Exploring Which Metals Can be Anodized
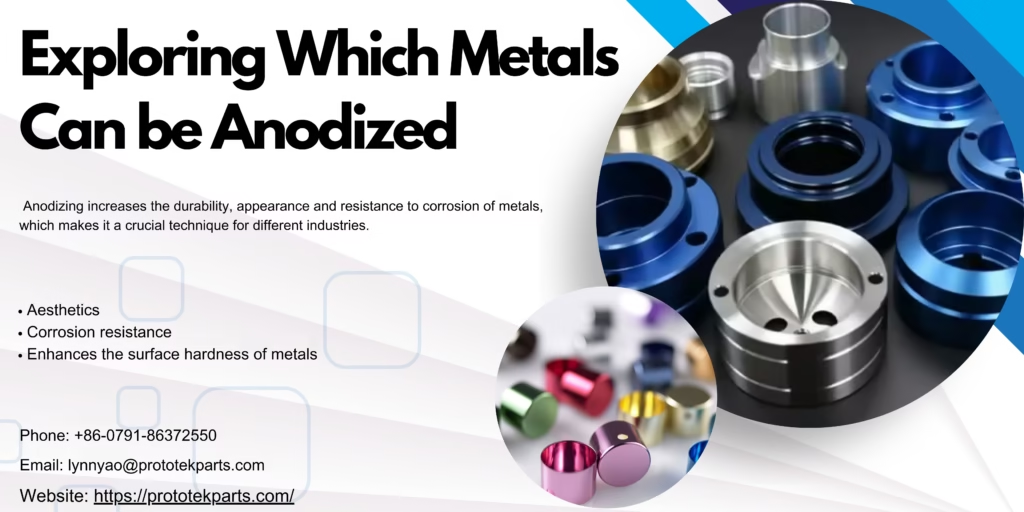
Exploring Which Metals Can be Anodized In this informative article, we’ll explore which metals are anodized and the reasons for it. Anodizing increases the durability, appearance and resistance to corrosion of metals, which makes it a crucial technique for different industries. In the case of anodizing, not all materials are made equally. Certain metals, for instance titanium and aluminum, are often anodized because of their outstanding anodizing capabilities. They create a protective oxide coating on their surface of the metal during the process of anodizing, providing an additional layer of protection from chemical wear and weathering. If you are aware of the basics of anodizing and the kinds of metals suitable for this process, you can make informed choices on the right metal for your project. You may be a designer or engineer, or just interested in the field of finishing metals this guide will provide you with the necessary information to be able to use the process efficiently. So, prepare to enter the anodizing world to find out which metals can undergo this transformational process. Let’s find out which metals are anodized and the reasons they’re so suitable to it. What is anodizing? The process of anodizing involves an electrochemical method that converts the surface of the metal to create a strong and rust-proof layer. The process involves primarily the oxidation of the material and an oxide-like layer is created on the surface. This process makes use of an electrolyte solution as well as electricity to produce a protective layer that is much thicker than the normal oxide layer that is formed on the majority of metals. The anodized surface that results can be both functional and attractive and offers a variety of benefits that boost the efficiency of metal. The anodizing process begins with cleaning the metal surface to remove any contaminants or oils that could interfere with the formation of the oxide layer. Once the surface is prepped, the metal is submerged in an electrolyte bath, typically composed of sulfuric acid, and connected to the positive terminal of a power supply. The negative terminal is connected to a cathode, often made of lead or stainless steel. When current flows through the solution, oxygen ions are released at the anode (the metal piece), leading to the growth of the oxide layer. One of the key advantages of anodizing is its applicability to various metals, especially those that naturally develop a protective oxide layer, such as aluminum and titanium. Unlike a simple coating, the anodized layer is an integral part of the metal’s surface, offering enhanced hardness and wear resistance, as well as the ability to absorb dyes for aesthetic purposes. This transformative process has become essential in many industries, from aerospace to consumer goods, due to its versatility and effectiveness. Why is anodizing important for metals? Anodizing is an integral process that improves metals for various uses. One primary advantage is anodizing’s ability to enhance corrosion resistance; metals like aluminum and titanium that naturally resist corrosion can reap significant rewards by anodizing. Anodization forms an oxide layer that acts as an excellent barrier against moisture, chemicals, and environmental pollutants, protecting underlying metal from deterioration over time – something especially valuable in industries where components may be exposed to harsh environments. Anodizing metals not only increase corrosion resistance but also harden their surfaces by increasing surface hardness; anodized layers may even become much harder than their base metal, leading to improved wear resistance in applications that involve friction or abrasion such as automotive and aerospace components. Furthermore, anodizing reduces friction coefficient making it an excellent surface treatment choice for components interacting with other materials. Anodizing offers aesthetic advantages as well, enabling a variety of colors and finishes. Due to its porous surface, anodized layers absorb dyes that produce vivid, long-term colors without chipping or peeling like traditional paints or coatings would. This is particularly advantageous in decorative applications like architectural elements, consumer electronics and sporting equipment where appearance plays an integral role in functionality – an important advantage when aesthetics is just as essential as functionality in modern manufacturing processes. Anodizing therefore not only improves the performance of metals but also adds visual appeal, making anodizing an integral process in modern manufacturing practices – an indispensable step that plays its part in modern manufacturing practices! Metals that can be anodized While anodizing is most commonly associated with aluminum, other metals can also undergo this process to enhance their properties. It is important to understand which metals can be anodized to select the right materials for specific applications. The most notable metals that can be anodized include aluminum, titanium, magnesium, and others. Each of these metals possesses unique properties that make them suitable candidates for anodizing. Aluminum is one of the most frequently anodized metals due to its lightweight nature, excellent corrosion resistance and ability to form an oxide protective layer. Anodizing further bolsters these characteristics, making aluminum suitable for applications ranging from aerospace components to architectural finishes. Its versatility provides endless color and texture choices extending its applicability in design and engineering applications. Titanium metal can benefit from anodization in several industries, particularly medical and aerospace applications. An anodized layer on titanium not only improves its corrosion resistance but also increases biocompatibility making it perfect for medical implants and devices. Furthermore, anodization creates vibrant colors on titanium surfaces which can serve aesthetic purposes or signal different levels of surface treatment. Magnesium, while less frequently anodized than aluminum or titanium, can still undergo the anodizing process to increase corrosion resistance for applications that focus on weight savings, such as automotive and aerospace sectors. Other metals like zinc may also undergo this process with different processes and outcomes depending on each metal; understanding how anodizing characteristics differ between metals is vital for engineers and manufacturers looking to maximize product performance. Aluminum anodizing process The aluminum anodizing process is a well-established technique that involves several key steps to ensure a high-quality anodized finish. Initially, the aluminum surface undergoes a thorough cleaning process to remove any contaminants such as dirt, grease, or existing oxide layers. This is