Blog Details
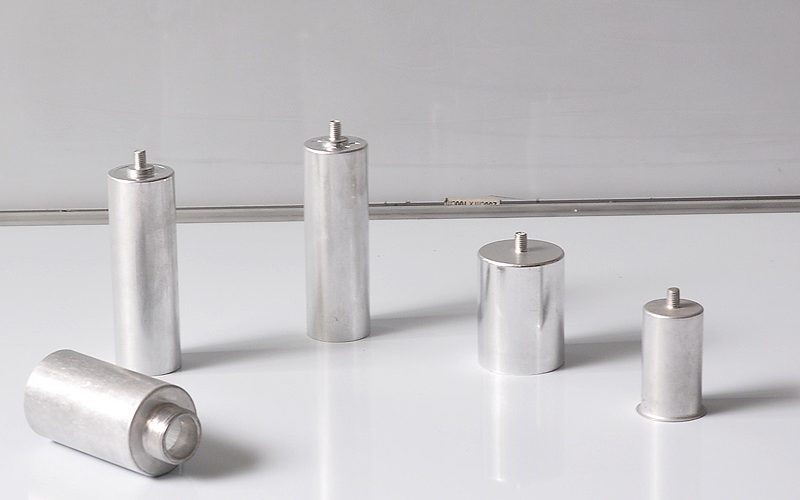
Advantages Of Cold Extrusion Process
Cold extrusion is to put the metal blank in the cold extrusion cavity, at room temperature, through the press fixed punch to apply pressure to the blank, so that the metal blank to produce plastic deformation and parts processing method.
China has been able to cold extrusion of lead, tin, aluminum, copper, zinc and their alloys, low carbon steel, medium carbon steel, tool steel, low alloy steel, and stainless steel, and even bearing steel, high carbon and high aluminum alloy tool steel, high-speed steel, and other metals can be cold extrusion of a certain amount of deformation.In extrusion equipment, our country has the ability to design and manufacture extrusion presses.
In addition to the general mechanical press, hydraulic press, cold extrusion press, friction press,, and high-speed high-energy equipment have been successfully used for hard extrusion production.
Define
Extrusion is a process that forces the gold chips to produce plastic flow through the gap between the punch and the die or the die outlet to make the hollow parts or the parts whose section is smaller than the blank section.If the blank is extruded without heat, it is called cold extrusion.Cold extrusion is one of the processing technology of no chip and less chip parts, so it is an advanced technology in the plastic processing of gold chips. If the blank is pressed by heating it to a temperature below the recrystallization temperature, it is called warm extrusion. Warm extrusion still has the advantage of fewer chips.
Advantages
- Accurate sizing
The general dimension accuracy of cold extruded parts developed in our country is up to 8 ~ 9 grades. If ideal lubrication is used, it is second only to the fine polishing surface. Therefore, parts manufactured by the cold extrusion method generally do not need to be reworked, and a small number only need to be finished (grinding). Save materials.
- Save materials
The utilization rate of cold extruded materials can usually reach more than 80%. Such as the Jiefang brand automobile piston pin dynamic cutting material utilization rate of 43.3%, and with cold extrusion material utilization rate increased to 92%; For example, after the universal joint bearing sleeve is changed to cold extrusion, the material utilization rate is increased from 27.8% to 64%. It can be seen that the cold extrusion method can save a lot of steel and non-ferrous metal materials in the production of machine parts
- High production efficiency
The efficiency of producing mechanical parts by cold extrusion is very high, especially in the production of large batch parts. The production by cold extrusion is several times, dozens of times, or even hundreds of times as compared with cutting. For example, cold-extruded piston pins for automobiles are 3.2 times more productive than machined ones, and cold-extruded piston pin automatons are now used to further increase productivity. The productivity of one cold extrusion automaton is equivalent to that of 100 regular lathes or 10 four-spindle automatic lathes.
- Wide application
Such as special-shaped sections, internal teeth, special-shaped holes, and blind holes, These parts are difficult to complete by other processing methods, but it is very convenient to process with cold extrusion.
- High strength
Because the cold extrusion adopts the cold deformation strengthening characteristic of metal materials, that is, the metal blank is in the state of three-way compressive stress during the extrusion process, and the material is compact and has continuous fiber flow direction after deformation, so the strength of the parts is greatly improved. In this way, low-strength materials can be used instead of high-strength materials. For example, in the past, 20Cr steel was used to manufacture liberation brand piston pins by cutting. Now, 20 steel is used to manufacture piston pins by cold extrusion. After the performance test, the cold extrusion method is higher than the cutting method to manufacture piston pins.
If you have any needs for cold extrusion, ple feel free to contact Prototek,
Tags:
- cold extrusion, cold impact