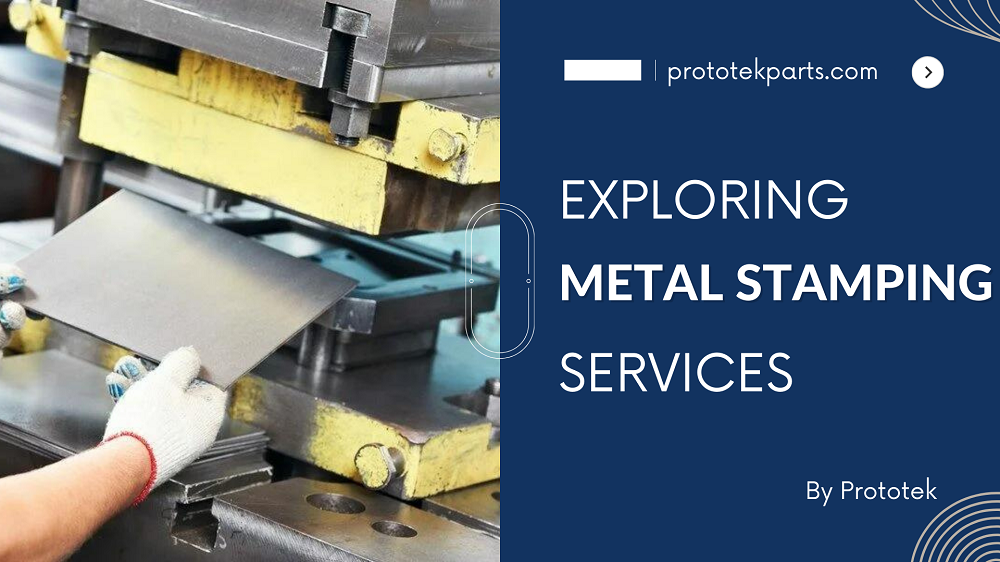
Blog Details Metal stamping services are pivotal in manufacturing, offering efficient solutions for shaping metal components. This article delves into the intricacies of metal stamping, exploring its significance, applications, and considerations for selecting the right service provider. What is Metal Stamping? Metal stamping is a versatile manufacturing process that converts flat metal sheets into various shapes and forms. It involves using presses, dies, and tooling to apply force and manipulate the metal into the desired configuration. The process is commonly employed in automotive, aerospace, electronics, and appliances industries to produce a wide range of components with high precision and efficiency. Process Overview The metal stamping process typically begins with a flat sheet or coil of metal, which is fed into a stamping press. The press applies force to the metal using specialized dies, which are machined to the precise shape and dimensions of the desired part. The metal undergoes various operations such as blanking, piercing, forming, and bending as it progresses through the dies. Each operation is carefully controlled to achieve the desired shape and dimensions of the final part. Blanking and Piercing Blanking is the process of cutting the metal into a specific shape while piercing involves creating holes or openings in the metal sheet. These operations are typically performed in the initial stages of the stamping process to create the basic outline of the part and prepare it for further forming operations. Forming and Bending Forming and bending operations shape the metal into complex geometries and contours. This is achieved by applying controlled pressure to the metal using specialized tooling, which deforms the metal into the desired shape. Forming operations can include drawing, stretching, and deep drawing, depending on the part’s complexity. Secondary Operations After the primary forming operations are complete, the stamped parts may undergo secondary operations such as trimming, machining, welding, or assembly to achieve the final desired specifications. These secondary operations are often necessary to remove excess material, refine features, or join multiple components together. Components of Metal Stamping Presses Presses are the primary machines used in metal stamping, applying force to the metal to deform it into the desired shape. Presses can vary in size and capacity, ranging from small mechanical presses to large hydraulic or servo-driven presses capable of exerting thousands of tons of force. Dies Dies are specialized tooling components that shape and form metal during stamping. They consist of two main parts: the punch, which applies force to the metal, and the die, which provides the desired shape and support for the metal as it is formed. Depending on the application’s requirements, dies can be made from various materials such as tool steel, carbide, or ceramic. Tooling Tooling refers to the various components and accessories used with the presses and dies to facilitate stamping. This includes feeders, grippers, sensors, and safety devices, which help automate and control the stamping operation, ensuring consistent quality and productivity. Advantages of Metal Stamping Metal stamping offers several advantages over other manufacturing processes, including: High Precision: Metal stamping can achieve tight tolerances and intricate geometries, ensuring consistent quality and accuracy in the finished parts. Cost Efficiency: Stamping allows for high-volume production at relatively low per-part costs, making it economical for mass-production applications. Versatility: Metal stamping can be used with various metals, including steel, aluminum, copper, and stainless steel, in various thicknesses and grades. Speed and Efficiency: Stamping processes can be highly automated, allowing for fast cycle times and high production rates, reducing lead times and time-to-market for new products. Types of Metal Stamping Services Single-step Stamping Single-step stamping, or blanking or shallow drawing, involves completing the entire shaping process in a single stroke of the press. This method suits simpler designs and involves basic operations such as cutting, bending, or forming the metal sheet into the desired shape. Single-step stamping often produces flat or shallow parts with minimal complexity. Progressive Stamping On the other hand, progressive stamping is a more advanced technique involving multiple steps or operations performed in sequential dies. As the metal sheet progresses through the press, it undergoes successive operations such as blanking, piercing, forming, and bending in different stages. Each die in the progression performs a specific operation, gradually shaping the metal into the final desired form. Progressive stamping is ideal for producing complex, intricate parts with tight tolerances and high precision. Custom Stamping Custom stamping services cater to unique specifications and low-volume orders, offering flexibility and customization options to meet customers’ specific needs. Custom stamping involves working closely with the client to design and manufacture parts tailored to their requirements, often involving prototype development, tooling design, and testing to ensure the final product meets quality standards. Production Stamping On the other hand, production stamping focuses on the high-volume manufacturing of standardized parts for mass-production applications. Production stamping services are optimized for efficiency, consistency, and cost-effectiveness, emphasizing high-speed operation and repeatability. These services are typically used for producing large quantities of parts with consistent quality and performance, often using automated equipment and processes to maximize productivity. Considerations for Choosing the Right Stamping Service Complexity of Parts The complexity of the parts to be produced is a key factor in determining the type of stamping service required. For simple designs with minimal features, single-step stamping may be sufficient, while complex parts with intricate geometries may require progressive stamping for precision and accuracy. Volume and Scale of Production The volume and scale of production also influence the choice between custom and production stamping services. Custom stamping may be more suitable for low-volume or custom orders, offering flexibility and customization options. Production stamping is often more cost-effective and efficient for high-volume production runs, allowing for large quantities of parts to be produced quickly and consistently. Quality and Precision Requirements The quality and precision requirements of the final parts are critical considerations when selecting a stamping service provider. Both single-step and progressive stamping can achieve high levels of accuracy and repeatability, but the specific capabilities and expertise of the service provider may vary. Choosing a
Understanding Mold Making Services: From Prototyping to Mass Production
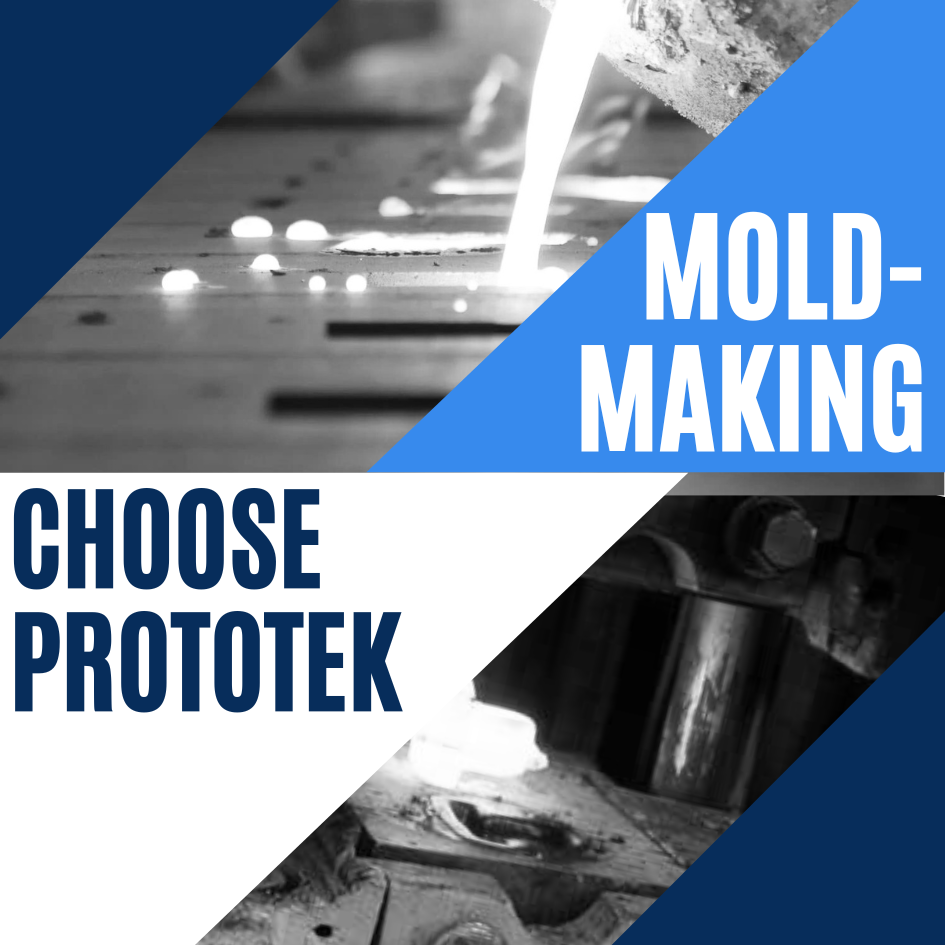
Blog Details In various industries, producing high-quality parts and products often relies on efficient and precise mold making services. These services translate designs into tangible objects, facilitate prototyping, and enable mass production. This article delves into the fundamentals of mold-making services, exploring their processes and benefits and explaining how to choose the right service provider. Basics of Mold Making Understanding Molds Molds are essential tools used in manufacturing to shape raw materials into desired forms. They are the negative space into which materials like plastics, metals, or ceramics are poured or injected, creating finished products. Molds come in various shapes and sizes, ranging from simple one-part molds for basic shapes to complex multi-part molds for intricate designs. The Mold-Making Process The process of mold-making typically involves several distinct stages: 1. Design The design phase is where the specifications and requirements for the mold are established. This includes determining the desired product’s shape, size, and features and selecting the appropriate materials for the mold itself. Modern design tools, such as computer-aided design (CAD) software, are often utilized in this stage to create precise blueprints of the mold. 2. Manufacturing Once the design is finalized, the actual manufacturing of the mold begins. Manufacturing techniques may vary depending on factors like the complexity of the design and the chosen materials. Common methods include machining, casting, and additive manufacturing (e.g., 3D printing). Skilled craftsmen or advanced machinery are employed to transform raw materials into finished mold components. 3. Testing After manufacturing the mold components, they undergo rigorous testing to ensure they meet the specified criteria. Testing may involve verifying dimensional accuracy, assessing material compatibility, and conducting trial runs to simulate real-world production conditions. Any issues or discrepancies discovered during testing are addressed through modifications or adjustments to the mold design or manufacturing process. 4. Revision Based on the results of testing, revisions to the mold design or manufacturing process may be necessary to address any identified issues or optimize performance. This iterative process continues until the mold meets the desired quality, functionality, and reliability standards. Importance of Precision and Accuracy Precision and accuracy are paramount in mold making. Even minor deviations from the intended specifications can result in defective parts or products, leading to waste, rework, and increased production costs. Therefore, meticulous attention to detail and adherence to tight tolerances are critical throughout the mold-making process to ensure consistent, high-quality results. Materials Used in Mold Making The choice of materials for mold making depends on various factors, including the type of product being manufactured, the production volume, and the desired characteristics of the finished mold. Common materials used in mold making include: Metals (e.g., aluminum, steel) for durable, long-lasting molds suitable for high-volume production. Plastics (e.g., epoxy, silicone) are used for cost-effective, flexible molds that are ideal for prototyping and low-volume production. Composites (e.g., fiberglass, carbon fiber) for lightweight, high-strength molds capable of withstanding demanding manufacturing environments. Each material offers unique advantages and considerations in terms of strength, durability, thermal conductivity, and moldability, which must be carefully evaluated to determine the most suitable option for a given application. Types of Mold-Making Services Prototyping Mold-Making Services Prototyping molds plays a crucial role in the product development process by enabling the creation of initial versions of a product for testing, validation, and refinement. These molds are designed to produce prototypes quickly and cost-effectively, allowing designers and engineers to iterate on designs and make necessary modifications before proceeding to mass production. Process and Technologies Prototyping molds employ various advanced manufacturing technologies to rapidly create prototypes with precision and accuracy. Some common techniques include: 3D Printing: Additive manufacturing processes such as stereolithography (SLA), selective laser sintering (SLS), and fused deposition modeling (FDM) are widely used for producing prototype molds directly from digital designs. 3D printing offers fast turnaround times and the ability to create complex geometries with minimal tooling costs. CNC Machining: Computer numerical control (CNC) machining utilizes computer-controlled cutting tools to remove material from a solid block or billet, resulting in highly accurate prototype molds. CNC machining is suitable for producing prototypes from a wide range of materials, including metals, plastics, and composites. Silicone Molding: Silicone molding, also known as rapid tooling or soft tooling, involves creating a silicone mold directly from a master pattern or 3D-printed model. This flexible and cost-effective method allows for producing small-batch prototypes with intricate details and fine surface finishes. Mass Production Mold-Making Services Mass production molds are designed for high-volume manufacturing, allowing businesses to replicate products consistently and efficiently on a large scale. These molds are engineered to withstand continuous production demands while maintaining tight tolerances and dimensional accuracy. Characteristics Mass-production molds are characterized by their durability, precision, and suitability for high-volume production. Key features of mass-production molds include: Durability: Mass-production molds are typically constructed from robust materials such as hardened steel or aluminum to withstand the rigors of prolonged use and repeated molding cycles without experiencing excessive wear or degradation. Precision: Mass production molds are engineered with precision-machined cavities and cores to ensure uniformity and consistency in the molded parts. Tight tolerances are maintained to meet the strict quality standards required for mass-produced components. High-Volume Capability: Mass production molds are optimized for rapid cycle times and efficient material utilization, allowing for producing large quantities of parts within a short timeframe. This scalability makes them ideal for industries with high demand and production volumes. Process and Technologies Mass production molds leverage advanced manufacturing processes and technologies to achieve high productivity and cost efficiency. Some commonly used techniques include: Injection Molding: Injection molding is a versatile manufacturing process that involves injecting molten material (such as plastic resin) into a mold cavity under high pressure. This process allows for the rapid production of large quantities of complex parts with consistent quality and precise details. Die Casting: Die casting is a metal casting process that involves forcing molten metal into a reusable steel mold (called a die) under high pressure. Die casting is well-suited for producing intricate metal parts with excellent surface finish
Exploring Aluminum Cast Parts: Manufacturing,Applications,and Advantages
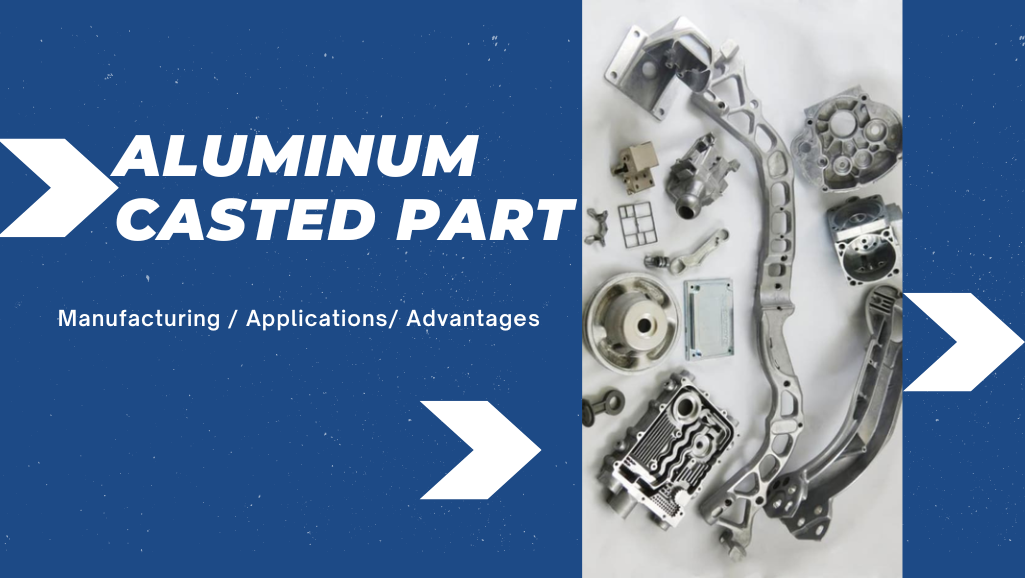
Blog Details Aluminum cast parts play a pivotal role in various industries, owing to their versatility and reliability in manufacturing processes. This article delves into the intricacies of aluminum cast parts, encompassing their manufacturing techniques, diverse applications, and the inherent advantages they offer. Techniques of Aluminum Cast Parts Production Aluminum cast parts are manufactured through several sophisticated techniques, each carefully selected based on factors such as the complexity of the part, required precision, and volume of production. Below, we delve into the intricacies of these techniques: Die Casting Die casting is a highly efficient and precise method used in the mass production of aluminum cast parts. It involves injecting molten aluminum into a steel mold, also known as a die, under high pressure. The die is typically composed of two halves, allowing for the creation of intricate shapes and features with excellent dimensional accuracy. Die casting offers rapid cycle times, making it ideal for high-volume manufacturing. Gravity Casting Gravity casting, also called permanent mold casting, relies on gravity to fill a reusable mold cavity with molten aluminum. Unlike die casting, gravity casting does not involve high-pressure injection, resulting in a slower filling process. However, this method is well-suited for producing larger, thicker parts with minimal porosity. Gravity-casting molds are typically made from materials such as steel or cast iron, offering durability for repeated use. Sand Casting Sand casting is a versatile and cost-effective technique for producing aluminum cast parts, particularly those with complex geometries and low to medium production volumes. In sand casting, a pattern of the desired part is pressed into a sand mixture, creating a mold cavity. Molten aluminum is then poured into the mold, where it solidifies to form the final part. Sand casting allows for flexibility in design iterations and is suitable for both small and large components. Investment Casting Investment casting, also known as lost-wax casting, is employed to create aluminum cast parts with intricate details and fine surface finishes. This technique begins with the creation of a wax pattern, which is coated with a ceramic shell to form the mold. The wax is then melted or “lost” from the mold, leaving behind a hollow cavity into which molten aluminum is poured. Investment casting is favored for its ability to produce complex shapes with minimal machining required, making it ideal for high-value components in aerospace and automotive applications. Centrifugal Casting Centrifugal casting utilizes centrifugal force to distribute molten aluminum evenly within a spinning mold. This technique is particularly well-suited for producing cylindrical or symmetrical parts, such as pipes, tubes, and cylindrical sleeves. By controlling the rotation speed and the aluminum pouring rate, manufacturers can achieve uniform wall thickness and superior metallurgical properties in the final castings. Each aluminum cast parts production technique offers distinct advantages and limitations, catering to a wide range of applications and manufacturing requirements. Whether it’s die casting for high-volume production, sand casting for complex geometries, or investment casting for intricate details, manufacturers have a variety of options at their disposal to create aluminum cast parts that meet the stringent demands of modern industry. Applications of Aluminum Cast Parts Aluminum cast parts find extensive use across diverse industries owing to their lightweight nature, excellent mechanical properties, and versatility in manufacturing. Let’s explore some of the key applications in which aluminum castings play a crucial role: Automotive Industry In the automotive sector, aluminum cast parts are integral to achieving lightweight designs, improving fuel efficiency, and enhancing overall vehicle performance. Engine components such as cylinder heads, engine blocks, and intake manifolds are commonly produced using aluminum castings. These parts offer high strength-to-weight ratios, enabling automakers to reduce vehicle weight without sacrificing structural integrity. Additionally, aluminum castings are utilized in transmission housings, suspension components, and structural reinforcements, contributing to enhanced durability and crashworthiness. Aerospace Sector Aluminum cast parts play a vital role in the aerospace industry, where the demand for lightweight materials and precision engineering is paramount. Aircraft manufacturers rely on aluminum castings for structural components, engine parts, and critical assemblies. Wing ribs, fuselage frames, and landing gear components are often produced using aluminum castings due to their exceptional strength-to-weight ratios and resistance to fatigue. Furthermore, aluminum’s corrosion resistance ensures longevity and reliability in harsh aerospace environments, making it a preferred choice for both commercial and military aircraft applications. Electronics and Consumer Goods In the electronics and consumer goods sectors, aluminum cast parts serve various purposes, ranging from heat dissipation to structural support. Electronic devices such as smartphones, laptops, and tablets incorporate aluminum castings in their chassis and heat sinks to dissipate heat generated during operation efficiently. The lightweight and malleable nature of aluminum allows for intricate designs and compact form factors, facilitating sleek and stylish product designs. Additionally, aluminum castings are utilized in household appliances, power tools, and recreational equipment, where durability and aesthetics are essential considerations. Industrial Machinery and Equipment Aluminum cast parts are widely used in industrial machinery and equipment, contributing to enhanced performance, reliability, and cost-effectiveness. Industrial pumps, valves, and hydraulic components often utilize aluminum castings due to their corrosion resistance and ability to withstand high-pressure applications. Furthermore, aluminum castings are employed in manufacturing equipment such as die-casting machines, extruders, and injection molding tools, where precision engineering and dimensional stability are critical for achieving consistent production outputs. Renewable Energy Systems Aluminum cast parts play a crucial role in renewable energy systems such as wind turbines, solar panels, and hydroelectric generators. Wind turbine components such as rotor hubs, nacelle frames, and tower sections utilize aluminum castings to reduce overall weight and improve energy efficiency. Similarly, solar panel frames and mounting structures benefit from aluminum castings’ lightweight and corrosion-resistant properties, ensuring long-term reliability and performance in diverse environmental conditions. Additionally, aluminum castings are utilized in hydroelectric power generation equipment such as turbine housings and impellers, where they offer high strength and durability in water-intensive environments. The applications of aluminum cast parts span across a wide range of industries, encompassing automotive, aerospace, electronics, industrial machinery, renewable energy, and beyond. Their lightweight nature, exceptional